THOUGHT LEADERSHIP
Planning for the future – the challenges of dam inspection and maintenance
No dam is ‘maintenance free’. Without appropriate maintenance and refurbishment at the right times, a dam may not be able to fulfil its function safely for the full length of its design life (which could be more than a century).
This presents many challenges for asset owners. To keep the dam operating as the designer intended – and get the most out of the original investment over the long term – owners will need to develop and implement a suitable operations and maintenance manual aligned with the asset management plan and reflecting a ‘whole of life’ strategy. These plans will need to consider the unique characteristics of each dam and cover all the relevant issues. And there are many!
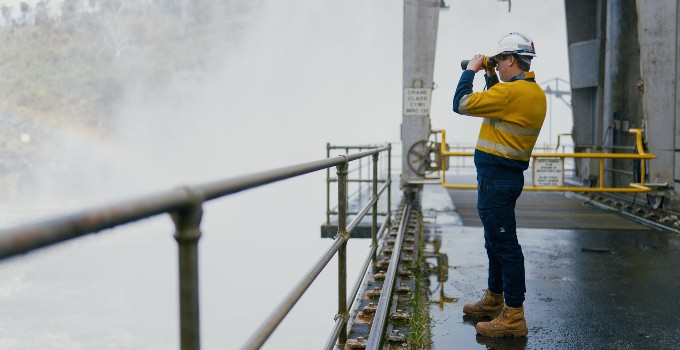
Dams consist of a number of different elements. There are the main civil engineering components including the wall that holds back the water and the spillway – but there could also be mechanical elements (pipework, valves and gates) and electrical elements (power supply to lights, valves, gate motors and control systems). Each of these elements will have its own operational and maintenance requirements and different lifecycle duration. Ideally, all this detail needs to be captured in the operation and maintenance manual (as recommended by ANCOLD guidelines) and in an asset management plan.
Civil components
The civil components of dams have the longest life span, typically more than 100 years if well constructed and maintained. Common maintenance items that need to be regularly addressed include:
- Vegetation management
Trees and bushes will readily grow in earthfill and rockfill embankments. Regular control (e.g. annually) is necessary to ensure that roots don’t grow through the fill and initiate leaks through the embankment. Mowing the grass on the downstream face of the earthfill embankment and downstream contact is necessary so that the condition of the face can be observed. Even concrete gravity and concrete arch dams will require vegetation control along the downstream face contact with the foundation so that the dam can be easily viewed in routine inspections.
- Surface water drainage
Dam construction typically affects natural drainage lines, which is why surface water drains are a common feature around and on dams – such as along the groins (where the dam wall intersects with natural ground), along berms in embankment dams, along benches, at the top of cuttings, and along access tracks. Drains will need regular inspection for both erosion and blockage due to sediment or vegetation.
- Foundation drain cleaning
Concrete gravity dams and concrete arch dams typically have drains drilled into the rock foundations to relieve uplift pressures and help maintain stability of the wall. Over time, silt or iron-rich slime can build up as a byproduct of bacterial growth in the drains, reducing effectiveness. These drains typically require 5-yearly high-pressure flushing. Cleaning will also be needed for drains underneath spillways founded on rock and cut slopes in rock.
- Protection of the dam safety monitoring system
Protecting the dam safety monitoring system requires a range of regular activities. These include cleaning and clearing vee-notch seepage monitoring weirs, checking survey monitoring pillars and targets, and checking the calibration of level monitoring and indication devices, such as reservoir-level sensors, piezometers, tiltmeters and inclinometers. Regular functional testing will also need to be carried out on the alarming and tripping devices that form the primary protection elements of the dam, including spillway gates and scour valves.
- Clearing of trash racks
Outlet works usually have trash racks to stop debris entering the pipework and causing blockages. It’s important to check that the build-up of debris is tolerable and that any hydraulic losses won’t affect operations. Assessing and removing the debris isn’t easy, as the trash racks are often accessible only by remotely operated vehicles (ROVs) or by divers. Before the inspection, the outlet will typically need to be closed and isolated.
Inspection-driven longer term maintenance will also be required for particular elements of the dam, ideally addressing repair items promptly to minimise damage and the cost of future repairs if left untreated. For example, concrete repairs may be needed to address erosion in stilling basins and spillway chutes, or spalling of concrete due to reinforcement corrosion or freeze/thaw damage.
While regular inspections should be undertaken to detect slow deterioration, special inspections following major events – such as floods or earthquakes – should also be part of the operations and maintenance plan. Given that the key areas for inspection are often difficult to access safely, use of UAVs (e.g. to inspect a spillway crest and chute) or ROVs (e.g. to undertake underwater inspections or scanning of stilling basins, plunge pools or riverbed scour) should be considered.
When special inspections identify the need for repairs, the time is right to consider whether the dam’s design or surveillance could be improved to increase resilience for a similar event in future. For example, a higher strength concrete overlay may treat erosion of a spillway chute and increase its resistance to future erosion.
Mechanical components
Mechanical items such as steel or cast-iron pipework can also often last up to 100 years if adequately protected from corrosion. Concrete and cement mortar are very effective for this purpose as the alkaline environment provided by the cement paste provides a very low corrosion environment. Key to the effectiveness of this protection is ensuring that the cement remains in intimate contact with the steel or iron. This will require regular inspections and timely repairs. Where concrete protection is not practical, paint systems can be very effective for up to about 20 years. A suitable inspection regime will be needed so that any areas where the paint has deteriorated can be detected and patched.
Mechanical items such as valves and gates typically have an effective life of around 50 years; however, they need to be exercised regularly to keep them able to work on demand. This is not an issue of the parts wearing out from use; rather, it’s the risk of them seizing due to lack of use. Regular lubrication of bearings, gearboxes and trunnions needs to be included as part of the maintenance of these items. This is particularly important in scour valves and spillway gates that may have a very low frequency of use during normal operations but are there for use in emergencies. The wire ropes commonly used to hoist spillway gates open will need even more frequent replacement, at approximately every 20 years.
Electrical components
Electric motors are commonly used to drive the winches hoisting spillway gates or driving the shafts to open valves. Associated with the motors will be switchboards and power supply systems, typically including grid power supply and backup diesel generators. The typical life of these components is around 25 years. As with the mechanical components, lack of operation can lead to premature failure, so a regular regime of exercise is necessary to ensure maximum reliability and life.
The programable logic controllers (PLC) that are used to automate operations, allow remote operations and generate alarms will have a typical life of only 10–12 years due to changes in programming languages and rapid evolution of the hardware.
Getting the most out of life
As we’ve seen, regular maintenance is fundamental for keeping all the components of a dam operating as intended and maximising their lifespan – whether that’s 10 years or 100. This maintenance, including the exercising of the mechanical and electrical components, needs to be clearly documented in the operations and maintenance manual and recorded in an asset management system. The asset management plan must allow for regular maintenance and also budget appropriately for replacement or refurbishment when any component of the dam is due for retirement.
At Entura, we believe in getting the most out of every piece of infrastructure because that’s good for our clients, communities and the planet. With a solid regime of inspection and maintenance, all the parts of your dam will be on the strongest path to a long, reliable and sustainable life.
If you’d like to talk with us about inspecting and maintaining your dam/s, contact Phil Ellerton, Paul Southcott, or Richard Herweynen.
About the author
Paul Southcott is Entura’s Senior Principal – Dams and Headworks. Paul has an outstanding depth of knowledge and skill developed over more than 3 decades in the fields of civil and dam engineering. He is a highly respected dams specialist and was recognised as Tasmania’s Professional Engineer of the Year in Engineers Australia’s 2021 Engineering Excellence Awards. Paul has contributed to many major dam and hydropower projects in Australia and abroad, including Tasmania’s ‘Battery of the Nation’, the Tarraleah hydropower scheme, Snowy Hydro, and numerous programs of work for water utilities including SeqWater, Sun Water and SAWater. His expertise is a crucial part of Entura’s ongoing support for upgrade and safety works for Hydro Tasmania’s and TasWater’s extensive dams portfolios. Paul is passionate about furthering the engineering profession through knowledge sharing, and has supported many young and emerging engineers through training and mentoring.
30 April, 2025