Renewables in remote mines – a litmus test for the wider renewables transition
Entura’s Greg Koppens has recently returned from the Energy and Mines Summit in Perth, where he led the ‘Think Tank’: a collaborative session addressing the challenge of powering process steam requirements from renewables-generated electricity. Here he shares his observations on the rise of renewables in the mining industry …
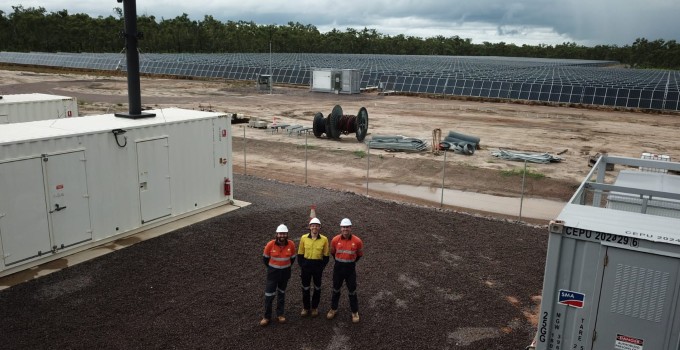
Australia’s mining industry is beginning the peak phase of its energy revolution. However, I find it unfortunate that this exciting fact is invisible to regular people. It is happening in remote areas on mining leases, inaccessible to the public. Each project alone is not sensational enough for media attention, but added together these projects are nothing short of a technology revolution. For remote mining sites to have a solar farm is now standard practice. In many cases this is backed up by battery storage and a handful of mines have onsite wind turbines.
The past: fossil-fuel driven mines
Australia is world-renowned for our mining industries, with mines of virtually every resource throughout our country. Up until about ten years ago, nearly all of Australia’s mines ran completely on diesel or gas. In most cases diesel was trucked in, or gas was brought in via pipeline. Most of these mines have energy expenses in the tens of millions of dollars per year. A small change in the oil price can drastically impact the mine’s bottom line.
If there’s one doubtless fact about mining, it’s that miners are practical people. They are problem solvers, and they know what works. With the boom-and-bust nature of resource markets and shareholder responsibilities, finances must be well managed.
The present: hybrid renewables power generation
At the Energy and Mines Summit, there was no discussion about whether it’s a good idea to consider renewables in the mix of power generation – it was simply a given. This is an industry in ‘early maturity’: it is no longer pioneers running a trial. Several systems are in the order of 100 MW capacity. Renewables are a tested and proven business decision. Everyone has crunched the numbers on their sites and, while each project has unique site-specific requirements, the conclusions are unanimous. The frontier is now getting access to skilled people, there is community engagement for siting of large assets and mutual benefits, and the industry is exploring emerging technologies such as electric fleet.
We now have all the technology needed to harness the power of the wind and the sun in an 80/20 mix with fossil fuels. Or a 50/50 mix when the system has solar power alone. And this is what is being implemented in practice all over Australia. We can do it in a way that achieves targets for price, reliability, service life, operability, maintainability and environmental impact. This greatly reduces the costs and risks of intermediate services such as refining and transportation as well as exposure to the global oil price. Mining companies are taking control of their energy supply by either owning the energy and storage assets or building well-defined low-risk partnerships.
The big project: transitioning the Pilbara to renewables
At the conference there was some focus on the Pilbara, which is a huge and complicated energy consumer, consuming 16 TWh (16 million MWh) of electricity per year, mostly coming from gas.
On the surface, it seems to be very low hanging fruit to quickly construct a few solar and wind assets to shift this picture. However, in the interests of the best long-term outcomes, the area needs planning, consultation and coordination. The Western Australian Government has developed a plan for ensuring that common-use infrastructure is used where possible, rather than risking having multiple redundant assets owned by different corporations. Aboriginal and community participation is recognised as crucial for the appropriate siting of wind, solar and transmission equipment.
The near future: electric fleet
Approximately half of a typical mine’s energy needs can be met by onsite electricity generation. The other half currently requires diesel fuel to run a fleet of light vehicles, monstrous ‘haul’ dump trucks such as the 250 tonne CAT 793, and every piece of mobile machinery in between. These mobile machines are the next target for reducing costs, carbon emissions and labour. Several trial projects are happening. For underground mines, where diesel has previously been used, huge ventilation fans will need far less power when there are no exhaust fumes to expel.
Machine manufacturers are developing a wide array of specialised battery electric products. In some applications, there is battery swap technology, as in modern power tools. In other applications, a fixed battery plugs in to recharge, like in an electric car. There are also trolley systems, akin to a tram or train. The best system for each job depends on the application.
Transitioning to a fully electric fleet will significantly increase a site’s electricity needs, with the biggest chargers running at 6 MW at full power. We are expecting to see sites’ electrical grids upgraded soon to integrate this high-power charging.
What is Entura doing?
At Entura, in addition to electrical generation and distribution design, we have specialised capabilities in control systems and power system studies for mining projects. Our microgrid control system (MCS) uses standard and reliable industrial Allen Bradley hardware to monitor and control the power station assets. We have a field-proven core algorithm for maintaining a priority of reliable power supply including backup/reserve supply, while making the greatest use of wind and solar where available. We’ve proven this process in our existing installations in the field and we lead the industry in methodology, practicality and voltage/frequency management.
We’ve seen the real benefits these systems bring to our clients and communities, both at mining sites and in other remote locations. Entura has a long history of design, formation and operation of microgrids throughout Australia (such as King Island, Flinders Island, Rottnest Island, and at mining sites such as the Agnew gold mine) and in the Pacific region (including the Cook Islands, the Federated States of Micronesia, Tonga, and the Solomon Islands, to name just a few).
Contact us if you’re interested in unlocking the full potential of microgrids for your operation or community, or if you’re interested in ways to increase your use of renewable energy.

[Image immediately above] Entura’s Patrick Pease, Greg Koppens and Mark Richardson at the 2025 Energy and Mines Summit
[Top of article] Greg Koppens (centre) onsite at Jabiru Power Station, Northern Territory
ABOUT THE AUTHOR
Greg Koppens is Entura’s Principal Control Engineer Hybrid Renewable Systems and previously led Entura’s secondary electrical engineering team. Greg’s experience spans power, oil and gas, and mining, including onsite roles. With over two decades of detailed design experience, Greg facilitates collaboration between engineering disciplines and other stakeholders to solve complex problems. He regularly shares his extensive expertise with the mining sector to advance their decarbonisation goals. Find out more about Greg in our podcast series here.
New technologies are important tools, but they need to be used properly
Entura’s Technical Director (Water), Richard Herweynen, recently attended the 2025 ICOLD Congress in Chengdu, China, themed ‘Common Challenges, Shared Future, Better Dams’. Here he shares his observations on the state of play in the international dams industry – and the opportunities emerging with artificial intelligence and automation.
My first ICOLD Congress was in Beijing, China in 2000. I was presenting some finite element analysis work that I had done on Gordon Dam, a 140m-high concrete arch dam in Tasmania. The analysis was being used to help predict and explain some cracks that had formed at the base of the downstream face of the concrete shell, roughly normal to the foundation, during first filling. In the 1980s, an attempt had been made to model the crack using finite element modelling, but with little success due to the coarseness of the mesh. However, by the late 1990s, computing power had increased and finite element programs had improved, providing the capability to construct more detailed finite element models, which were able to predict and explain the cracking that had occurred.
Dr Sergio Giudici, the designer of Gordon Dam, was my mentor on this finite element analysis, and he reinforced these principles:
- It is important to verify the input data to make sure the model represents, as well as possible, the actual dam parameters.
- Results should be validated using alternative techniques to give the engineer confidence in the results that the model is producing (i.e. structural hand calculations still have a place).
- Complexity should be built into these models only gradually, so that the engineer can see the impact of changes and determine whether they are reasonable.
These same principles are true for many complex engineering models and when setting up calculation spreadsheets or similar.
Now, 25 years on, I have had the privilege of attending the 2025 ICOLD Congress in Chengdu, China. At this Congress, there was much talk about the importance of dams in society for water security, the growing role dams and reservoirs play in providing resilience to climate change and the energy transition, the importance of balancing economic benefits and environmental needs, and – in all of this – the importance of ensuring that our dams are safe for communities downstream.
We have discussed many of these themes before – and they remain highly important; however, one thing I took away from ICOLD 2025 in particular was how China is embracing technology and advancing a ‘Smart Dam’ initiative.
New technologies and smarter dams
One could say that our industry has always been building smart dams, but China’s ‘Smart Dam’ concept is about using the full power of current technologies to construct, monitor and operate dams in smarter ways, and to use technologies to predict and adapt to changing conditions.
The CHINCOLD Workshop on Digital and Intelligent Technologies for Dam Construction, Operation and Maintenance, which occurred during ICOLD 2025, gave a glimpse of what may be possible.
Many projects utilise 3-dimensional digital models and building information modelling (BIM). However, the concept of having a digital twin of the dam, replicating every aspect of the physical dam in a digital form, opens the door to many possibilities, especially in light of the advent of artificial intelligence (AI).
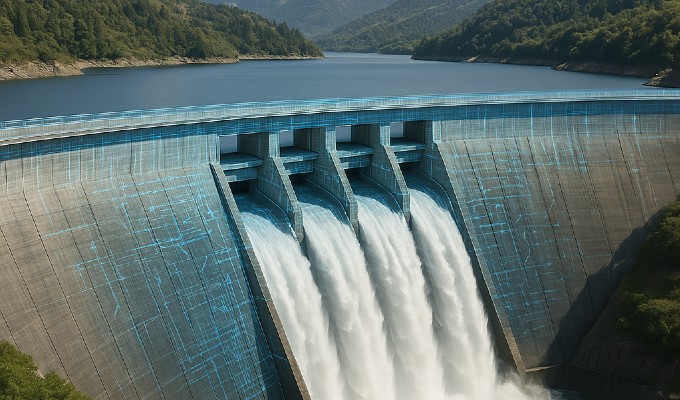
Artificial intelligence and machine learning
Many organisations and nations have been cautious about AI, but China is increasingly adopting it to improve construction practices in dam engineering, improve monitoring and surveillance of dams, and to help adapt to extreme events as they occur.
Machine learning (ML), an element of AI, enables computers to learn from data without being explicitly programmed. ML algorithms analyse data, identify patterns, and make predictions or decisions, improving their performance over time and with more data. There are no doubt many engineering applications where ML could be used to help improve predictive modelling or optimisation, and to make these more efficient. However, the same principles that were important when we were beginning to embrace larger, more refined finite element models with the advent of faster computing remain true here:
- We must verify the input data that machine learning is utilising to ensure we don’t get ‘garbage in equals garbage out’.
- Results need to be validated. AI needs to be trained correctly, and we need experts involved at this stage to ensure that the outputs from AI are correct.
- Complexity, or the full power of technology, should be added incrementally, to provide progressive confidence in the outcomes.
Engineering is the application of science, and therefore it is critical for every engineer to understand the fundamental principles and how to apply them. The complex computer programs used for a lot of engineering modelling can become ‘black boxes’, and practitioners risk diluting or losing their understanding of the fundamental principles behind the models, and hence their ability to validate the results.
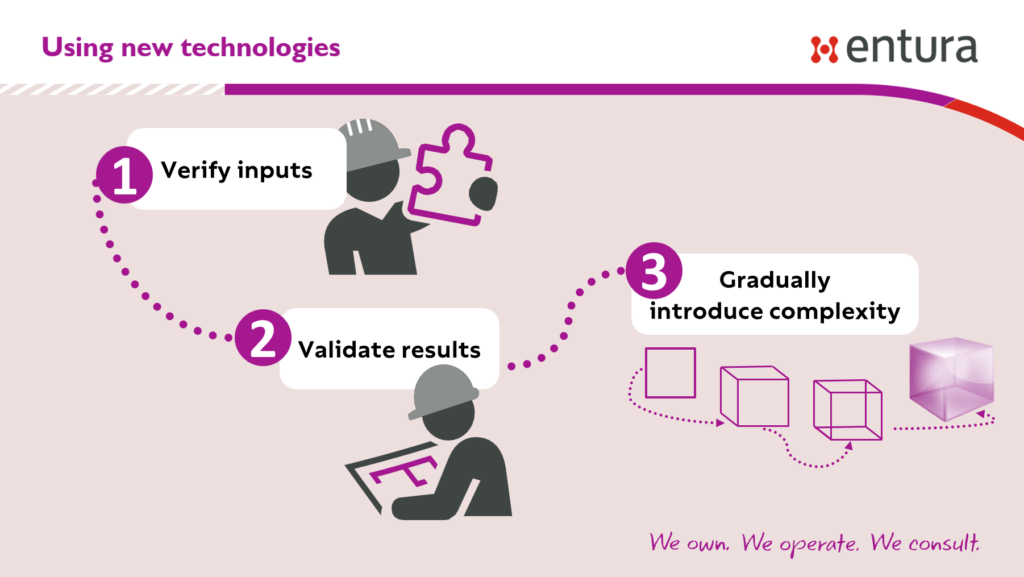
Automation brings a step change in efficiency and accuracy
At the ICOLD Congress in 2000, I co-authored a paper for the international symposium on concrete-faced rockfill dams (CFRD) entitled ‘Hydro Tasmania experience in concrete-faced rockfill dams – past, present and future’. There is no doubt that Hydro Tasmania has a strong history in CFRD, with Cethana Dam playing an important role in the development of the modern, high CFRD.
In 2000, however, the future in CFRD that we envisaged did not include unmanned construction equipment with automatic quality control feedback loops. At the 2025 CHINCOLD Workshop on Digital and Intelligent Technologies for Dam Construction, Operation and Maintenance, a presentation was given by Wang Jiajun from Tianjin University on intelligent unmanned roller systems to compact rockfill dams. Unmanned rolling compaction (URC) systems involve three core technology modules: (1) intelligent perception, (2) autonomous planning and decision making, and (3) intelligent control. These systems use automated driving technology to control the rolling process on earth and rockfill dams, improving productivity and quality. They can accurately control compaction parameters such as passes, speed, vibration and lift thickness. URC systems also enable continuous monitoring and real-time feedback for quality control, reducing human error and improving overall project performance. This automated technology was used on the 295m-high, 1.57km-long Lianghekou hydropower dam in China, with a total fill volume of 43 million m3.
The changing face of dam engineering
With AI and automation, the scope for embracing new technology in dam engineering is growing fast. It is clear that there are significant benefits that could be realised for dam design, construction, operation, dam safety and emergency response – and there’s a role for these advanced technologies at all of the stages of the life cycle of a dam. A degree of caution is appropriate and necessary, but caution should not be a reason to refuse to engage with the new technologies available to our industry.
However, with more sophisticated models – such as digital twins – being created of our dams, it is important to ensure we maintain the guiding engineering principles of verifying input data, validating models for correctness, and building complexity gradually. By doing this, we can provide the necessary assurance and confidence in our increasingly sophisticated and evolving tools.
ABOUT THE AUTHOR
Richard Herweynen is Entura’s Technical Director – Water. He has more than three decades of experience in dam and hydropower engineering, working throughout the Indo-Pacific region on both dam and hydropower projects. His experience covers all aspects including investigations, feasibility studies, detailed design, construction liaison, operation and maintenance and risk assessment for both new and existing projects. Richard has been part of a number of recent expert review panels for major water projects. He participated in the ANCOLD working group for concrete gravity dams and was the Chairman of the ICOLD technical committee on engineering activities in the planning process for water resources projects. Richard has won many engineering excellence and innovation awards (including Engineers Australia’s Professional Engineer of the Year 2012 – Tasmanian Division), and has published more than 30 technical papers on dam engineering.
When the lights go out
Major power outage events, like the one that affected Spain and Portugal this April, can be enormously disruptive and even deadly. Here Entura’s Technical Director Power, Donald Vaughan, considers the complex factors at play and their implications for grids everywhere ...
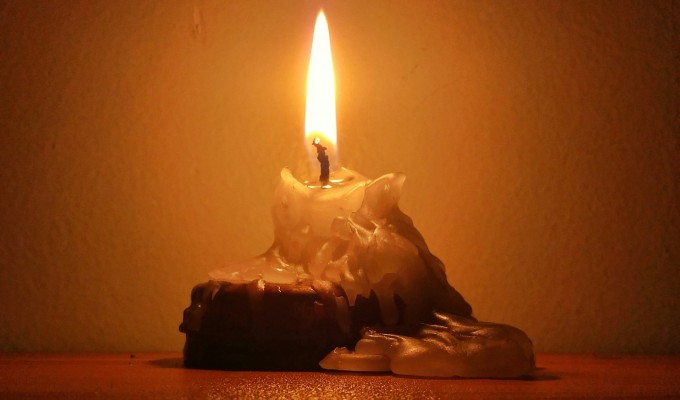
The recent power outage on the Iberian Peninsula provides a serious opportunity for reflection. Many articles have been published that try to explore the seconds and milliseconds after 12:32 PM on 28 April 2025 while only having access to the grainy frequency plots and approximate timelines that have been released (to date). This is not one of those articles. Nor is it an article that will lay blame on a particular technology or energy source. Instead, I will expand on the physics at play in this instance and reflect on whether current network security practices are adequately catering for changes to the power grid.
The physics
The power system is governed by the laws of physics, as is normal in the physical world. Quite a few of these laws tend to gang up on us during a power system event[1].
(i) conservation of energy
(ii) Ohm’s law
(iii) Newton’s laws of motion
and, of course,
(iv) Murphy’s law.
We’ll talk about the first three now and the last one later.
We learn very early that energy can neither be created nor destroyed (law i, above). This is at the heart of a power system event. The power system supplies loads by supporting voltage across the network that supplies millions of parallel loads. Each of these loads converts electrical energy into another form of energy based on the voltage it sees and its internal characteristics. This will continue as long as the voltage profile is maintained (law ii). So, demands take energy out of the power system regardless of what generation events occur.
We know that the main trouble in the recent Iberian event started when a large amount of generation stopped in southern Spain. This led to an imbalance between generation and demand in that region. That imbalance is immediately addressed through the inertial action of synchronous generation across Europe (law iii).
If interconnection were perfect, the burden of this inertial response would be shared perfectly across Europe and we probably wouldn’t be talking about this event quite as much as we are. Yet interconnection is rarely perfect (law ii). The frequency in Spain started to move away from frequency to the east and the AC interconnection to the east opened (which avoided the disturbance that stems from loss of synchronism). This should have been some help to the falling frequency in Spain given the eastward flows at the time. Under-frequency load shedding (UFLS) occurred around this time and should also have helped. It seems that the voltage disturbance that then occurred as a result of all these trips was the last straw.
Network security practices
It would be a gross over-simplification of network security practices to say that the power system should not lose customer load for the loss of one generation or network element (N-1 redundancy). The event on 28 April is way beyond that. Typically, for larger events, the grid should fail safely. We’ll look at that definition of ‘safely’ later. For now though, we can see that the grid did, in fact, try to fail gracefully:
- The AC interconnectors opened to avoid damaging loss of synchronism.
- The under-frequency load shedding operated to try to preserve supply to some customers and keep the grid up, so as to reduce the duration of the interruption.
- Other generating unit controls acted to either increase output or trip to avoid damage.
We see in the Iberian Peninsula outage, as we did in the major South Australian blackout in 2016, lots of independent protection operations slowly but surely weakening the grid to the extent that it is no longer viable. Each of these protection operations undergoes scrutiny after an event of this nature, and will likely lead to some changes in Spain and France as was the case in South Australia.
The 28 April event appears to be quite slow in comparison to some other network blackout events. Even so, the event lasted less than 20 seconds and had 2–3 stages within it. One of the bases of design of the AC network is that it can generally operate with minimal, fast coordination even under large events. Control relies on observation, computation and action. So, to manage an event, a control system must measure what it needs to reliably determine what control actions it must make, and then take those control actions (assuming it can control all the elements it might need to control) in time for them to have an effect. If we think about a need to deftly control the response of individual units (or control systems) in an unusual way in a short period of time, then we can quickly conclude that this may not be possible.
If we can’t manage these events in real time, we have three courses of action:
(i) Physical plant
We could design networks, network supports, and network and generator protection and control systems to be more robust in the face of large power system events, thus decreasing the likelihood of unnecessary cascading protection operation.
This would include better interconnection, more dynamic reactive support (separate from generating units and demand), system-level protection schemes, and a review of generating unit protection settings to ensure generator capability rather than network requirements setting operating limits
(ii) Dispatch rules
We could change dispatch to provide greater margin for real and reactive power control as determined by the security risk and the cost to mitigate it.
We could continue the traditional N-X approach to system supports or we could use a stochastic approach to determining system support requirements (weighting the probability of an event occurring against its impact). Either way, we’d have to pay an ‘insurance’ premium at each dispatch interval to make large-scale system outages less possible.
(iii) Restart planning and capability
We could make recovering from major blackout events easier and faster.
We think about these events in terms of how often they occur (which is what the first two course of action cover) and how long they last. System operators typically have generic plans for system restart that rely on starting synchronous plant and re-energising transmission systems and eventually customer demand. This can be made easier with interconnection. It can also be made easier with good visibility of voltages and voltage profiles across regions (and the tools to control them). Often, for big events like in South Australia in 2016, the network is left somewhat stricken from equipment damage. System restart efforts are often hampered in this scenario because plans need to be improvised to adapt. This depends on the skill, knowledge and experience of the operators. Some jurisdictions have simulated such events as part of training operators.
The fourth law
We know that ‘anything that can go wrong will go wrong’. Seemingly simple things can undermine the best laid plans and the best intentions. We often can’t plan for these things specifically, although HAZOPS, root-cause analyses, scenario simulations and reviews can help us understand where the problems may lie and give us a chance to close loop-holes before they become SNAFUs.
Major power outage events are serious. They often lead to loss of life or injury, and the recent Iberian Peninsula event was no exception. They also always have an economic impact, which is not always fairly distributed. As an industry we need to improve how we manage them. We also need to get better at talking about technical issues in a political environment. If there’s a risk of blackouts, we have a duty to not only mitigate that risk within the current rules but also advocate for rule changes if that mitigation is inadequate. To be most productive, this conversation should happen in a techno-economic environment. The automatic debate after power system events often focuses on the role of renewables, commercial interests and the like, which may sometimes be entertaining but inevitably affects the techno-economic outcomes in a negative way for everyone.
ABOUT THE AUTHOR
Donald Vaughan has over 20 years’ experience providing advice on regulatory and technical requirements for generators, substations and transmission systems. He has worked for all areas of the electrical industry, including generators, equipment suppliers, customers, NSPs and market operators. Donald specialises in the performance of power systems. His experience in generating units, governors and excitation systems provides a helpful perspective on how the physical electrical network behaves.
Image: Basil James on Unsplash
[1] There are more laws, but these are the main and most accessible.
Decommissioning battery energy storage systems: It’s never too early to plan for retirement
All good things come to an end – even big battery energy storage systems (BESS). In Australia, the end of life for BESS may feel very distant, since we’re really only in the infancy of the booming BESS industry; however, the life expectancy of these big batteries is nothing like the design life of other renewable energy and storage technologies. With BESS currently only lasting for around 10 to 15 years of operation, developers and owners of BESS installations need to be thinking and planning now for what decommissioning will involve and what it will cost. In fact, planning for decommissioning is best done right from the start – long before the project is constructed.
Here, one of Entura’s BESS specialists, Dr Rahmat Khezri, answers some burning questions about the end stages of a BESS project.
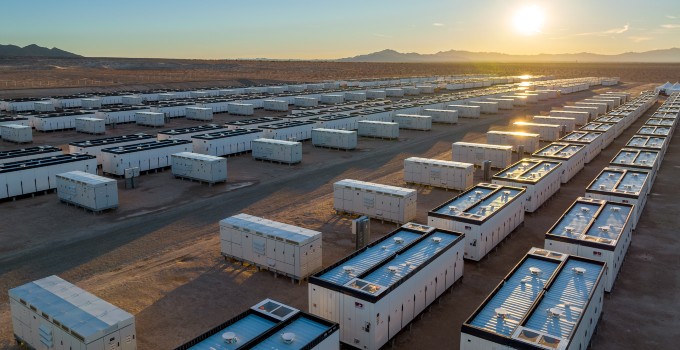
- When does the life of a BESS project come to an end?
The need to decommission a BESS project could arise either from the conclusion of a contract or power purchase agreement – though this is unlikely – or from the expiration of the battery’s operational lifespan. This could be when the battery capacity has degraded to a point where it is no longer financially viable to operate in the market or when the battery’s internal chemistry has reached a point where it is unsafe to continue operating.
For nickel-manganese-cobalt (NMC) batteries, which held a significant share of batteries before lithium-iron-phosphate (LFP) batteries entered the market, this could be after 3,000 to 7,000 cycles at 80% depth of discharge (DoD) or around 10 to 15 years. For LFP batteries, which are gradually dominating the battery market for BESS, it’s around 4,000 to 10,000 cycles or 15 to 20 years. However, several factors can either reduce or extend the battery lifespan. Higher DoD shortens battery life, and frequent high-power cycling (e.g. for frequency control ancillary services, FCAS) can accelerate degradation. Avoiding prolonged high or low state-of-charge management (SoC) reduces degradation. Temperature is also an issue – so proper cooling and heating systems can support greater longevity.
- Is decommissioning the only option?
Full decommissioning of aging BESS assets is not always necessary at battery end of life, as some key components – such as inverters, transformers and balance of plant (PoP) – often retain residual service life. There may be opportunities for repowering or augmentation instead, which will require a much lower level of decommissioning activities. Repowering replaces old batteries with newer or upgraded technology to restore or enhance performance. Augmentation generally aims to increase capacity or power output by expanding the system with additional capacity, for example by adding extra battery racks to an existing setup.
- What does a full BESS decommissioning program involve?
A typical full BESS decommissioning program includes the following activities:
- developing the decommissioning plan including a risk assessment
- de-energising the BESS
- removing power conversion systems (inverter/transformer stations)
- removing integrated battery storage units (site dismantling and packaging may be required)
- shipping the packed battery storage units to recycling facilities
- removing electrical cables and conduits
- removing substation equipment
- shipping the power conversion systems and cables to recyclers of electronic waste
- transporting non-recyclable material removed from the site to disposal facilities
- restoring the site.
- How long could BESS decommissioning take?
Once a BESS project stops operating, the decommissioning process can begin (usually within 12 months) and can take around 6 to 9 months. Of course, this will depend on the scale of the BESS project, which will determine the amount of battery units and electrical infrastructure that will need to be removed from the site. If site restoration is required, this could extend the timeframe.
- What might BESS decommissioning cost?
Decommissioning costs are made up of labour, equipment, transport, materials, and recycling or disposal. These costs can be categorised across the stages of the project: removing the BESS facilities, restoring the site, packaging and transport, and the cost of recycling or disposal. If it is possible to achieve some value from salvage, this can be offset against the decommissioning costs. Currently the total recycling fee for high-powered batteries is around $10–15 per kg. Assuming approximately 6 kg for 1 kWh, the recycling cost would be $60–90 per kWh.
- Talking about recycling, what are the options for decommissioning BESS sustainably?
In Australia, we’re still in the early days of developing a lithium battery recycling industry – but we are seeing increasing recognition by owners, developers, regulators and the community of the need for the renewable energy industry to strengthen the circular economy and minimise landfill. Battery modules are recyclable – but salvage and reuse are likely to remain very dynamic and the future market for used lithium-ion modules remains uncertain. We recommend that every BESS developer/owner should aim to maximise recycling and develop as sustainable a waste management plan as possible. It is worth noting that recycling and reuse of inverters, transformers and BoP components are well established and available.
- What regulatory requirements are there in Australia for BESS decommissioning, and how do you envisage this changing?
In Australia, BESS projects must comply with relevant environmental regulations, which vary by state but generally align with the environmental protection guidelines set by each state’s Environment Protection Authority (EPA). At the federal level, the Product Stewardship Act 2011 promotes the responsible management of products at the end of their life cycle, including batteries. Decommissioned components from BESS projects, particularly lithium-ion batteries, are typically classified as prescribed industrial waste (PIW), requiring handling by licensed transporters and disposal at approved facilities.
At this stage the permitting process to build a BESS facility does not require a formal plan for decommissioning and disposal – but it is probably only a matter of time until we see more stringent requirements as part of the development application process. Despite a detailed plan not yet being required, it is definitely worthwhile doing, not least because the costs of decommissioning should be factored into the business case from the outset.
- What lessons have been learned from international examples of BESS decommissioning?
There haven’t been many examples of BESS decommissioning in our region yet, but the example of decommissioning the Tehachapi Energy Storage Project (TSP) project in South California in 2022 is an instructive real-life case study. This 8 MW / 32 MWh lithium-ion battery project was one of world’s first and largest BESS when it was commissioned in 2014. It had a footprint of 585 m2, with 604 battery racks and two 40-foot PCS containers. The decommissioning was completed in just over 4 months from the generation of the purchase order to the finish.
A key takeaway from this case study is the significant impact that logistical and site-specific constraints can have on project outcomes. Although the PCS containers were initially expected to be removed within a single day, unforeseen space limitations and permitting restrictions ruled out the use of cranes. As a result, the containers had to be dismantled and cut into sections on-site. This increased the schedule by 17% and the cost by 20%. The lesson here is clear: success lies in the details, particularly when it comes to transport and access logistics. Thorough, site-specific planning is essential to avoid unexpected delays and budget overruns.
- What should Australian BESS developers and owners be doing now about decommissioning?
Ideally, every player in the BESS industry in Australia should be thinking ahead, however far off BESS decommissioning, repowering or augmentation may seem right now. It is never too early to start investigating the potential options, costs, timing, emissions, challenges and solutions – and developing a plan that can continue to evolve as the industry matures. A robust decommissioning plan will also be a valuable input into the technical due diligence process for sale/purchase. Ultimately, solid, early planning is the key to minimising risk and maximising value – and achieving a more efficient, more cost-effective and more sustainable outcome for any BESS project.
At Entura, we’ve been involved with BESS since the very start of the sector in Australia, and we’re always learning from our experiences here and around the world. We’re actively developing our analyses of decommissioning costs, transport, timing and circularity opportunities so that we can support your BESS project holistically, from cradle to grave.
Regardless of the stage of your BESS project, Entura can help. Contact Patrick Pease to find out how.
About the author
Senior Renewable Energy and BESS Engineer Dr Rahmat Khezri has vast professional and technical experience with batteries. He has worked in the renewable energy and battery industry in project delivery from BESS design, business case and feasibility analysis to operation and construction. Rahmat has managed several utility-scale BESS projects during his time with Entura, overseeing successful delivery while ensuring compliance with industry standards, optimising performance, and managing key stakeholder relationships. Before joining Entura, he worked on projects supported by Sustainability Victoria for technical design and business case development of ‘second-life BESS’ using retired batteries of electric vehicles. In 2023 and 2024, he was recognised by Stanford University as being in the top 2% of scientists worldwide for two consecutive years.
Planning for the future – the challenges of dam inspection and maintenance
No dam is ‘maintenance free’. Without appropriate maintenance and refurbishment at the right times, a dam may not be able to fulfil its function safely for the full length of its design life (which could be more than a century).
This presents many challenges for asset owners. To keep the dam operating as the designer intended – and get the most out of the original investment over the long term – owners will need to develop and implement a suitable operations and maintenance manual aligned with the asset management plan and reflecting a ‘whole of life’ strategy. These plans will need to consider the unique characteristics of each dam and cover all the relevant issues. And there are many!
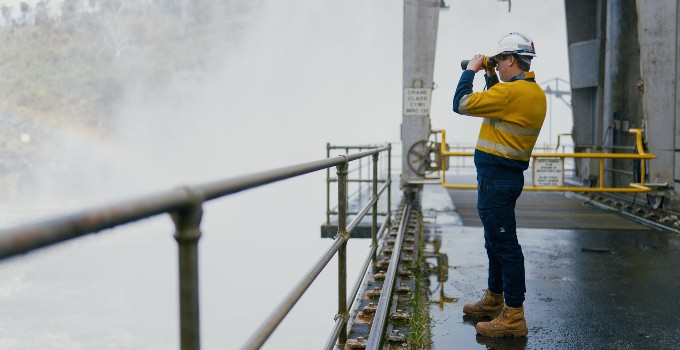
Dams consist of a number of different elements. There are the main civil engineering components including the wall that holds back the water and the spillway – but there could also be mechanical elements (pipework, valves and gates) and electrical elements (power supply to lights, valves, gate motors and control systems). Each of these elements will have its own operational and maintenance requirements and different lifecycle duration. Ideally, all this detail needs to be captured in the operation and maintenance manual (as recommended by ANCOLD guidelines) and in an asset management plan.
Civil components
The civil components of dams have the longest life span, typically more than 100 years if well constructed and maintained. Common maintenance items that need to be regularly addressed include:
- Vegetation management
Trees and bushes will readily grow in earthfill and rockfill embankments. Regular control (e.g. annually) is necessary to ensure that roots don’t grow through the fill and initiate leaks through the embankment. Mowing the grass on the downstream face of the earthfill embankment and downstream contact is necessary so that the condition of the face can be observed. Even concrete gravity and concrete arch dams will require vegetation control along the downstream face contact with the foundation so that the dam can be easily viewed in routine inspections.
- Surface water drainage
Dam construction typically affects natural drainage lines, which is why surface water drains are a common feature around and on dams – such as along the groins (where the dam wall intersects with natural ground), along berms in embankment dams, along benches, at the top of cuttings, and along access tracks. Drains will need regular inspection for both erosion and blockage due to sediment or vegetation.
- Foundation drain cleaning
Concrete gravity dams and concrete arch dams typically have drains drilled into the rock foundations to relieve uplift pressures and help maintain stability of the wall. Over time, silt or iron-rich slime can build up as a byproduct of bacterial growth in the drains, reducing effectiveness. These drains typically require 5-yearly high-pressure flushing. Cleaning will also be needed for drains underneath spillways founded on rock and cut slopes in rock.
- Protection of the dam safety monitoring system
Protecting the dam safety monitoring system requires a range of regular activities. These include cleaning and clearing vee-notch seepage monitoring weirs, checking survey monitoring pillars and targets, and checking the calibration of level monitoring and indication devices, such as reservoir-level sensors, piezometers, tiltmeters and inclinometers. Regular functional testing will also need to be carried out on the alarming and tripping devices that form the primary protection elements of the dam, including spillway gates and scour valves.
- Clearing of trash racks
Outlet works usually have trash racks to stop debris entering the pipework and causing blockages. It’s important to check that the build-up of debris is tolerable and that any hydraulic losses won’t affect operations. Assessing and removing the debris isn’t easy, as the trash racks are often accessible only by remotely operated vehicles (ROVs) or by divers. Before the inspection, the outlet will typically need to be closed and isolated.
Inspection-driven longer term maintenance will also be required for particular elements of the dam, ideally addressing repair items promptly to minimise damage and the cost of future repairs if left untreated. For example, concrete repairs may be needed to address erosion in stilling basins and spillway chutes, or spalling of concrete due to reinforcement corrosion or freeze/thaw damage.
While regular inspections should be undertaken to detect slow deterioration, special inspections following major events – such as floods or earthquakes – should also be part of the operations and maintenance plan. Given that the key areas for inspection are often difficult to access safely, use of UAVs (e.g. to inspect a spillway crest and chute) or ROVs (e.g. to undertake underwater inspections or scanning of stilling basins, plunge pools or riverbed scour) should be considered.
When special inspections identify the need for repairs, the time is right to consider whether the dam’s design or surveillance could be improved to increase resilience for a similar event in future. For example, a higher strength concrete overlay may treat erosion of a spillway chute and increase its resistance to future erosion.
Mechanical components
Mechanical items such as steel or cast-iron pipework can also often last up to 100 years if adequately protected from corrosion. Concrete and cement mortar are very effective for this purpose as the alkaline environment provided by the cement paste provides a very low corrosion environment. Key to the effectiveness of this protection is ensuring that the cement remains in intimate contact with the steel or iron. This will require regular inspections and timely repairs. Where concrete protection is not practical, paint systems can be very effective for up to about 20 years. A suitable inspection regime will be needed so that any areas where the paint has deteriorated can be detected and patched.
Mechanical items such as valves and gates typically have an effective life of around 50 years; however, they need to be exercised regularly to keep them able to work on demand. This is not an issue of the parts wearing out from use; rather, it’s the risk of them seizing due to lack of use. Regular lubrication of bearings, gearboxes and trunnions needs to be included as part of the maintenance of these items. This is particularly important in scour valves and spillway gates that may have a very low frequency of use during normal operations but are there for use in emergencies. The wire ropes commonly used to hoist spillway gates open will need even more frequent replacement, at approximately every 20 years.
Electrical components
Electric motors are commonly used to drive the winches hoisting spillway gates or driving the shafts to open valves. Associated with the motors will be switchboards and power supply systems, typically including grid power supply and backup diesel generators. The typical life of these components is around 25 years. As with the mechanical components, lack of operation can lead to premature failure, so a regular regime of exercise is necessary to ensure maximum reliability and life.
The programable logic controllers (PLC) that are used to automate operations, allow remote operations and generate alarms will have a typical life of only 10–12 years due to changes in programming languages and rapid evolution of the hardware.
Getting the most out of life
As we’ve seen, regular maintenance is fundamental for keeping all the components of a dam operating as intended and maximising their lifespan – whether that’s 10 years or 100. This maintenance, including the exercising of the mechanical and electrical components, needs to be clearly documented in the operations and maintenance manual and recorded in an asset management system. The asset management plan must allow for regular maintenance and also budget appropriately for replacement or refurbishment when any component of the dam is due for retirement.
At Entura, we believe in getting the most out of every piece of infrastructure because that’s good for our clients, communities and the planet. With a solid regime of inspection and maintenance, all the parts of your dam will be on the strongest path to a long, reliable and sustainable life.
If you’d like to talk with us about inspecting and maintaining your dam/s, contact Phil Ellerton, Paul Southcott, or Richard Herweynen.
About the author
Paul Southcott is Entura’s Senior Principal – Dams and Headworks. Paul has an outstanding depth of knowledge and skill developed over more than 3 decades in the fields of civil and dam engineering. He is a highly respected dams specialist and was recognised as Tasmania’s Professional Engineer of the Year in Engineers Australia’s 2021 Engineering Excellence Awards. Paul has contributed to many major dam and hydropower projects in Australia and abroad, including Tasmania’s ‘Battery of the Nation’, the Tarraleah hydropower scheme, Snowy Hydro, and numerous programs of work for water utilities including SeqWater, Sun Water and SAWater. His expertise is a crucial part of Entura’s ongoing support for upgrade and safety works for Hydro Tasmania’s and TasWater’s extensive dams portfolios. Paul is passionate about furthering the engineering profession through knowledge sharing, and has supported many young and emerging engineers through training and mentoring.
What have we learnt about renewable microgrids and remote area power systems?
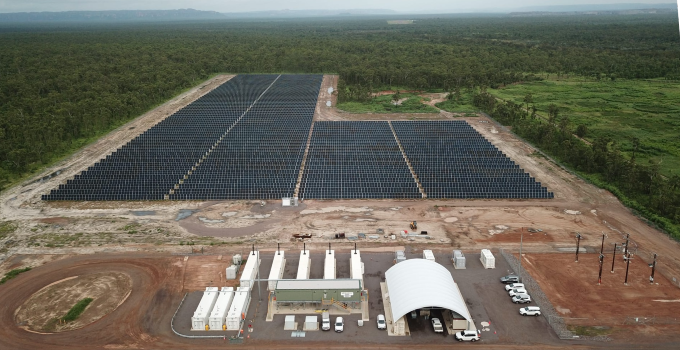
With the evolution of modern inverter and renewable energy technologies, it’s become possible to build microgrids with very high renewable penetration. These renewable solutions are revolutionising electricity sustainability, reliability and access in many far-flung locations – such as Pacific islands, remote locations around Australia, and on mining sites.
High renewable penetration allows operators of off-grid microgrids to extract maximum value from their installed solar, wind or other renewable generation while minimising the use of fossil fuels, such as diesel. It’s a win-win for the financial bottom line and emissions-reduction goals. If the microgrid connects with a broader power system, the benefits of reducing reliance on externally sourced energy are significant too.
Establishing a relatively simple microgrid with modest fuel-saving targets doesn’t have to be particularly complex. It’s within the reach of current technology and practice to be able to optimise microgrids to all but eliminate the use of fossil fuel (with the related advantages of eliminating fuel handling, shipping, etc.). However, careful thought must be given to the distinct nature of the microgrid: its customers, energy sources and storage options.
To make a microgrid successful, some technical challenges will need to be managed. Resolving these challenges in a cost-effective way becomes more difficult as the renewable energy balance approaches 100% – but they’re not insurmountable. Let’s explore.
Challenge 1: Ensuring quality of supply and an acceptable customer experience
The small size of microgrids and the fact that they are usually dedicated to a single ‘customer’ makes engineering a microgrid a sensitive task. While larger grids can operate with tight voltage and frequency tolerances and multiple levels of redundancy, microgrids often cannot. This inevitably means negotiating acceptable system standards for islanded operation that are within the tolerance of customers’ equipment and expectations. Microgrids powered by fossil fuels typically have more difficulty maintaining tight frequency and voltage tolerances than renewables-based microgrids.
Understanding customer and stakeholder expectations relating to reliability and robustness (energy availability and the ability to ride-through faults) is key to the establishment of a successful microgrid. Where the microgrid exists with no possibility of interconnection to another power network (i.e. in an ‘island’), there is more flexibility and less operational complexity. Discerning acceptable standards and practices is still not easy but it can be a more productive discussion than when the microgrid must comply with less tailored standards due to interconnection.
When the microgrid is interconnected, many of the technical requirements for the microgrid will be specified and/or mandated by the network service provider, electricity code requirements, and some operational requirements for electrical safety. If additional communication and inter-tripping with network equipment remote to the microgrid are required, these can add further complexity.
Challenge 2: Managing different modes of operation requiring different controls
In the previous section, we discussed how complicated it is to determine system standards. A great deal of care is also needed when contemplating which standards and controls are most appropriate to the microgrid’s specific characteristics. This is where cookie-cutter solutions could under-deliver and a more insightful approach is required.
A microgrid must manage the voltage, frequency and quality of supply while it is islanded as well as during periods of interconnection. Islands can remain satisfactory for longer if there are energy sources, storage and load controls within the island. Each of these elements comes at a cost and, depending on the frequency and duration of islanded operation, must have a value outside of the islanded scenario.
Our experience with microgrids is that semi-autonomous operation of each of the power sources using standard power system control approaches (solar, BESS and other power sources on voltage and frequency droop control) leads to the simplest and most secure response to transients (load or generation trips, network or network faults). Slower controls can be put in place to balance generation and rates of battery charge or discharge. If the battery power rating is large enough relative to the largest disturbance, it can manage most frequency disturbances within acceptable limits. If the battery energy capacity is large enough, it can always maintain a state of charge that allows fast reaction to variations in customer demand or VRE. Alternatively, auxiliary plant such as switched resistors, synchronous condensers and customer-level load control can be used to minimise battery power, storage and other energy inputs.
Operating microgrids in different modes requires careful engineering of the controls and equipment. The solutions and approaches described above have proven successful across multiple projects, but the key is to always be open to new solutions as new problems arise or new technologies emerge.
Challenge 3: Understanding the marginal value of resistors, synchronous condensers and/or demand management
Auxiliary equipment can help to extend the range and effectiveness of a microgrid to rely solely on renewable energy. The challenge is to understand the actual value of extension in this context. Where it has a direct bearing on fossil fuel use, the benefits are clear. Where it might cause an incremental improvement in the robustness of the islanded operation only, it’s important to consider whether any operational benefits or security benefits gained from the additional capital investment are valuable enough to justify the cost.
If the robustness of islanded operation is to be increased by managing customer demand, customer storage and/or embedded generation (e.g. rooftop solar), the value of the extended island longevity should be weighed against the perceived cost (direct or indirect) to the customer. This requires careful consideration of the diversity within the community, their openness to energy management, and the relationship between true costs and benefits.
Microgrids that maximise local use of renewable resources represent a relatively cost-effective option for lowering carbon emissions and/or reducing energy costs. Isolated communities, remote industrial sites, unreliably connected rural communities and others could benefit greatly from considering microgrid opportunities.
Entura has a long history of design, formation and operation of microgrids throughout Australia (such as King Island, Flinders Island, Rottnest Island, and at mining sites such as the Agnew gold mine) and in the Pacific region (including the Cook Islands, the Federated States of Micronesia, Tonga, and the Solomon Islands, to name just a few). We’ve seen the real benefits these systems bring to our clients and communities.
Contact us if you’re interested in unlocking the full potential of microgrids for your operation or community, or if you’re interested in ways to increase your use of renewable energy.
ABOUT THE AUTHORS
Donald Vaughan has over 20 years’ experience providing advice on regulatory and technical requirements for generators, substations and transmission systems. He has worked for all areas of the electrical industry, including generators, equipment suppliers, customers, NSPs and market operators. Donald specialises in the performance of power systems. His experience in generating units, governors and excitation systems provides a helpful perspective on how the physical electrical network behaves.
Greg Koppens is Entura’s Principal Control Engineer Hybrid Renewable Systems and has led Entura’s secondary electrical engineering team. Greg’s experience spans power, oil and gas, and mining, including onsite roles. With over a decade of detailed design experience, Greg facilitates collaboration between engineering disciplines and other stakeholders to solve complex problems. He regularly shares his extensive expertise with the mining sector to advance their decarbonisation goals. Find out more about Greg in our podcast series here.
We built this synchronicity … but what now?
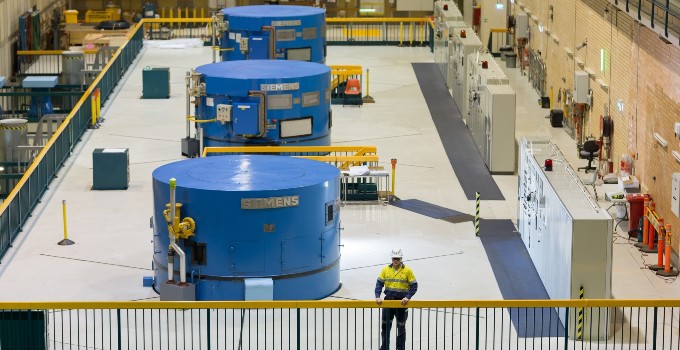
The alternating current (AC) transmission age started in 1891 through collaboration and perseverance. This transmission method has transformed the world, led us to the brink (or over the brink) of a climate disaster, and provides the backbone for a future founded on abundant renewable resources (in Australia, at least). Collaboration and perseverance are now required to ensure the continued utility of the grid.
Synchronous machines have always been the driving force in the grid. These elegantly simple electrical machines sit in powerhouses around the globe using their century-old technology (nearly 150 years, in fact) to convert mechanical energy into electrical energy to power the computer that I’m using to type this.
There’s a romance to these machines. It’s more than nostalgia. They spin, as the name suggests, in synchronism. If one of them falters, all the rest pick up the slack. The only connection they need is the power lines. This robustness is central to the way our electricity grids have operated for over 130 years – but the influence of synchronous machines is slowly being eroded.
The most obvious erosion of the influence of synchronous machines is their displacement by inverter-based renewable (IBR) technologies as solar, wind and battery energy storage (BESS) installations proliferate. A less obvious erosion of their influence is the diminishing understanding and appreciation of synchronous technology within the industry. This lack of understanding by engineers, planners and regulators of the fundamental building blocks of the electricity grid is starting to show.
This might sound like the curmudgeonly ranting of yesterday’s engineer as technology passes them by. Maybe it is … but, rather than dwell on negatives, let’s look at what synchronous machines bring to the power system.
- System strength
The fundamental difference between synchronous machines and IBR is thermal inertia. Typical synchronous machine design can sustain high levels of over-current for a relatively long time (seconds) compared to IBR units (milliseconds). This difference allows synchronous machines to provide a strong ‘natural’ response to voltage variations in the power system without threat of overload and damage. Transmission protection systems – and therefore grid security and safety – rely on this characteristic.
There are alternatives. Overload capacity can be built into inverters, but this is expensive. Dedicated inverter-based devices such as static synchronous compensators (STATCOMs) can be used to provide fault response.
- Inertia
Synchronous machines spin. Their spinning bits (rotors) have mass, so they have mechanical inertia. This mechanical inertia doesn’t require a control system to provide an inertial response. The inertial response from a synchronous machine is a known, predictable quantity, regardless of voltage.
IBRs can provide synthetic inertia and, when voltage is healthy, can out-perform synchronous units. When voltage is not nominal, the same current limitations that affect the IBRs’ ability to deliver fault level can also restrict the effectiveness of synthetic inertia delivery.
- Robustness
The previous two characteristics – system strength and inertia – show the support that synchronous machines can provide to the power system during disturbances. The synchronous machine can deliver these supports across a wide range of power system disturbances to voltage and frequency.
IBRs typically rely on fast controls to manage their response to system disturbances. Under some extreme conditions these controls may not be fast enough or well enough tuned to manage. While tuning is important to synchronous machine performance, often it has a second-order effect or adds robustness over and above the natural response.
Displaced but not superseded
Understanding the inherent dynamics of synchronous machines gives power system engineers a better appreciation of these machines’ contribution to power system stability. Regulators should be mindful of the reduced risk (and mostly advantages) to system security that synchronous machines offer relative to IBRs. This is despite the uncontrollable nature of synchronous machines. That is, physics dictates the stabilising effects from synchronous machines whereas control algorithms determine whether an IBR can stabilise or destabilise. Controller model accuracy is therefore more important for IBRs than it is for synchronous machines where transient stability or electro-mechanical transient time frames are considered.
Better understanding of synchronous machines should lead to more appropriate rules relating to dynamic response to system events. Overly specific requirements for fault ride-through, power recovery post-fault, and maintenance of real and reactive power during voltage disturbances may all lead to needless protracted negotiations over access standards. This slows down the progress of the energy transition, frustrates otherwise helpful development, and diverts resources towards trivial considerations rather than focusing on issues of greater importance.
Synchronous machines will play a role in the energy grid of the future. Our industry needs to maintain expertise and regulatory frameworks that allow this technology to continue providing the grid with vital stabilisation and robustness.
ABOUT THE AUTHOR
Donald has over 20 years’ experience providing advice on regulatory and technical requirements for generators, substations and transmission systems. He has worked for all areas of the electrical industry, including generators, equipment suppliers, customers, NSPs and market operators. Donald specialises in the performance of power systems. His experience in generating units, governors and excitation systems provides a helpful perspective on how the physical electrical network behaves.
‘Dams for People, Water, Environment and Development’ – some reflections from ICOLD 2024
Entura’s Amanda Ashworth (Managing Director) and Richard Herweynen (Technical Director, Water) recently attended the International Commission on Large Dams (ICOLD) 2024 Annual Meeting and International Symposium, held in New Delhi. Amanda presented on building dam safety capability, skills and competencies, while Richard presented on Hydro Tasmania’s risk-based, systems approach to dam safety management, and the importance of pumped hydro in Australia’s energy transition.
Here they share some reflections on ICOLD 2024 …
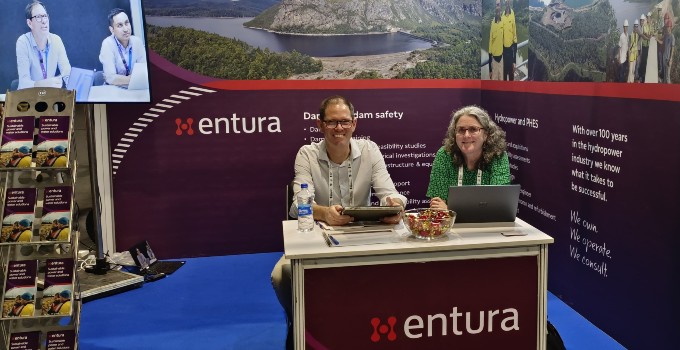
Richard Herweynen – on the value of storage, ‘right dams’, and stewardship
At ICOLD 2024 we were reminded again that water storages will be critical for the world’s ability to deal with climate change and meet the growing global population’s needs for food and water. We can expect greater climate variability and therefore more variability in river flows, which means that more storage will be needed to ensure a high level of reliability of water supply. Without more water storages to buffer climate impacts, heavily water-dependent sectors like agriculture will be impacted.
To slow the rate of climate change, we must decarbonise our economies – but without significant energy storage, it will be difficult to transition from thermal power to variable renewable energy (wind and solar). Pablo Valverde, representing the International Hydropower Association (IHA), said at the conference that ‘storage is the hidden crisis within the crisis’. There was a lot of discussion at ICOLD 2024 about pumped hydro energy storage as a promising part of the solution. It is also important, however, to remember that conventional hydropower, with significant water storage, can be repurposed operationally to provide a firming role too. Water storage is the biggest ‘battery’ of the world and will be a critical element in the energy transition.
With the title of the ICOLD Symposium being ‘Dams for People, Water, Environment and Development’, I reflected again on the need for ‘right dams’ rather than ‘no dams’. ‘Right dams’ are those that achieve a balance among people, water, environment and development. In the opening address, we were reminded of the links between ‘ecology’ and ‘economy’ – which are not only connected by their linguistic roots but also by the dependence of any successful economy on the natural environment. It is our ethical responsibility to manage the environment with care.
When planning and designing water storages, we must recognise that a river provides ecological services and that affected people should be engaged and involved in achieving the right balance. If appropriate project sites are selected and designs strive to mitigate impacts, it is possible for a dam project’s positive contribution to be greater than its environmental impact, as was showcased in number of projects presented at the ICOLD gathering. Finding the balance is our challenge as dam engineers.
The president of ICOLD, Michel Lino, reminded delegates that the safety of dams has always been ICOLD’s focus, and that there is more to be done to improve dam safety around the world. At one session, Piotr Sliwinski discussed the Topola Dam in Poland, which failed during recent floods due to overtopping of the emergency spillway. Sharing and learning together from such experiences is an important benefit of participating in the ICOLD community.
Alejandro Pujol from Argentina, who chaired one of the ‘Dam Safety Management and Engineering’ sessions, reflected that in ICOLD’s early years the focus was on better ways to design and construct new dams, but the spotlight has now shifted to the long-term health of existing dams. It is critical that dams remain safe throughout the challenges that nature delivers, from floods to earthquakes. In reality, dams usually continue to operate long beyond their 80–100 year design life if they are structurally safe, as evidenced in the examples of long-lived dams presented by Martin Wieland from Switzerland. He suggested that the lifespan of well-designed, well-constructed, well-maintained and well-operated dams can even exceed 200 years. As dam engineers, no matter the part we play in the life of a dam, we have a responsibility to do it well.
From my conversations with a number of dam engineers representing the ICOLD Young Professional Forum (YPF), and seeing the progress of this body within the ICOLD community, I believe that the dam industry is in good hands – although, of course, there is always more to be done. I was pleased to see an Australian, Brandon Pearce, voted onto the ICOLD YPF Board.
Another YPF member, Sam Tudor from the UK, reminded us in his address of the importance of knowledge transfer, the moral obligation we all have especially to the downstream communities of our dams, and our stewardship role. He was referencing his experience of looking after dams that are more than 120 years old – all built long before he was born. Many of our colleagues across Entura and Hydro Tasmania feel this same sense of responsibility and pride when we work on Hydro Tasmania’s assets, which were built over more than a century and have been fundamental to shaping our state’s economy and delivering the quality of life we now enjoy. It is up to all of us to carry the positive legacy of these assets forward with care and custodianship, for the benefit of future generations.
Amanda Ashworth – on costs and benefits, dam safety, and an inclusive workforce
Like Richard, I found much food for thought at ICOLD 2024. For me, it reinforced the need to accelerate hydropower globally, particularly in places where the total resource is as yet underdeveloped. To do so, we will need regulatory frameworks that support success – such as by monetising storage and recognising it as an official use – and administrative reforms that ease the challenges of achieving planning approvals, grid connection agreements and financing for long-duration storage. We must encourage research and development to move our sector forward: from multi-energy hybrids to advanced construction materials and innovations to improve rehabilitation.
In particular, I’ve been reflecting on how our sector could extend our thinking and discourse about the impacts and benefits equation beyond the broad answer that dams are good for the net zero transition. How can we enact and communicate the many other potential local environmental and social benefits and long-term value from dams?
Much of the world’s existing critical infrastructure came at a significant financial expense as well as social and environmental costs – so it is our obligation to pay back that investment by maximising every dam’s effective life. When we invest in extending the lifespan of dam infrastructure through effective asset management and maintenance, and when we maximise generation or the value of storage in the market, we increase the ‘return on investment’ against the financial, social and environmental impacts incurred in the past.
Of course, the global dams community must continue to prioritise dam safety and work towards a ‘safety culture’. I was pleased to hear Debashree Mukherjee, Secretary of the Ministry of Jal Shakti, celebrate the progress on finalising regulations across states to enact India’s Federal Dam Safety Act and establishing two centres of excellence to lift capacity across the nation. Dam safety depends on well-trained people with the right skills and competencies to comply with evolving standards, apply new technologies, and respond effectively to changing operational circumstances and demands.
I also enjoyed hearing from ICOLD’s gender and diversity committee on its progress, including updates from around 14 nations on their efforts to build a more inclusive renewable energy and dams workforce. This is front of mind for us, as we step up Entura’s own focus and actions on gender equity throughout our business this year.
The challenges facing our dams community – and our planet – are enormous, but there is certainly much to be excited about, and we look forward to continuing these important conversations over the next year.
From Richard, Amanda and Entura’s team, many thanks to the Indian National Committee on Large Dams (INCOLD) for organising and hosting this year’s ICOLD event, supporting our sector to build international professional networks, and facilitating the sharing of experiences and knowledge across the globe – all of which are so important for growing the ‘ICOLD family’ and supporting a safer, more resilient and more sustainable water and energy future.
Growing the future of hydropower – observations from a career in the industry
Entura’s Senior Principal Hydropower, Flavio Campos, knows hydropower inside out. Flavio has recently joined Entura, after working around the world on significant hydropower projects ranging from 30 MW to a whopping 8,240 MW. We asked him to share some of his hydropower journey, what excites him about the future of the sector, and what’s different about conventional hydropower and pumped hydro in supporting the clean energy transition …
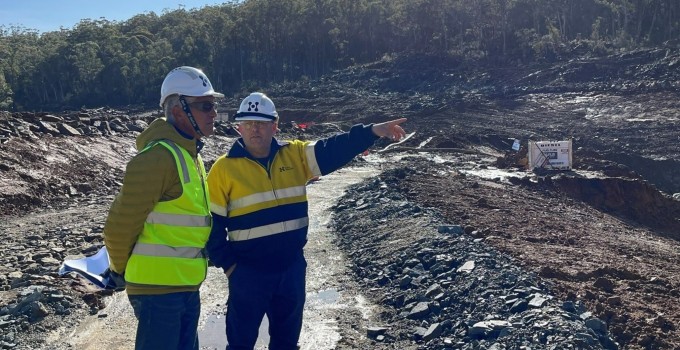
When I immigrated from Brazil to Canada in 2012, it was no accident that I settled in Ontario, near Niagara Falls. I had taken a job with a consulting firm that had a hydropower hub strategically located in the Niagara region due to its long history of hydropower.
The Niagara region is the home of the Adams Power Plant, completed in 1886 – the first alternating current (AC) power plant built at scale, delivering an installed capacity of 37 MW at 2,200 V. The voltage is stepped up by a transformer to 11,000 V, allowing for an economic transmission line reaching to the city of Buffalo, NY, 32 km away. The concept was launched by engineer Nikola Tesla in collaboration with George Westinghouse, beating Thomas Edison’s bid, which was based on a direct current (DC) system. Tesla’s dream of harnessing the awesome power of Niagara Falls was realised by the end of the 19th century, when hundreds of small hydropower plants emerged and multiple forms of electricity utilisation spread across the world.
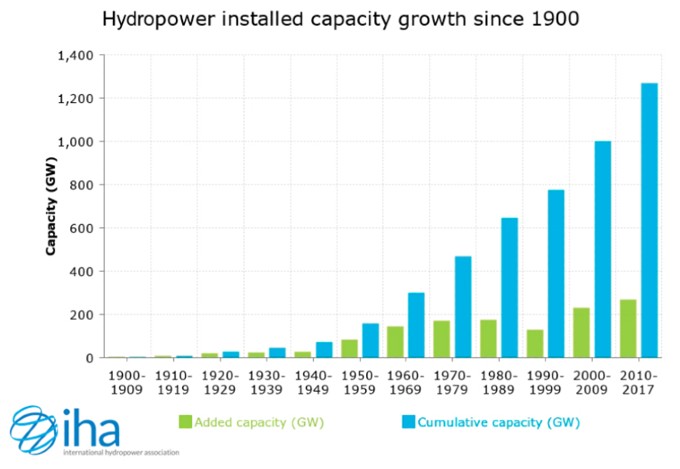
The hydropower boom, led by Brazil and China
When I started my career in the hydropower industry in 1995, I could feel the ongoing impact of the great hydropower boom that was led by Brazil and China through the 1970s and 1980s. In 1999, I was construction manager for Tucurui Dam, one of the biggest hydropower plants in Brazil and the world at that time (now ranked 8th in the world), delivering a total installed capacity of 8,240 MW. As part of my role, in order to raise production to the expected rates, I was able to visit China’s Three Gorges Dam during construction and learn about their techniques and massive concrete operations.
In the 1990s, Brazil’s hydropower industry had plenty of experienced professionals, from construction trading foremen and general superintendents to highly educated engineering professionals from whom I had the privilege to learn.
Since those glorious decades, global hydropower capacity has increased significantly. The strongest period was 2007 to 2016, when more than 30 GW was added per year on average. Since 2017, the industry has slumped to only 22 GW per year on average, with only 13.7 GW installed in 2023. However, it is interesting that of the new 13.7 GW, 6.5 GW was delivered as pumped hydro energy storage.
A new wave of pumped hydro
At a HydroVision International conference in Portland, Oregon, in 2019, I noticed that pumped hydro was a significant topic of discussion. The conference highlighted several factors making pumped hydro projects attractive for the clean energy transition: the ‘battery’ feature itself which helps to balance supply and demand, its contributions to grid stability, its lower environmental impact compared to conventional hydropower, the availability and efficiency of variable-speed units, and the cost comparison against other types of batteries.
Projections of a new wave of pumped storage soon evolved from conference coffee-break chatter to reality: in 2022, more than 10 GW of pumped hydro was delivered, the most ever achieved by the industry. Most of this has been delivered in China, where top-down policies imposed by government can deliver rapid results. Other countries operating on a more open-market basis need to improve the mechanisms to foster pumped hydro so that it can support the grid effectively as other variable renewable energy (VRE) sources, such as wind and solar, proliferate.
There is now consensus that pumped hydro is a necessity for grids to cope with increasing amounts of VRE– and the need is urgent. Pumped hydro, however, requires significant upfront investment in civil works and time to implement. Studies by the IHA indicate that besides the inherent need for additional pumped storage in the grid, the world’s conventional (non-pumped) hydropower installed capacity must double by 2050 in order to achieve net-zero transition targets. This will be challenging, given such a low level of new hydropower worldwide in recent years, and the fact that the most attractive sites have been already developed.
There is also opportunity to re-imagine existing conventional hydropower plants to make the most of their natural battery and firming potential – by operating flexibly to support firming VRE rather than generating for maximum volume. Even where there is no market mechanism to specifically monetise this value, it could be rewarded for national or regional outcomes.
How can we achieve the much-needed growth in conventional hydro and pumped hydro?
Conventional (non-pumped) hydropower has long been recognised for clean energy and the long life of the infrastructure. The challenge now is to identify, gain approvals and sustainably deliver new projects in a world where human occupation is growing fast and reaching into the most remote corners of watersheds. Governments and regulators must assess cost benefits against the social and environmental impacts before giving the green light to new hydropower projects.
Developing pumped hydro can be more flexible, especially when it is a closed-loop system that doesn’t depend on water flows, except for first-time filling and for topping up the losses caused by evaporation. Pumped hydro is not new – in fact, it has existed for more than a century. What is new, however, is the challenge of fostering pumped hydro development at the rate needed.
The IHA has helped clarify what is needed for the industry to develop pumped hydro faster. The IHA’s Guidance Note delivers recommendations to reduce risks and enhance certainty, supporting market players to better understand the issues.
Another interesting initiative in the hydropower journey is XFLEX Hydro, a European initiative which brought together 19 entities such as IHA, EDP, EDF, Alpiq, Bechtel and others, with the objective of increasing hydropower capabilities and flexibility to cope with changing grid profiles. X-Flex has launched 7 pilot projects already – and 4 of these are pumped hydro. This combined initiative has illustrated two important areas of focus that can benefit market players and accelerate uptake:
- The need for a supportive regulatory regime: Policy-makers and other stakeholders need to facilitate the development of regulations or market mechanisms that fairly compensate pumped hydro, as well as conventional hydropower, such as ‘price cap and floor’ mechanisms, compensation for stability features provided by hydropower, and expediting the approval process while ensuring that social and environmental impacts are minimised and mitigated.
- The advantages of evolving technologies, including:
- variable-speed units, increasing flexibility
- hydraulic short-circuit operation, in which the plant can pump and generate simultaneously
- hydro/battery hybrid system, in which the battery works along with hydropower and enhances plant flexibility
- digital/AI control platforms, which can improve the overall grid efficiency and reduce downtime.
Hydropower for a better future
The challenges of rapidly building out new conventional hydropower and pumped hydro are huge. Yet, where there is a will, there is a way. Those of us who understand and believe in the benefits of conventional hydropower and pumped hydro have a duty to bring communities along on the journey and to help build a better future for the next generations.
We look forward to bringing you more of Flavio’s insights into conventional hydropower and pumped hydro in future articles. Flavio is currently contributing to a number of Entura’s assignments including supervising construction on the Genex Kidston PHES project in Queensland, for which Entura is the Owner’s Engineer, and being a key adviser on the Tarraleah upgrade as part of Hydro Tasmania’s Battery of the Nation program.
Understanding the business risks of small dams and weirs
Small dams may pose significant business risks that are often under-appreciated, even if these dams don’t pose a safety risk to the community. Managing risk is a key part of running any sustainable business and understanding how to mitigate risks requires that they are properly identified, analysed and evaluated.
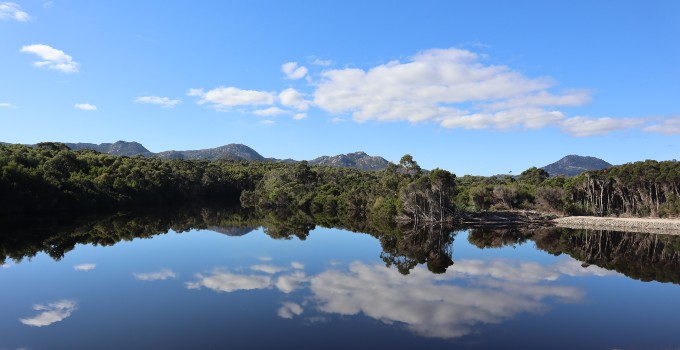
The Guidelines on Risk Assessment prepared by ANCOLD (Australian National Committee on Large Dams) provides a detailed process for quantitative analysis of dam safety risks for large high-consequence dams, but adopting this process for small dams and weirs can be costly and may not be clearly justifiable.
For owners of small dams, ANCOLD has a number of other guidelines that can be useful for managing these dams, including Guidelines on the Consequence Categories for Dams and Guidelines on Dam Safety Management. Assigning a consequence category for a small dam can be a useful first step in understanding the risks – and will consider the impacts on community safety, on the environment, on the dam owner’s business, and on other social factors including impacts on health, community and business dislocation, loss of employment and damage to recreational facilities and heritage.
The consequence categories are graded from ‘Low’ to ‘Extreme’. These categories are used for a number of purposes including:
- regulatory requirements (depending on which state the dam is in)
- recommended surveillance and monitoring activities
- maintenance and operational requirements
- spillway flood capacity
- dam design standards.
The focus of ANCOLD’s consequence category guidelines is on wider community safety and impacts, but not on the dam owner’s business. This potentially leaves the dam owner exposed to significant unidentified business risks. Ideally, these should be managed consistently alongside all the other business risks.
A structured approach to assessing the business risks of small dams
ANCOLD’s Guidelines on Risk Assessment is a useful starting point for undertaking a business-focused risk assessment of small dam assets. As with all risk assessments, it is useful to follow a structured approach, including the following steps:
- identify the hazards
- brainstorm the failure modes
- estimate the likelihood of the failure
- estimate the consequences of failure
- evaluate the risks
- develop risk mitigation measures.
Such a risk assessment approach is ideally completed with a dam engineer working closely with the business owner to capture both the dam engineering and the business-specific knowledge.
1. Hazards
Dams need to be properly designed, constructed and maintained to continue to perform their function safely. It is essential to avoid becoming complacent. Floods are a significant hazard to all dams and cause around 50% of all failures in large, well-engineered embankment dams. Small dams are often constructed with no or minimal engineering input into the design or construction and as a result may have inherent defects that may not manifest themselves until years later.
Dams in general do not require a lot of maintenance; however, a lack of suitable maintenance can lead to failures. A key maintenance activity is management of vegetation so that trees do not establish themselves in the embankment. Tree roots can create leakage paths that could lead to piping or internal erosion, and ultimately to a failure.
2. Failure modes
A key part of the expertise of a dams engineer is understanding how different types of dams can fail, which is crucial for identifying potential failure modes. The ANCOLD guidelines on risk assessment recommend completing a site inspection of the dam to help identify the key ways in which the dam could fail. The inspection should be conducted with the dam owner to look for evidence of failure modes, such as:
- deformation or cracking, which may indicate issues with the stability of the dam
- wet areas or flows through the dam, which may indicate a piping failure
- spillways where the original crest is filled in or raised to increase storage in the reservoir, which can often be an area of concern
- erosion close to the dam from operation of the spillway, which could lead to undermining and instability of the dam wall.
Typically, failure modes are identified in a workshop setting and then prioritised by criticality. The full list of failure modes is then reduced to a shortlist of those that are most critical.
3. Likelihood of failure
ANCOLD’s Guidelines on Risk Assessment provides an approach that can be used for detailed quantitative risk assessments; however, such approaches require significant effort to apply and can be costly. For small dams, it can be more appropriate to use a risk matrix approach, similar to that outlined in the Australian standard AS ISO 31000 Risk Management.
Typically, most businesses have a standard risk assessment procedure that can be adapted to give a qualitative or semi-qualitative assessment of likelihood. An experienced dams engineer will be able to assign a likelihood for each of the credible failure modes based on engineering judgement and some simple calculations (e.g. using regional flood estimates and estimates of the spillway discharge capacity). Failure modes for dams that are well designed and constructed will often have a likelihood rating of ‘Rare’ or ‘Unlikely’. The likelihood may be higher for dams in poor condition or with identified deficiencies.
4. Consequences of failure
A business risk assessment focuses on the consequences to the business, rather than the wider community, if the small dam were to fail. This will be unique to each business and will need input from the owner. It can be assessed by working through a series of questions about the need for the dam and its purpose – for example:
- What is the water in the dam used for? Can the business function without the water or the storage space in the dam?
- Are there alternative sources for the water that can be quickly accessed, and will these be sufficient for normal operations or would it be necessary to reduce operation?
- Is there business infrastructure downstream of the dam, and could a failure of the dam cause failure of these assets (e.g. pumping stations, water treatment plants or other dams) that would impact business operations? Can the business operate without these assets?
- How will customers be affected and what are the reputational consequences of not being able to supply or only partially supply?
- What are the financial implications for the business, and is there insurance that would cover the cost of the event, including consequential losses?
- How long would it take to replace the dam (including refilling) and the other assets?
5. Evaluation of risks
Using the business’s standard risk assessment tool enables comparison of the small dam risks against other business risks on a consistent basis (e.g. safety risks to employees). The level of risk will indicate the urgency of addressing the risk. This process allows a clearly articulated justification to be presented to the business for putting in place any required mitigations. It also enables the owner to focus on the key business risks rather than become distracted by issues with lower risk.
6. Risk mitigation
Mitigations can address either likelihood or consequences and will need to be tailored to the specific risks and the business needs. Addressing the risks by reducing the likelihood will typically involve physical works to the dam – for example, increasing the size of the spillway to reduce the likelihood of an overtopping failure, or managing vegetation to reduce the likelihood of a piping failure.
Where reducing the likelihood is not practical or not sufficient, addressing the consequences may be an effective approach. Addressing the consequences may involve options such as securing alternative water supplies, contingency planning to reduce impacts on customers, or insurance to cover the financial losses.
Bringing it all together for better business insights
Entura has undertaken qualitative and semi-qualitative small dam risk assessments for a number of clients in a cooperative environment to bring together our dams engineering expertise with the owner’s knowledge of their business. This is a cost-effective approach that has provided clarity on the specific business risks related to small dams, allowing targeted risk mitigation measures to be put in place. The process has provided important insights enabling owners to justify business decisions and reduce their overall business risk exposure.
If you have small dams and would like to talk with us about assessing your business risks, contact Phillip Ellerton or Richard Herweynen.
About the author
Paul Southcott is Entura’s Senior Principal – Dams and Headworks. Paul has an outstanding depth of knowledge and skill developed over more than 3 decades in the fields of civil and dam engineering. He is a highly respected dams specialist and was recognised as Tasmania’s Professional Engineer of the Year in Engineers Australia’s 2021 Engineering Excellence Awards. Paul has contributed to many major dam and hydropower projects in Australia and abroad, including Tasmania’s ‘Battery of the Nation’, the Tarraleah hydropower scheme, Snowy Hydro, and numerous programs of work for water utilities including SeqWater, Sun Water and SAWater. His expertise is a crucial part of Entura’s ongoing support for upgrade and safety works for Hydro Tasmania’s and TasWater’s extensive dams portfolios. Paul is passionate about furthering the engineering profession through knowledge sharing, and has supported many young and emerging engineers through training and mentoring.