THOUGHT LEADERSHIP
Decommissioning battery energy storage systems: It’s never too early to plan for retirement
All good things come to an end – even big battery energy storage systems (BESS). In Australia, the end of life for BESS may feel very distant, since we’re really only in the infancy of the booming BESS industry; however, the life expectancy of these big batteries is nothing like the design life of other renewable energy and storage technologies. With BESS currently only lasting for around 10 to 15 years of operation, developers and owners of BESS installations need to be thinking and planning now for what decommissioning will involve and what it will cost. In fact, planning for decommissioning is best done right from the start – long before the project is constructed.
Here, one of Entura’s BESS specialists, Dr Rahmat Khezri, answers some burning questions about the end stages of a BESS project.
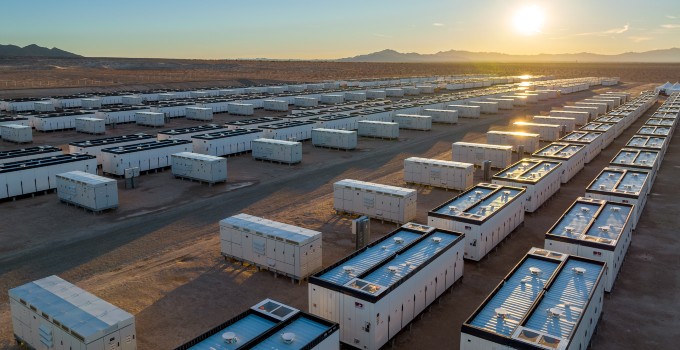
- When does the life of a BESS project come to an end?
The need to decommission a BESS project could arise either from the conclusion of a contract or power purchase agreement – though this is unlikely – or from the expiration of the battery’s operational lifespan. This could be when the battery capacity has degraded to a point where it is no longer financially viable to operate in the market or when the battery’s internal chemistry has reached a point where it is unsafe to continue operating.
For nickel-manganese-cobalt (NMC) batteries, which held a significant share of batteries before lithium-iron-phosphate (LFP) batteries entered the market, this could be after 3,000 to 7,000 cycles at 80% depth of discharge (DoD) or around 10 to 15 years. For LFP batteries, which are gradually dominating the battery market for BESS, it’s around 4,000 to 10,000 cycles or 15 to 20 years. However, several factors can either reduce or extend the battery lifespan. Higher DoD shortens battery life, and frequent high-power cycling (e.g. for frequency control ancillary services, FCAS) can accelerate degradation. Avoiding prolonged high or low state-of-charge management (SoC) reduces degradation. Temperature is also an issue – so proper cooling and heating systems can support greater longevity.
- Is decommissioning the only option?
Full decommissioning of aging BESS assets is not always necessary at battery end of life, as some key components – such as inverters, transformers and balance of plant (PoP) – often retain residual service life. There may be opportunities for repowering or augmentation instead, which will require a much lower level of decommissioning activities. Repowering replaces old batteries with newer or upgraded technology to restore or enhance performance. Augmentation generally aims to increase capacity or power output by expanding the system with additional capacity, for example by adding extra battery racks to an existing setup.
- What does a full BESS decommissioning program involve?
A typical full BESS decommissioning program includes the following activities:
- developing the decommissioning plan including a risk assessment
- de-energising the BESS
- removing power conversion systems (inverter/transformer stations)
- removing integrated battery storage units (site dismantling and packaging may be required)
- shipping the packed battery storage units to recycling facilities
- removing electrical cables and conduits
- removing substation equipment
- shipping the power conversion systems and cables to recyclers of electronic waste
- transporting non-recyclable material removed from the site to disposal facilities
- restoring the site.
- How long could BESS decommissioning take?
Once a BESS project stops operating, the decommissioning process can begin (usually within 12 months) and can take around 6 to 9 months. Of course, this will depend on the scale of the BESS project, which will determine the amount of battery units and electrical infrastructure that will need to be removed from the site. If site restoration is required, this could extend the timeframe.
- What might BESS decommissioning cost?
Decommissioning costs are made up of labour, equipment, transport, materials, and recycling or disposal. These costs can be categorised across the stages of the project: removing the BESS facilities, restoring the site, packaging and transport, and the cost of recycling or disposal. If it is possible to achieve some value from salvage, this can be offset against the decommissioning costs. Currently the total recycling fee for high-powered batteries is around $10–15 per kg. Assuming approximately 6 kg for 1 kWh, the recycling cost would be $60–90 per kWh.
- Talking about recycling, what are the options for decommissioning BESS sustainably?
In Australia, we’re still in the early days of developing a lithium battery recycling industry – but we are seeing increasing recognition by owners, developers, regulators and the community of the need for the renewable energy industry to strengthen the circular economy and minimise landfill. Battery modules are recyclable – but salvage and reuse are likely to remain very dynamic and the future market for used lithium-ion modules remains uncertain. We recommend that every BESS developer/owner should aim to maximise recycling and develop as sustainable a waste management plan as possible. It is worth noting that recycling and reuse of inverters, transformers and BoP components are well established and available.
- What regulatory requirements are there in Australia for BESS decommissioning, and how do you envisage this changing?
In Australia, BESS projects must comply with relevant environmental regulations, which vary by state but generally align with the environmental protection guidelines set by each state’s Environment Protection Authority (EPA). At the federal level, the Product Stewardship Act 2011 promotes the responsible management of products at the end of their life cycle, including batteries. Decommissioned components from BESS projects, particularly lithium-ion batteries, are typically classified as prescribed industrial waste (PIW), requiring handling by licensed transporters and disposal at approved facilities.
At this stage the permitting process to build a BESS facility does not require a formal plan for decommissioning and disposal – but it is probably only a matter of time until we see more stringent requirements as part of the development application process. Despite a detailed plan not yet being required, it is definitely worthwhile doing, not least because the costs of decommissioning should be factored into the business case from the outset.
- What lessons have been learned from international examples of BESS decommissioning?
There haven’t been many examples of BESS decommissioning in our region yet, but the example of decommissioning the Tehachapi Energy Storage Project (TSP) project in South California in 2022 is an instructive real-life case study. This 8 MW / 32 MWh lithium-ion battery project was one of world’s first and largest BESS when it was commissioned in 2014. It had a footprint of 585 m2, with 604 battery racks and two 40-foot PCS containers. The decommissioning was completed in just over 4 months from the generation of the purchase order to the finish.
A key takeaway from this case study is the significant impact that logistical and site-specific constraints can have on project outcomes. Although the PCS containers were initially expected to be removed within a single day, unforeseen space limitations and permitting restrictions ruled out the use of cranes. As a result, the containers had to be dismantled and cut into sections on-site. This increased the schedule by 17% and the cost by 20%. The lesson here is clear: success lies in the details, particularly when it comes to transport and access logistics. Thorough, site-specific planning is essential to avoid unexpected delays and budget overruns.
- What should Australian BESS developers and owners be doing now about decommissioning?
Ideally, every player in the BESS industry in Australia should be thinking ahead, however far off BESS decommissioning, repowering or augmentation may seem right now. It is never too early to start investigating the potential options, costs, timing, emissions, challenges and solutions – and developing a plan that can continue to evolve as the industry matures. A robust decommissioning plan will also be a valuable input into the technical due diligence process for sale/purchase. Ultimately, solid, early planning is the key to minimising risk and maximising value – and achieving a more efficient, more cost-effective and more sustainable outcome for any BESS project.
At Entura, we’ve been involved with BESS since the very start of the sector in Australia, and we’re always learning from our experiences here and around the world. We’re actively developing our analyses of decommissioning costs, transport, timing and circularity opportunities so that we can support your BESS project holistically, from cradle to grave.
Regardless of the stage of your BESS project, Entura can help. Contact Patrick Pease to find out how.
About the author
Senior Renewable Energy and BESS Engineer Dr Rahmat Khezri has vast professional and technical experience with batteries. He has worked in the renewable energy and battery industry in project delivery from BESS design, business case and feasibility analysis to operation and construction. Rahmat has managed several utility-scale BESS projects during his time with Entura, overseeing successful delivery while ensuring compliance with industry standards, optimising performance, and managing key stakeholder relationships. Before joining Entura, he worked on projects supported by Sustainability Victoria for technical design and business case development of ‘second-life BESS’ using retired batteries of electric vehicles. In 2023 and 2024, he was recognised by Stanford University as being in the top 2% of scientists worldwide for two consecutive years.
12 May, 2025