What to consider when you’re thinking about a synchronous condenser
Depending on when and where you want to connect your new solar farm or wind farm, the network service provider or your consultant may tell you that you’ll need a synchronous condenser. That may not be good news, because these machines don’t come cheap and they usually don’t provide a direct revenue stream. What should you do next?
Do you understand why you need a synchronous condenser?
The first step is to understand why you need the synchronous condenser. The inverters at the heart of most solar farms and most modern wind turbines need a strong electricity grid to push their energy into. If the network is not strong, the inverter is likely to fail to switch at the required times, swing against the power system like a pendulum, and distort the waveform, causing harmonics. The synchronous condenser overcomes this, strengthening the power system in the local area by forcing the network voltage into a near-perfect sine wave of the required size.
The rules have changed!
The burden for providing system strength in Australia’s National Electricity Market has shifted significantly. Previously, new generators bore the primary responsibility under a ‘do no harm’ principle.
As of December 2022, ‘transmission network service providers’ (TNSPs) became ‘system strength service providers’ (SSSPs) and are now responsible for proactively providing a baseline of system strength across their networks.
Furthermore, new connecting parties now face new access standards and ‘system strength mitigation requirements’. This framework offers generators two clear choices to address their system strength impact: (1) pay a system strength charge, which is a fee reflecting the cost for the SSSP to provide the necessary system strength, or (2) self-remediate by installing their own solutions, such as synchronous condensers or grid‑forming inverters, to mitigate their impact.
At Entura, our experience so far indicates that many generators are actively exploring the self‑remediation option, prioritising operating cost over capex for their project.
Self-remediation may mean using synchronous condensers. However, there are also other solutions to system strength, which we’ll discuss below.
Is it possible to predict the need for a synchronous condenser earlier?
There are ways that you can predict at the project pre-feasibility stage that a synchronous condenser might be needed, before the network service provider becomes involved. Take a look at other renewable energy installations that have been constructed recently in the same region; if they needed a synchronous condenser, you almost certainly will too.
Consider where the installation is in the grid. If the answer to any of the following questions is yes, you will likely need a synchronous condenser: Is your installation remote from all traditional generating stations? Has a large traditional generator shut down in the area recently? Are other generators in the area routinely constrained due to network stability challenges?
Simple calculations can be completed based on information that most network service providers publish on their websites, including network constraints and fault levels. These calculations aren’t always definitive, but they will offer significant insight.
What do you need to specify?
It is best to specify the exact function that the synchronous condenser must achieve. Typically, this means specifying the fault current contribution that is required from the machine and leaving it up to the manufacturer to decide the optimal machine design including the headline MVA rating. Once these headline values have been determined, consider the following questions, each of which has a substantial cost impact:
- How much reactive power do you need the synchronous condenser to absorb? Typically these machines can only absorb approximately half of their headline rating, so don’t ask for too much unless you have deep pockets.
- Do you really need inertia that is greater than the manufacturer’s standard? Synchronous condensers are known for having inertia, but asking for inertia that is greater than the manufacturer’s standard will result in substantial additional cost and usually results in no additional revenue stream.
- The synchronous condenser is being installed to provide system strength, so do you really want it to be able to supply reactive power indefinitely? Perhaps 60 seconds would be enough.
- What are the impacts of planned or unplanned outages of the synchronous condenser? Do these impacts warrant increased redundancy or spares retention? We’ll talk about this in more detail below.
Are some cost savings not worth making?
For a synchronous condenser project, there are some measures that, on the surface, might appear to be potential cost-saving considerations. Can you omit the transformer tap changer? Could the cooling equipment be downsized or even omitted? Can you connect to the station 33 kV busbar? Detailed analysis is needed to answer these questions definitively. In our experience, however, the answers to each question have been emphatically no.
If you need the synchronous condenser to operate close to its rated reactive power absorption limit, you’ll need a transformer tap changer. Similarly, if the machine connects to a 33 kV busbar, fault levels will become unreasonable and an even larger machine will be required.
What’s the best contracting model?
Your choice of contracting model will depend on your appetite for risk and the sensitivity of your schedule. A typical solar or wind farm project is very schedule-sensitive, which suits an all-inclusive turnkey project delivery including everything from civil foundations, fencing and drainage through to integration with the farm’s control system. But this delivery mode comes at a price, and there are few Tier-1 equipment suppliers prepared to take on this model. The lowest-cost suppliers will be likely to want to put your machine onto a ship, point it in your general direction, and send you the invoice.
Whatever your contracting model, one of the largest risks to projects is the adequacy of the power system models. You need to be confident that the original equipment manufacturer (OEM) understands the market operator’s model requirements and has the skills to comply with them.
Can the machine offer economic benefits?
Two possible revenue streams could potentially flow from installing a synchronous condenser. By sizing the synchronous condenser to provide the reactive power required from a solar farm by the electricity rules, it is possible to operate the solar inverters and the main transformer at a higher power factor. This has the potential to increase the power output and consequently the revenue from the farm by up to 7%. A proponent could also install an oversized synchronous condenser and sell the spare system-strengthening capacity to another renewable farm in the same region. In the future, inertia and system-strength markets may evolve in ways that provide direct revenue streams for the synchronous condenser.
Redundancy considerations: Is one syncon enough?
Most new generators initially opt for a single, larger synchronous condenser to minimise upfront capital expenditure and ongoing operational expenditure. However, this decision inherently introduces a significant operational risk: the potential for severe output constraint if that sole synchronous condenser becomes unavailable. While synchronous condensers are generally highly reliable, mechanical and electrical failures can occur, and the lead times for repairs or replacement components can be substantial, leading to prolonged outages.
For asset owners considering the future divestment of their renewable energy project, this redundancy factor becomes a critical due diligence item for potential purchasers. A single point of failure for system strength support will be scrutinised. A prospective buyer will likely conduct a far more pessimistic assessment of the probability and duration of generation curtailment due to a synchronous condenser being unavailable, compared with the assessment of the original developer. This increased risk perception can directly and negatively impact the valuation and sale price of the entire energy park.
Is there an alternative?
The inverters at the heart of most solar farms and most modern wind turbines are changing. Until approximately 2023, they exclusively used a technology called ‘grid-following inverters’, but a newer ‘grid-forming inverter’ is breaking into the market. These inverters are more expensive at the moment, but that’s changing rapidly. The newer inverters are much less sensitive to system strength and can typically be operated with the base level of system strength that the TNSP is required to provide. Applications are now emerging in which changing the inverter eliminates the need for a synchronous condenser.
Putting it all together
The most cost-effective projects are often those that link multiple technologies – such as a wind farm with modern wind turbines, static VAr compensators and more than one synchronous condenser. These technologies were not designed to work well together, but with carefully coordinated controls they have done so in practice, providing the required system strength, voltage control and inertia for a successful minimum-cost project.
If you would like to find out more about how Entura can help you overcome electrical challenges for your renewable energy projects, please contact David Wilkey or Patrick Pease.
ABOUT THE AUTHOR
David Wilkey is Entura’s Principal Consultant, Secondary Electrical Engineering. He has more than 25 years of consulting experience in electrical engineering across Australia and New Zealand, focusing on the delivery of advisory on secondary systems and power systems engineering. David’s expertise spans all areas of electrical engineering with a particular focus on electrical protection, power system studies and rotating electrical machines.
MORE THOUGHT LEADERSHIP ARTICLES
Renewables in remote mines – a litmus test for the wider renewables transition
Entura’s Greg Koppens has recently returned from the Energy and Mines Summit in Perth, where he led the ‘Think Tank’: a collaborative session addressing the challenge of powering process steam requirements from renewables-generated electricity. Here he shares his observations on the rise of renewables in the mining industry …
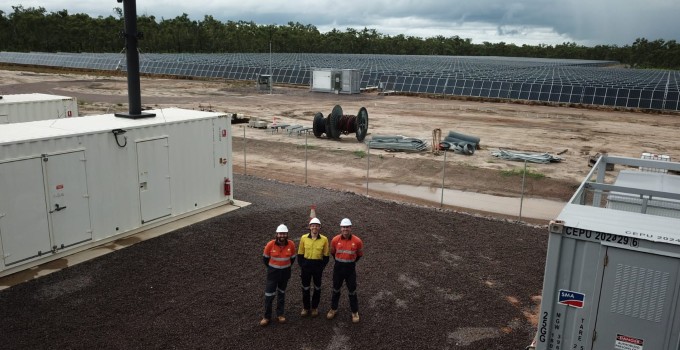
Australia’s mining industry is beginning the peak phase of its energy revolution. However, I find it unfortunate that this exciting fact is invisible to regular people. It is happening in remote areas on mining leases, inaccessible to the public. Each project alone is not sensational enough for media attention, but added together these projects are nothing short of a technology revolution. For remote mining sites to have a solar farm is now standard practice. In many cases this is backed up by battery storage and a handful of mines have onsite wind turbines.
The past: fossil-fuel driven mines
Australia is world-renowned for our mining industries, with mines of virtually every resource throughout our country. Up until about ten years ago, nearly all of Australia’s mines ran completely on diesel or gas. In most cases diesel was trucked in, or gas was brought in via pipeline. Most of these mines have energy expenses in the tens of millions of dollars per year. A small change in the oil price can drastically impact the mine’s bottom line.
If there’s one doubtless fact about mining, it’s that miners are practical people. They are problem solvers, and they know what works. With the boom-and-bust nature of resource markets and shareholder responsibilities, finances must be well managed.
The present: hybrid renewables power generation
At the Energy and Mines Summit, there was no discussion about whether it’s a good idea to consider renewables in the mix of power generation – it was simply a given. This is an industry in ‘early maturity’: it is no longer pioneers running a trial. Several systems are in the order of 100 MW capacity. Renewables are a tested and proven business decision. Everyone has crunched the numbers on their sites and, while each project has unique site-specific requirements, the conclusions are unanimous. The frontier is now getting access to skilled people, there is community engagement for siting of large assets and mutual benefits, and the industry is exploring emerging technologies such as electric fleet.
We now have all the technology needed to harness the power of the wind and the sun in an 80/20 mix with fossil fuels. Or a 50/50 mix when the system has solar power alone. And this is what is being implemented in practice all over Australia. We can do it in a way that achieves targets for price, reliability, service life, operability, maintainability and environmental impact. This greatly reduces the costs and risks of intermediate services such as refining and transportation as well as exposure to the global oil price. Mining companies are taking control of their energy supply by either owning the energy and storage assets or building well-defined low-risk partnerships.
The big project: transitioning the Pilbara to renewables
At the conference there was some focus on the Pilbara, which is a huge and complicated energy consumer, consuming 16 TWh (16 million MWh) of electricity per year, mostly coming from gas.
On the surface, it seems to be very low hanging fruit to quickly construct a few solar and wind assets to shift this picture. However, in the interests of the best long-term outcomes, the area needs planning, consultation and coordination. The Western Australian Government has developed a plan for ensuring that common-use infrastructure is used where possible, rather than risking having multiple redundant assets owned by different corporations. Aboriginal and community participation is recognised as crucial for the appropriate siting of wind, solar and transmission equipment.
The near future: electric fleet
Approximately half of a typical mine’s energy needs can be met by onsite electricity generation. The other half currently requires diesel fuel to run a fleet of light vehicles, monstrous ‘haul’ dump trucks such as the 250 tonne CAT 793, and every piece of mobile machinery in between. These mobile machines are the next target for reducing costs, carbon emissions and labour. Several trial projects are happening. For underground mines, where diesel has previously been used, huge ventilation fans will need far less power when there are no exhaust fumes to expel.
Machine manufacturers are developing a wide array of specialised battery electric products. In some applications, there is battery swap technology, as in modern power tools. In other applications, a fixed battery plugs in to recharge, like in an electric car. There are also trolley systems, akin to a tram or train. The best system for each job depends on the application.
Transitioning to a fully electric fleet will significantly increase a site’s electricity needs, with the biggest chargers running at 6 MW at full power. We are expecting to see sites’ electrical grids upgraded soon to integrate this high-power charging.
What is Entura doing?
At Entura, in addition to electrical generation and distribution design, we have specialised capabilities in control systems and power system studies for mining projects. Our microgrid control system (MCS) uses standard and reliable industrial Allen Bradley hardware to monitor and control the power station assets. We have a field-proven core algorithm for maintaining a priority of reliable power supply including backup/reserve supply, while making the greatest use of wind and solar where available. We’ve proven this process in our existing installations in the field and we lead the industry in methodology, practicality and voltage/frequency management.
We’ve seen the real benefits these systems bring to our clients and communities, both at mining sites and in other remote locations. Entura has a long history of design, formation and operation of microgrids throughout Australia (such as King Island, Flinders Island, Rottnest Island, and at mining sites such as the Agnew gold mine) and in the Pacific region (including the Cook Islands, the Federated States of Micronesia, Tonga, and the Solomon Islands, to name just a few).
Contact us if you’re interested in unlocking the full potential of microgrids for your operation or community, or if you’re interested in ways to increase your use of renewable energy.

[Image immediately above] Entura’s Patrick Pease, Greg Koppens and Mark Richardson at the 2025 Energy and Mines Summit
[Top of article] Greg Koppens (centre) onsite at Jabiru Power Station, Northern Territory
ABOUT THE AUTHOR
Greg Koppens is Entura’s Principal Control Engineer Hybrid Renewable Systems and previously led Entura’s secondary electrical engineering team. Greg’s experience spans power, oil and gas, and mining, including onsite roles. With over two decades of detailed design experience, Greg facilitates collaboration between engineering disciplines and other stakeholders to solve complex problems. He regularly shares his extensive expertise with the mining sector to advance their decarbonisation goals. Find out more about Greg in our podcast series here.
When the lights go out
Major power outage events, like the one that affected Spain and Portugal this April, can be enormously disruptive and even deadly. Here Entura’s Technical Director Power, Donald Vaughan, considers the complex factors at play and their implications for grids everywhere ...
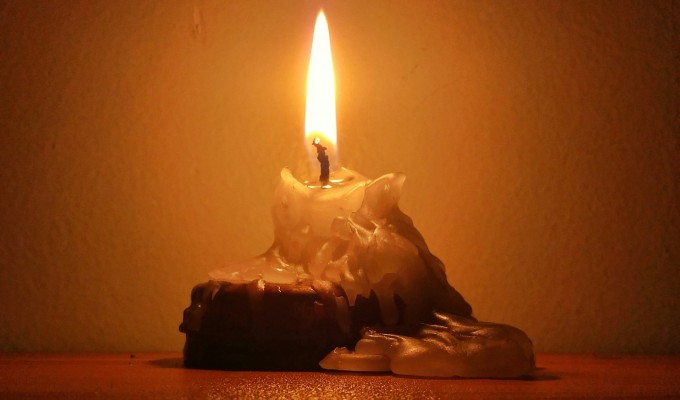
The recent power outage on the Iberian Peninsula provides a serious opportunity for reflection. Many articles have been published that try to explore the seconds and milliseconds after 12:32 PM on 28 April 2025 while only having access to the grainy frequency plots and approximate timelines that have been released (to date). This is not one of those articles. Nor is it an article that will lay blame on a particular technology or energy source. Instead, I will expand on the physics at play in this instance and reflect on whether current network security practices are adequately catering for changes to the power grid.
The physics
The power system is governed by the laws of physics, as is normal in the physical world. Quite a few of these laws tend to gang up on us during a power system event[1].
(i) conservation of energy
(ii) Ohm’s law
(iii) Newton’s laws of motion
and, of course,
(iv) Murphy’s law.
We’ll talk about the first three now and the last one later.
We learn very early that energy can neither be created nor destroyed (law i, above). This is at the heart of a power system event. The power system supplies loads by supporting voltage across the network that supplies millions of parallel loads. Each of these loads converts electrical energy into another form of energy based on the voltage it sees and its internal characteristics. This will continue as long as the voltage profile is maintained (law ii). So, demands take energy out of the power system regardless of what generation events occur.
We know that the main trouble in the recent Iberian event started when a large amount of generation stopped in southern Spain. This led to an imbalance between generation and demand in that region. That imbalance is immediately addressed through the inertial action of synchronous generation across Europe (law iii).
If interconnection were perfect, the burden of this inertial response would be shared perfectly across Europe and we probably wouldn’t be talking about this event quite as much as we are. Yet interconnection is rarely perfect (law ii). The frequency in Spain started to move away from frequency to the east and the AC interconnection to the east opened (which avoided the disturbance that stems from loss of synchronism). This should have been some help to the falling frequency in Spain given the eastward flows at the time. Under-frequency load shedding (UFLS) occurred around this time and should also have helped. It seems that the voltage disturbance that then occurred as a result of all these trips was the last straw.
Network security practices
It would be a gross over-simplification of network security practices to say that the power system should not lose customer load for the loss of one generation or network element (N-1 redundancy). The event on 28 April is way beyond that. Typically, for larger events, the grid should fail safely. We’ll look at that definition of ‘safely’ later. For now though, we can see that the grid did, in fact, try to fail gracefully:
- The AC interconnectors opened to avoid damaging loss of synchronism.
- The under-frequency load shedding operated to try to preserve supply to some customers and keep the grid up, so as to reduce the duration of the interruption.
- Other generating unit controls acted to either increase output or trip to avoid damage.
We see in the Iberian Peninsula outage, as we did in the major South Australian blackout in 2016, lots of independent protection operations slowly but surely weakening the grid to the extent that it is no longer viable. Each of these protection operations undergoes scrutiny after an event of this nature, and will likely lead to some changes in Spain and France as was the case in South Australia.
The 28 April event appears to be quite slow in comparison to some other network blackout events. Even so, the event lasted less than 20 seconds and had 2–3 stages within it. One of the bases of design of the AC network is that it can generally operate with minimal, fast coordination even under large events. Control relies on observation, computation and action. So, to manage an event, a control system must measure what it needs to reliably determine what control actions it must make, and then take those control actions (assuming it can control all the elements it might need to control) in time for them to have an effect. If we think about a need to deftly control the response of individual units (or control systems) in an unusual way in a short period of time, then we can quickly conclude that this may not be possible.
If we can’t manage these events in real time, we have three courses of action:
(i) Physical plant
We could design networks, network supports, and network and generator protection and control systems to be more robust in the face of large power system events, thus decreasing the likelihood of unnecessary cascading protection operation.
This would include better interconnection, more dynamic reactive support (separate from generating units and demand), system-level protection schemes, and a review of generating unit protection settings to ensure generator capability rather than network requirements setting operating limits
(ii) Dispatch rules
We could change dispatch to provide greater margin for real and reactive power control as determined by the security risk and the cost to mitigate it.
We could continue the traditional N-X approach to system supports or we could use a stochastic approach to determining system support requirements (weighting the probability of an event occurring against its impact). Either way, we’d have to pay an ‘insurance’ premium at each dispatch interval to make large-scale system outages less possible.
(iii) Restart planning and capability
We could make recovering from major blackout events easier and faster.
We think about these events in terms of how often they occur (which is what the first two course of action cover) and how long they last. System operators typically have generic plans for system restart that rely on starting synchronous plant and re-energising transmission systems and eventually customer demand. This can be made easier with interconnection. It can also be made easier with good visibility of voltages and voltage profiles across regions (and the tools to control them). Often, for big events like in South Australia in 2016, the network is left somewhat stricken from equipment damage. System restart efforts are often hampered in this scenario because plans need to be improvised to adapt. This depends on the skill, knowledge and experience of the operators. Some jurisdictions have simulated such events as part of training operators.
The fourth law
We know that ‘anything that can go wrong will go wrong’. Seemingly simple things can undermine the best laid plans and the best intentions. We often can’t plan for these things specifically, although HAZOPS, root-cause analyses, scenario simulations and reviews can help us understand where the problems may lie and give us a chance to close loop-holes before they become SNAFUs.
Major power outage events are serious. They often lead to loss of life or injury, and the recent Iberian Peninsula event was no exception. They also always have an economic impact, which is not always fairly distributed. As an industry we need to improve how we manage them. We also need to get better at talking about technical issues in a political environment. If there’s a risk of blackouts, we have a duty to not only mitigate that risk within the current rules but also advocate for rule changes if that mitigation is inadequate. To be most productive, this conversation should happen in a techno-economic environment. The automatic debate after power system events often focuses on the role of renewables, commercial interests and the like, which may sometimes be entertaining but inevitably affects the techno-economic outcomes in a negative way for everyone.
ABOUT THE AUTHOR
Donald Vaughan has over 20 years’ experience providing advice on regulatory and technical requirements for generators, substations and transmission systems. He has worked for all areas of the electrical industry, including generators, equipment suppliers, customers, NSPs and market operators. Donald specialises in the performance of power systems. His experience in generating units, governors and excitation systems provides a helpful perspective on how the physical electrical network behaves.
Image: Basil James on Unsplash
[1] There are more laws, but these are the main and most accessible.
Decommissioning battery energy storage systems: It’s never too early to plan for retirement
All good things come to an end – even big battery energy storage systems (BESS). In Australia, the end of life for BESS may feel very distant, since we’re really only in the infancy of the booming BESS industry; however, the life expectancy of these big batteries is nothing like the design life of other renewable energy and storage technologies. With BESS currently only lasting for around 10 to 15 years of operation, developers and owners of BESS installations need to be thinking and planning now for what decommissioning will involve and what it will cost. In fact, planning for decommissioning is best done right from the start – long before the project is constructed.
Here, one of Entura’s BESS specialists, Dr Rahmat Khezri, answers some burning questions about the end stages of a BESS project.
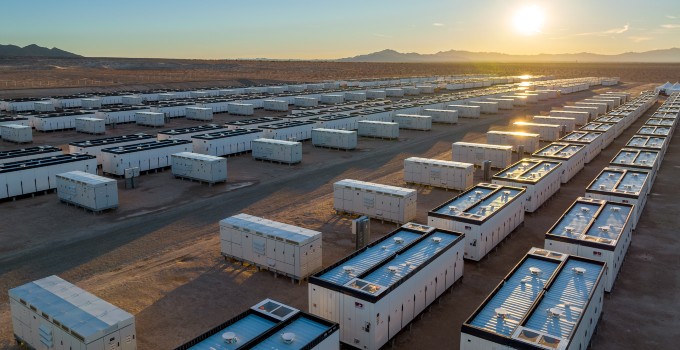
- When does the life of a BESS project come to an end?
The need to decommission a BESS project could arise either from the conclusion of a contract or power purchase agreement – though this is unlikely – or from the expiration of the battery’s operational lifespan. This could be when the battery capacity has degraded to a point where it is no longer financially viable to operate in the market or when the battery’s internal chemistry has reached a point where it is unsafe to continue operating.
For nickel-manganese-cobalt (NMC) batteries, which held a significant share of batteries before lithium-iron-phosphate (LFP) batteries entered the market, this could be after 3,000 to 7,000 cycles at 80% depth of discharge (DoD) or around 10 to 15 years. For LFP batteries, which are gradually dominating the battery market for BESS, it’s around 4,000 to 10,000 cycles or 15 to 20 years. However, several factors can either reduce or extend the battery lifespan. Higher DoD shortens battery life, and frequent high-power cycling (e.g. for frequency control ancillary services, FCAS) can accelerate degradation. Avoiding prolonged high or low state-of-charge management (SoC) reduces degradation. Temperature is also an issue – so proper cooling and heating systems can support greater longevity.
- Is decommissioning the only option?
Full decommissioning of aging BESS assets is not always necessary at battery end of life, as some key components – such as inverters, transformers and balance of plant (PoP) – often retain residual service life. There may be opportunities for repowering or augmentation instead, which will require a much lower level of decommissioning activities. Repowering replaces old batteries with newer or upgraded technology to restore or enhance performance. Augmentation generally aims to increase capacity or power output by expanding the system with additional capacity, for example by adding extra battery racks to an existing setup.
- What does a full BESS decommissioning program involve?
A typical full BESS decommissioning program includes the following activities:
- developing the decommissioning plan including a risk assessment
- de-energising the BESS
- removing power conversion systems (inverter/transformer stations)
- removing integrated battery storage units (site dismantling and packaging may be required)
- shipping the packed battery storage units to recycling facilities
- removing electrical cables and conduits
- removing substation equipment
- shipping the power conversion systems and cables to recyclers of electronic waste
- transporting non-recyclable material removed from the site to disposal facilities
- restoring the site.
- How long could BESS decommissioning take?
Once a BESS project stops operating, the decommissioning process can begin (usually within 12 months) and can take around 6 to 9 months. Of course, this will depend on the scale of the BESS project, which will determine the amount of battery units and electrical infrastructure that will need to be removed from the site. If site restoration is required, this could extend the timeframe.
- What might BESS decommissioning cost?
Decommissioning costs are made up of labour, equipment, transport, materials, and recycling or disposal. These costs can be categorised across the stages of the project: removing the BESS facilities, restoring the site, packaging and transport, and the cost of recycling or disposal. If it is possible to achieve some value from salvage, this can be offset against the decommissioning costs. Currently the total recycling fee for high-powered batteries is around $10–15 per kg. Assuming approximately 6 kg for 1 kWh, the recycling cost would be $60–90 per kWh.
- Talking about recycling, what are the options for decommissioning BESS sustainably?
In Australia, we’re still in the early days of developing a lithium battery recycling industry – but we are seeing increasing recognition by owners, developers, regulators and the community of the need for the renewable energy industry to strengthen the circular economy and minimise landfill. Battery modules are recyclable – but salvage and reuse are likely to remain very dynamic and the future market for used lithium-ion modules remains uncertain. We recommend that every BESS developer/owner should aim to maximise recycling and develop as sustainable a waste management plan as possible. It is worth noting that recycling and reuse of inverters, transformers and BoP components are well established and available.
- What regulatory requirements are there in Australia for BESS decommissioning, and how do you envisage this changing?
In Australia, BESS projects must comply with relevant environmental regulations, which vary by state but generally align with the environmental protection guidelines set by each state’s Environment Protection Authority (EPA). At the federal level, the Product Stewardship Act 2011 promotes the responsible management of products at the end of their life cycle, including batteries. Decommissioned components from BESS projects, particularly lithium-ion batteries, are typically classified as prescribed industrial waste (PIW), requiring handling by licensed transporters and disposal at approved facilities.
At this stage the permitting process to build a BESS facility does not require a formal plan for decommissioning and disposal – but it is probably only a matter of time until we see more stringent requirements as part of the development application process. Despite a detailed plan not yet being required, it is definitely worthwhile doing, not least because the costs of decommissioning should be factored into the business case from the outset.
- What lessons have been learned from international examples of BESS decommissioning?
There haven’t been many examples of BESS decommissioning in our region yet, but the example of decommissioning the Tehachapi Energy Storage Project (TSP) project in South California in 2022 is an instructive real-life case study. This 8 MW / 32 MWh lithium-ion battery project was one of world’s first and largest BESS when it was commissioned in 2014. It had a footprint of 585 m2, with 604 battery racks and two 40-foot PCS containers. The decommissioning was completed in just over 4 months from the generation of the purchase order to the finish.
A key takeaway from this case study is the significant impact that logistical and site-specific constraints can have on project outcomes. Although the PCS containers were initially expected to be removed within a single day, unforeseen space limitations and permitting restrictions ruled out the use of cranes. As a result, the containers had to be dismantled and cut into sections on-site. This increased the schedule by 17% and the cost by 20%. The lesson here is clear: success lies in the details, particularly when it comes to transport and access logistics. Thorough, site-specific planning is essential to avoid unexpected delays and budget overruns.
- What should Australian BESS developers and owners be doing now about decommissioning?
Ideally, every player in the BESS industry in Australia should be thinking ahead, however far off BESS decommissioning, repowering or augmentation may seem right now. It is never too early to start investigating the potential options, costs, timing, emissions, challenges and solutions – and developing a plan that can continue to evolve as the industry matures. A robust decommissioning plan will also be a valuable input into the technical due diligence process for sale/purchase. Ultimately, solid, early planning is the key to minimising risk and maximising value – and achieving a more efficient, more cost-effective and more sustainable outcome for any BESS project.
At Entura, we’ve been involved with BESS since the very start of the sector in Australia, and we’re always learning from our experiences here and around the world. We’re actively developing our analyses of decommissioning costs, transport, timing and circularity opportunities so that we can support your BESS project holistically, from cradle to grave.
Regardless of the stage of your BESS project, Entura can help. Contact Patrick Pease to find out how.
About the author
Senior Renewable Energy and BESS Engineer Dr Rahmat Khezri has vast professional and technical experience with batteries. He has worked in the renewable energy and battery industry in project delivery from BESS design, business case and feasibility analysis to operation and construction. Rahmat has managed several utility-scale BESS projects during his time with Entura, overseeing successful delivery while ensuring compliance with industry standards, optimising performance, and managing key stakeholder relationships. Before joining Entura, he worked on projects supported by Sustainability Victoria for technical design and business case development of ‘second-life BESS’ using retired batteries of electric vehicles. In 2023 and 2024, he was recognised by Stanford University as being in the top 2% of scientists worldwide for two consecutive years.