THOUGHT LEADERSHIP
New technologies are important tools, but they need to be used properly
Entura’s Technical Director (Water), Richard Herweynen, recently attended the 2025 ICOLD Congress in Chengdu, China, themed ‘Common Challenges, Shared Future, Better Dams’. Here he shares his observations on the state of play in the international dams industry – and the opportunities emerging with artificial intelligence and automation.
My first ICOLD Congress was in Beijing, China in 2000. I was presenting some finite element analysis work that I had done on Gordon Dam, a 140m-high concrete arch dam in Tasmania. The analysis was being used to help predict and explain some cracks that had formed at the base of the downstream face of the concrete shell, roughly normal to the foundation, during first filling. In the 1980s, an attempt had been made to model the crack using finite element modelling, but with little success due to the coarseness of the mesh. However, by the late 1990s, computing power had increased and finite element programs had improved, providing the capability to construct more detailed finite element models, which were able to predict and explain the cracking that had occurred.
Dr Sergio Giudici, the designer of Gordon Dam, was my mentor on this finite element analysis, and he reinforced these principles:
- It is important to verify the input data to make sure the model represents, as well as possible, the actual dam parameters.
- Results should be validated using alternative techniques to give the engineer confidence in the results that the model is producing (i.e. structural hand calculations still have a place).
- Complexity should be built into these models only gradually, so that the engineer can see the impact of changes and determine whether they are reasonable.
These same principles are true for many complex engineering models and when setting up calculation spreadsheets or similar.
Now, 25 years on, I have had the privilege of attending the 2025 ICOLD Congress in Chengdu, China. At this Congress, there was much talk about the importance of dams in society for water security, the growing role dams and reservoirs play in providing resilience to climate change and the energy transition, the importance of balancing economic benefits and environmental needs, and – in all of this – the importance of ensuring that our dams are safe for communities downstream.
We have discussed many of these themes before – and they remain highly important; however, one thing I took away from ICOLD 2025 in particular was how China is embracing technology and advancing a ‘Smart Dam’ initiative.
New technologies and smarter dams
One could say that our industry has always been building smart dams, but China’s ‘Smart Dam’ concept is about using the full power of current technologies to construct, monitor and operate dams in smarter ways, and to use technologies to predict and adapt to changing conditions.
The CHINCOLD Workshop on Digital and Intelligent Technologies for Dam Construction, Operation and Maintenance, which occurred during ICOLD 2025, gave a glimpse of what may be possible.
Many projects utilise 3-dimensional digital models and building information modelling (BIM). However, the concept of having a digital twin of the dam, replicating every aspect of the physical dam in a digital form, opens the door to many possibilities, especially in light of the advent of artificial intelligence (AI).
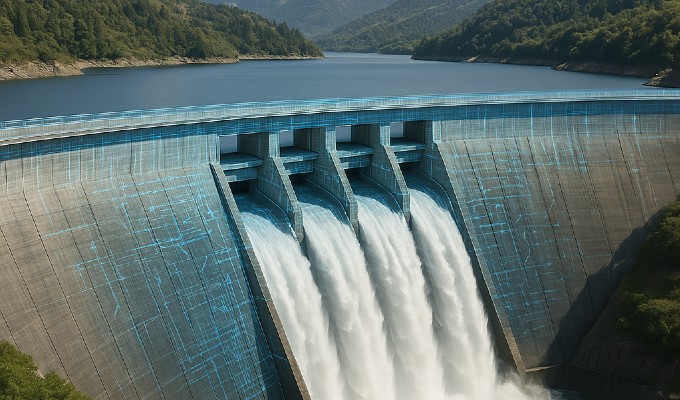
Artificial intelligence and machine learning
Many organisations and nations have been cautious about AI, but China is increasingly adopting it to improve construction practices in dam engineering, improve monitoring and surveillance of dams, and to help adapt to extreme events as they occur.
Machine learning (ML), an element of AI, enables computers to learn from data without being explicitly programmed. ML algorithms analyse data, identify patterns, and make predictions or decisions, improving their performance over time and with more data. There are no doubt many engineering applications where ML could be used to help improve predictive modelling or optimisation, and to make these more efficient. However, the same principles that were important when we were beginning to embrace larger, more refined finite element models with the advent of faster computing remain true here:
- We must verify the input data that machine learning is utilising to ensure we don’t get ‘garbage in equals garbage out’.
- Results need to be validated. AI needs to be trained correctly, and we need experts involved at this stage to ensure that the outputs from AI are correct.
- Complexity, or the full power of technology, should be added incrementally, to provide progressive confidence in the outcomes.
Engineering is the application of science, and therefore it is critical for every engineer to understand the fundamental principles and how to apply them. The complex computer programs used for a lot of engineering modelling can become ‘black boxes’, and practitioners risk diluting or losing their understanding of the fundamental principles behind the models, and hence their ability to validate the results.
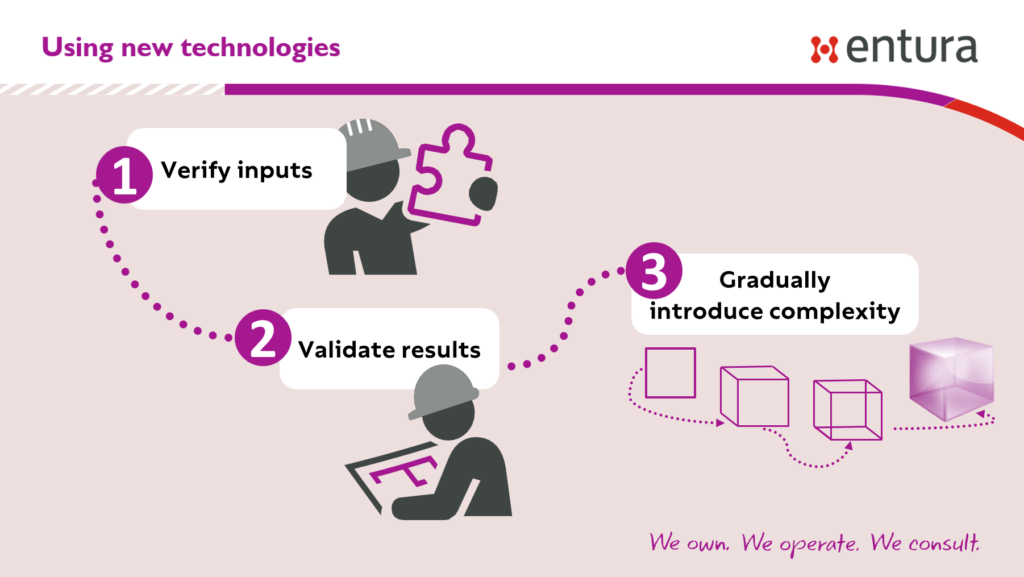
Automation brings a step change in efficiency and accuracy
At the ICOLD Congress in 2000, I co-authored a paper for the international symposium on concrete-faced rockfill dams (CFRD) entitled ‘Hydro Tasmania experience in concrete-faced rockfill dams – past, present and future’. There is no doubt that Hydro Tasmania has a strong history in CFRD, with Cethana Dam playing an important role in the development of the modern, high CFRD.
In 2000, however, the future in CFRD that we envisaged did not include unmanned construction equipment with automatic quality control feedback loops. At the 2025 CHINCOLD Workshop on Digital and Intelligent Technologies for Dam Construction, Operation and Maintenance, a presentation was given by Wang Jiajun from Tianjin University on intelligent unmanned roller systems to compact rockfill dams. Unmanned rolling compaction (URC) systems involve three core technology modules: (1) intelligent perception, (2) autonomous planning and decision making, and (3) intelligent control. These systems use automated driving technology to control the rolling process on earth and rockfill dams, improving productivity and quality. They can accurately control compaction parameters such as passes, speed, vibration and lift thickness. URC systems also enable continuous monitoring and real-time feedback for quality control, reducing human error and improving overall project performance. This automated technology was used on the 295m-high, 1.57km-long Lianghekou hydropower dam in China, with a total fill volume of 43 million m3.
The changing face of dam engineering
With AI and automation, the scope for embracing new technology in dam engineering is growing fast. It is clear that there are significant benefits that could be realised for dam design, construction, operation, dam safety and emergency response – and there’s a role for these advanced technologies at all of the stages of the life cycle of a dam. A degree of caution is appropriate and necessary, but caution should not be a reason to refuse to engage with the new technologies available to our industry.
However, with more sophisticated models – such as digital twins – being created of our dams, it is important to ensure we maintain the guiding engineering principles of verifying input data, validating models for correctness, and building complexity gradually. By doing this, we can provide the necessary assurance and confidence in our increasingly sophisticated and evolving tools.
ABOUT THE AUTHOR
Richard Herweynen is Entura’s Technical Director – Water. He has more than three decades of experience in dam and hydropower engineering, working throughout the Indo-Pacific region on both dam and hydropower projects. His experience covers all aspects including investigations, feasibility studies, detailed design, construction liaison, operation and maintenance and risk assessment for both new and existing projects. Richard has been part of a number of recent expert review panels for major water projects. He participated in the ANCOLD working group for concrete gravity dams and was the Chairman of the ICOLD technical committee on engineering activities in the planning process for water resources projects. Richard has won many engineering excellence and innovation awards (including Engineers Australia’s Professional Engineer of the Year 2012 – Tasmanian Division), and has published more than 30 technical papers on dam engineering.
25 June, 2025