How hydropower history and innovation can continue to power progress
Having been named as the Planning Institute of Australia’s Young Planner of the Year for 2024 and awarded a bursary, Entura’s Bunfu Yu travelled through Switzerland and France to study hydropower and energy innovation. Her reflections from the study tour highlight how history-rich hydropower assets can continue to evolve and add value in a changing world …
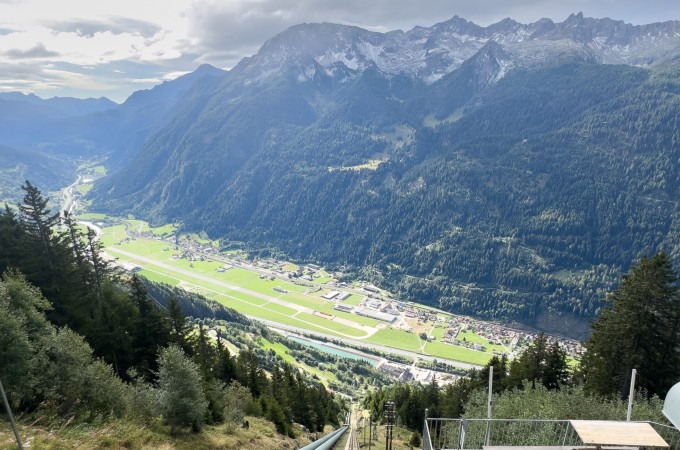
Switzerland’s Ritom hydropower project – which is in the late stages of a major redevelopment and anticipated to be operational later in 2025 – is a technical marvel of the past and the present. It is also a lesson in how energy infrastructure can evolve while still respecting its historical roots.
The original Ritom power station was commissioned in 1920 as part of a traditional hydropower scheme using water from Lake Ritom to generate electricity. It holds a special place in Swiss energy history as the first plant to supply electricity to the Gotthard railway, which is a vital north–south transit corridor through the Alps. This early integration of hydropower with transport infrastructure helped shape the modern Swiss energy landscape.
However, after more than a century of faithful service, Ritom’s aging infrastructure and the region’s changing energy needs prompted a major rethink.
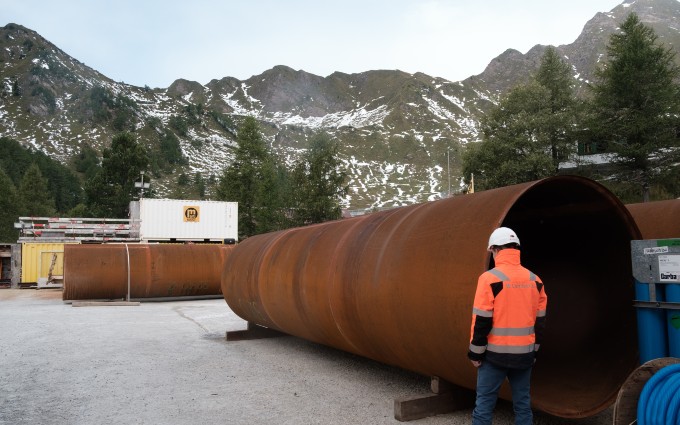
Modernising with purpose
Ritom is undergoing a major transformation to meet 21st century demands. The redevelopment project involves replacing the historic hydropower plant with modern facilities and converting it from a conventional hydropower scheme to include a pumped hydropower component. By using two existing lakes (Lake Ritom and Lago di Cadagno) as the upper and lower reservoirs, energy can be stored by pumping water uphill during periods of low demand and releasing it to generate electricity when demand peaks. This is critical for maintaining reliability and stability in today’s dynamic grid. The lakes are also popular with walkers, and this recreational value will continue alongside the repurposed scheme.
The revamped facility will increase capacity to 120 MW, improving energy resilience for both the local Ticino region and the Swiss Federal Railways. The upgrade enhances energy security and does so with a strong emphasis on environmental and community values.
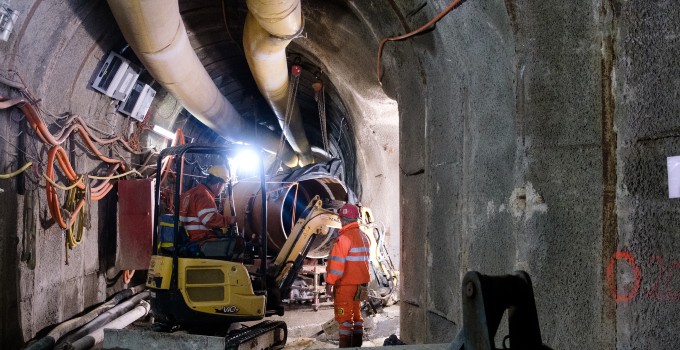
Balancing environment, engineering and community
Like all major infrastructure projects, Ritom has complexities. A key concern is managing downstream water flow to protect river ecosystems. To address this, the project incorporates a demodulation basin – an engineered feature that moderates flow variations, preserving the ecological health of the river below.
Minimising disruption for the local community during construction has also been a priority. This has taken careful management, as the project is nestled between the alpine villages of Piotta and Piora. The project team constructed a dedicated cableway to move heavy materials – such as massive steel penstocks – away from narrow local roads. This solution reduced construction traffic and helped preserve the peace and safety of surrounding communities.
Ritom is an inspiring example of how infrastructure can evolve when regulators, engineers and communities work together. Innovative thinking coupled with flexibility in permitting has enabled tailored solutions that are practical and environmentally sound – an approach that is replicable worldwide.
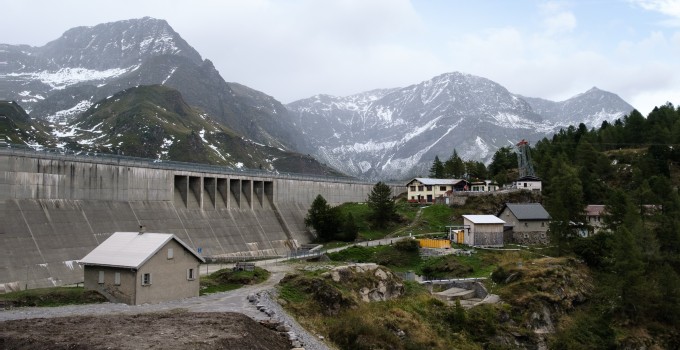
Technical excellence delivering long-term social value
Ritom reminds us that great infrastructure is more than engineering and functionality – it can inspire and be enjoyed.
Each year, the region celebrates the connection between nature, people and infrastructure through the ‘Stairways to Heaven’ race – a brutal yet iconic event that ascends 4,261 steps alongside the original penstocks of the Ritom scheme. With an average 89% incline over 1.2 km, it is Europe’s steepest race, attracting elite athletes as well as daring locals. The climb is physically punishing, but those who reach the summit are rewarded with breathtaking panoramic views of the Swiss Alps and the glistening Ritom reservoir.
This race is more than a sporting challenge. It is a symbol of how infrastructure can become deeply woven into the identity of a community, engendering enduring pride and delivering long-term social value well beyond its technical purpose.
The Ritom project is a powerful reminder that the future of energy lies in more than technology alone, but in how we carefully and intentionally navigate the intersections and synergies of history, environment and communities.
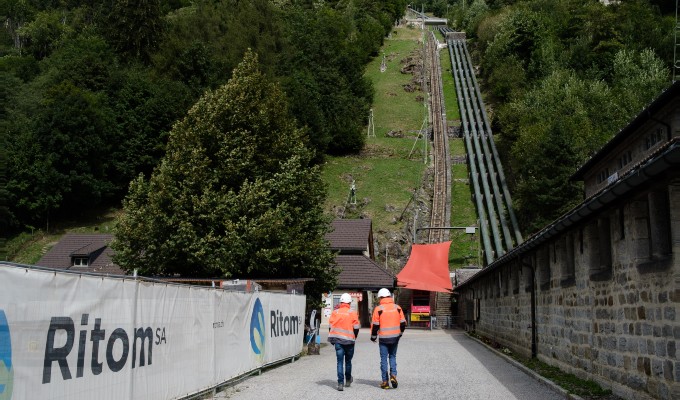
Planning for progress
Redeveloping or repurposing long-standing hydropower assets demands more than engineering expertise – it requires sensitivity to contemporary expectations. Since many of these projects were first built, the regulatory environment has shifted dramatically, with much greater emphasis on biodiversity protection (terrestrial and aquatic), climate resilience, the voices of local communities, and the cultural and heritage values of the Country on which these projects have been developed. The best projects don’t treat these as hurdles, but as opportunities to build broader value into the asset’s future.
Making good decisions at the earliest stages of refurbishment, repurposing or redevelopment is critical. To ensure lasting benefits, projects will need clear strategies grounded in sound technical evidence and shaped by a strong understanding of regulatory requirements and community expectations. Long-term success is more likely when projects are not only viewed through the technical lens of extending asset life, but are reimagined with community and environment at their core. Hydropower projects such as these can be catalysts for long-term energy security, greater ecological stewardship, strengthened social outcomes, and even become a source of community pride and inspiration.
In Australia, Entura is working with Hydro Tasmania to apply these principles through our work on the redevelopment of the Tarraleah hydropower scheme, parts of which are more than 80 years old. The redevelopment aims to increase capacity and flexibility so that Tarraleah can better serve the needs of the changing energy market – and future generations. It’s a project that echoes Ritom’s lesson: that heritage and innovation can coexist to create modern, sustainable infrastructure with value that endures for generations. By striking the right balance, hydropower can continue to do what it has always done best – power progress – while also meeting the needs and values of communities and environments today and long into the future.
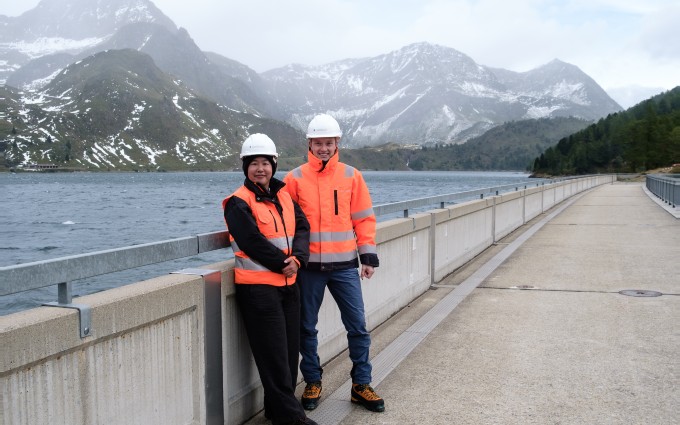
Bunfu (above left) thanks Lombardi Engineering Switzerland for organising a comprehensive on-site tour of the Ritom hydropower project.
ABOUT THE AUTHOR
Bunfu Yu is a dynamic young leader in renewable energy planning, approvals, and business development. Bunfu played a pivotal role in Entura’s Environment and Planning Team’s success in achieving the Planning Institute of Australia’s National Award for Stakeholder Engagement in 2024. In 2023, Bunfu was named the National Young Planner of the Year by the Planning Institute of Australia. This honour recognised not only her passion for the planning and delivery of renewable infrastructure but also her active contribution to the profession through mentoring, public engagement, and knowledge sharing. She is currently a Senior Environmental Planner and a Business Development Manager at Entura, having joined the business as a Graduate Planner in 2018.
What to consider when you’re thinking about a synchronous condenser
Depending on when and where you want to connect your new solar farm or wind farm, the network service provider or your consultant may tell you that you’ll need a synchronous condenser. That may not be good news, because these machines don’t come cheap and they usually don’t provide a direct revenue stream. What should you do next?
Do you understand why you need a synchronous condenser?
The first step is to understand why you need the synchronous condenser. The inverters at the heart of most solar farms and most modern wind turbines need a strong electricity grid to push their energy into. If the network is not strong, the inverter is likely to fail to switch at the required times, swing against the power system like a pendulum, and distort the waveform, causing harmonics. The synchronous condenser overcomes this, strengthening the power system in the local area by forcing the network voltage into a near-perfect sine wave of the required size.
The rules have changed!
The burden for providing system strength in Australia’s National Electricity Market has shifted significantly. Previously, new generators bore the primary responsibility under a ‘do no harm’ principle.
As of December 2022, ‘transmission network service providers’ (TNSPs) became ‘system strength service providers’ (SSSPs) and are now responsible for proactively providing a baseline of system strength across their networks.
Furthermore, new connecting parties now face new access standards and ‘system strength mitigation requirements’. This framework offers generators two clear choices to address their system strength impact: (1) pay a system strength charge, which is a fee reflecting the cost for the SSSP to provide the necessary system strength, or (2) self-remediate by installing their own solutions, such as synchronous condensers or grid‑forming inverters, to mitigate their impact.
At Entura, our experience so far indicates that many generators are actively exploring the self‑remediation option, prioritising operating cost over capex for their project.
Self-remediation may mean using synchronous condensers. However, there are also other solutions to system strength, which we’ll discuss below.
Is it possible to predict the need for a synchronous condenser earlier?
There are ways that you can predict at the project pre-feasibility stage that a synchronous condenser might be needed, before the network service provider becomes involved. Take a look at other renewable energy installations that have been constructed recently in the same region; if they needed a synchronous condenser, you almost certainly will too.
Consider where the installation is in the grid. If the answer to any of the following questions is yes, you will likely need a synchronous condenser: Is your installation remote from all traditional generating stations? Has a large traditional generator shut down in the area recently? Are other generators in the area routinely constrained due to network stability challenges?
Simple calculations can be completed based on information that most network service providers publish on their websites, including network constraints and fault levels. These calculations aren’t always definitive, but they will offer significant insight.
What do you need to specify?
It is best to specify the exact function that the synchronous condenser must achieve. Typically, this means specifying the fault current contribution that is required from the machine and leaving it up to the manufacturer to decide the optimal machine design including the headline MVA rating. Once these headline values have been determined, consider the following questions, each of which has a substantial cost impact:
- How much reactive power do you need the synchronous condenser to absorb? Typically these machines can only absorb approximately half of their headline rating, so don’t ask for too much unless you have deep pockets.
- Do you really need inertia that is greater than the manufacturer’s standard? Synchronous condensers are known for having inertia, but asking for inertia that is greater than the manufacturer’s standard will result in substantial additional cost and usually results in no additional revenue stream.
- The synchronous condenser is being installed to provide system strength, so do you really want it to be able to supply reactive power indefinitely? Perhaps 60 seconds would be enough.
- What are the impacts of planned or unplanned outages of the synchronous condenser? Do these impacts warrant increased redundancy or spares retention? We’ll talk about this in more detail below.
Are some cost savings not worth making?
For a synchronous condenser project, there are some measures that, on the surface, might appear to be potential cost-saving considerations. Can you omit the transformer tap changer? Could the cooling equipment be downsized or even omitted? Can you connect to the station 33 kV busbar? Detailed analysis is needed to answer these questions definitively. In our experience, however, the answers to each question have been emphatically no.
If you need the synchronous condenser to operate close to its rated reactive power absorption limit, you’ll need a transformer tap changer. Similarly, if the machine connects to a 33 kV busbar, fault levels will become unreasonable and an even larger machine will be required.
What’s the best contracting model?
Your choice of contracting model will depend on your appetite for risk and the sensitivity of your schedule. A typical solar or wind farm project is very schedule-sensitive, which suits an all-inclusive turnkey project delivery including everything from civil foundations, fencing and drainage through to integration with the farm’s control system. But this delivery mode comes at a price, and there are few Tier-1 equipment suppliers prepared to take on this model. The lowest-cost suppliers will be likely to want to put your machine onto a ship, point it in your general direction, and send you the invoice.
Whatever your contracting model, one of the largest risks to projects is the adequacy of the power system models. You need to be confident that the original equipment manufacturer (OEM) understands the market operator’s model requirements and has the skills to comply with them.
Can the machine offer economic benefits?
Two possible revenue streams could potentially flow from installing a synchronous condenser. By sizing the synchronous condenser to provide the reactive power required from a solar farm by the electricity rules, it is possible to operate the solar inverters and the main transformer at a higher power factor. This has the potential to increase the power output and consequently the revenue from the farm by up to 7%. A proponent could also install an oversized synchronous condenser and sell the spare system-strengthening capacity to another renewable farm in the same region. In the future, inertia and system-strength markets may evolve in ways that provide direct revenue streams for the synchronous condenser.
Redundancy considerations: Is one syncon enough?
Most new generators initially opt for a single, larger synchronous condenser to minimise upfront capital expenditure and ongoing operational expenditure. However, this decision inherently introduces a significant operational risk: the potential for severe output constraint if that sole synchronous condenser becomes unavailable. While synchronous condensers are generally highly reliable, mechanical and electrical failures can occur, and the lead times for repairs or replacement components can be substantial, leading to prolonged outages.
For asset owners considering the future divestment of their renewable energy project, this redundancy factor becomes a critical due diligence item for potential purchasers. A single point of failure for system strength support will be scrutinised. A prospective buyer will likely conduct a far more pessimistic assessment of the probability and duration of generation curtailment due to a synchronous condenser being unavailable, compared with the assessment of the original developer. This increased risk perception can directly and negatively impact the valuation and sale price of the entire energy park.
Is there an alternative?
The inverters at the heart of most solar farms and most modern wind turbines are changing. Until approximately 2023, they exclusively used a technology called ‘grid-following inverters’, but a newer ‘grid-forming inverter’ is breaking into the market. These inverters are more expensive at the moment, but that’s changing rapidly. The newer inverters are much less sensitive to system strength and can typically be operated with the base level of system strength that the TNSP is required to provide. Applications are now emerging in which changing the inverter eliminates the need for a synchronous condenser.
Putting it all together
The most cost-effective projects are often those that link multiple technologies – such as a wind farm with modern wind turbines, static VAr compensators and more than one synchronous condenser. These technologies were not designed to work well together, but with carefully coordinated controls they have done so in practice, providing the required system strength, voltage control and inertia for a successful minimum-cost project.
If you would like to find out more about how Entura can help you overcome electrical challenges for your renewable energy projects, please contact David Wilkey or Patrick Pease.
ABOUT THE AUTHOR
David Wilkey is Entura’s Principal Consultant, Secondary Electrical Engineering. He has more than 25 years of consulting experience in electrical engineering across Australia and New Zealand, focusing on the delivery of advisory on secondary systems and power systems engineering. David’s expertise spans all areas of electrical engineering with a particular focus on electrical protection, power system studies and rotating electrical machines.
MORE THOUGHT LEADERSHIP ARTICLES
Renewables in remote mines – a litmus test for the wider renewables transition
Entura’s Greg Koppens has recently returned from the Energy and Mines Summit in Perth, where he led the ‘Think Tank’: a collaborative session addressing the challenge of powering process steam requirements from renewables-generated electricity. Here he shares his observations on the rise of renewables in the mining industry …
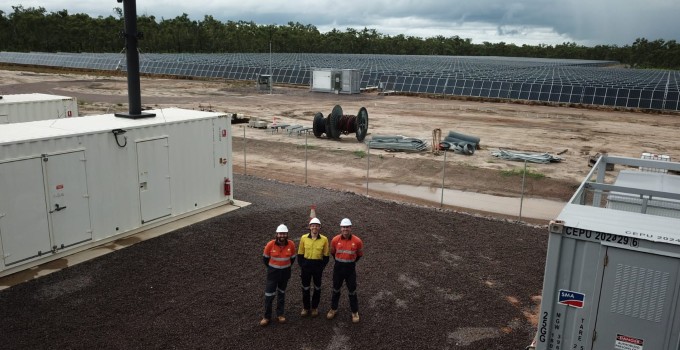
Australia’s mining industry is beginning the peak phase of its energy revolution. However, I find it unfortunate that this exciting fact is invisible to regular people. It is happening in remote areas on mining leases, inaccessible to the public. Each project alone is not sensational enough for media attention, but added together these projects are nothing short of a technology revolution. For remote mining sites to have a solar farm is now standard practice. In many cases this is backed up by battery storage and a handful of mines have onsite wind turbines.
The past: fossil-fuel driven mines
Australia is world-renowned for our mining industries, with mines of virtually every resource throughout our country. Up until about ten years ago, nearly all of Australia’s mines ran completely on diesel or gas. In most cases diesel was trucked in, or gas was brought in via pipeline. Most of these mines have energy expenses in the tens of millions of dollars per year. A small change in the oil price can drastically impact the mine’s bottom line.
If there’s one doubtless fact about mining, it’s that miners are practical people. They are problem solvers, and they know what works. With the boom-and-bust nature of resource markets and shareholder responsibilities, finances must be well managed.
The present: hybrid renewables power generation
At the Energy and Mines Summit, there was no discussion about whether it’s a good idea to consider renewables in the mix of power generation – it was simply a given. This is an industry in ‘early maturity’: it is no longer pioneers running a trial. Several systems are in the order of 100 MW capacity. Renewables are a tested and proven business decision. Everyone has crunched the numbers on their sites and, while each project has unique site-specific requirements, the conclusions are unanimous. The frontier is now getting access to skilled people, there is community engagement for siting of large assets and mutual benefits, and the industry is exploring emerging technologies such as electric fleet.
We now have all the technology needed to harness the power of the wind and the sun in an 80/20 mix with fossil fuels. Or a 50/50 mix when the system has solar power alone. And this is what is being implemented in practice all over Australia. We can do it in a way that achieves targets for price, reliability, service life, operability, maintainability and environmental impact. This greatly reduces the costs and risks of intermediate services such as refining and transportation as well as exposure to the global oil price. Mining companies are taking control of their energy supply by either owning the energy and storage assets or building well-defined low-risk partnerships.
The big project: transitioning the Pilbara to renewables
At the conference there was some focus on the Pilbara, which is a huge and complicated energy consumer, consuming 16 TWh (16 million MWh) of electricity per year, mostly coming from gas.
On the surface, it seems to be very low hanging fruit to quickly construct a few solar and wind assets to shift this picture. However, in the interests of the best long-term outcomes, the area needs planning, consultation and coordination. The Western Australian Government has developed a plan for ensuring that common-use infrastructure is used where possible, rather than risking having multiple redundant assets owned by different corporations. Aboriginal and community participation is recognised as crucial for the appropriate siting of wind, solar and transmission equipment.
The near future: electric fleet
Approximately half of a typical mine’s energy needs can be met by onsite electricity generation. The other half currently requires diesel fuel to run a fleet of light vehicles, monstrous ‘haul’ dump trucks such as the 250 tonne CAT 793, and every piece of mobile machinery in between. These mobile machines are the next target for reducing costs, carbon emissions and labour. Several trial projects are happening. For underground mines, where diesel has previously been used, huge ventilation fans will need far less power when there are no exhaust fumes to expel.
Machine manufacturers are developing a wide array of specialised battery electric products. In some applications, there is battery swap technology, as in modern power tools. In other applications, a fixed battery plugs in to recharge, like in an electric car. There are also trolley systems, akin to a tram or train. The best system for each job depends on the application.
Transitioning to a fully electric fleet will significantly increase a site’s electricity needs, with the biggest chargers running at 6 MW at full power. We are expecting to see sites’ electrical grids upgraded soon to integrate this high-power charging.
What is Entura doing?
At Entura, in addition to electrical generation and distribution design, we have specialised capabilities in control systems and power system studies for mining projects. Our microgrid control system (MCS) uses standard and reliable industrial Allen Bradley hardware to monitor and control the power station assets. We have a field-proven core algorithm for maintaining a priority of reliable power supply including backup/reserve supply, while making the greatest use of wind and solar where available. We’ve proven this process in our existing installations in the field and we lead the industry in methodology, practicality and voltage/frequency management.
We’ve seen the real benefits these systems bring to our clients and communities, both at mining sites and in other remote locations. Entura has a long history of design, formation and operation of microgrids throughout Australia (such as King Island, Flinders Island, Rottnest Island, and at mining sites such as the Agnew gold mine) and in the Pacific region (including the Cook Islands, the Federated States of Micronesia, Tonga, and the Solomon Islands, to name just a few).
Contact us if you’re interested in unlocking the full potential of microgrids for your operation or community, or if you’re interested in ways to increase your use of renewable energy.

[Image immediately above] Entura’s Patrick Pease, Greg Koppens and Mark Richardson at the 2025 Energy and Mines Summit
[Top of article] Greg Koppens (centre) onsite at Jabiru Power Station, Northern Territory
ABOUT THE AUTHOR
Greg Koppens is Entura’s Principal Control Engineer Hybrid Renewable Systems and previously led Entura’s secondary electrical engineering team. Greg’s experience spans power, oil and gas, and mining, including onsite roles. With over two decades of detailed design experience, Greg facilitates collaboration between engineering disciplines and other stakeholders to solve complex problems. He regularly shares his extensive expertise with the mining sector to advance their decarbonisation goals. Find out more about Greg in our podcast series here.
New technologies are important tools, but they need to be used properly
Entura’s Technical Director (Water), Richard Herweynen, recently attended the 2025 ICOLD Congress in Chengdu, China, themed ‘Common Challenges, Shared Future, Better Dams’. Here he shares his observations on the state of play in the international dams industry – and the opportunities emerging with artificial intelligence and automation.
My first ICOLD Congress was in Beijing, China in 2000. I was presenting some finite element analysis work that I had done on Gordon Dam, a 140m-high concrete arch dam in Tasmania. The analysis was being used to help predict and explain some cracks that had formed at the base of the downstream face of the concrete shell, roughly normal to the foundation, during first filling. In the 1980s, an attempt had been made to model the crack using finite element modelling, but with little success due to the coarseness of the mesh. However, by the late 1990s, computing power had increased and finite element programs had improved, providing the capability to construct more detailed finite element models, which were able to predict and explain the cracking that had occurred.
Dr Sergio Giudici, the designer of Gordon Dam, was my mentor on this finite element analysis, and he reinforced these principles:
- It is important to verify the input data to make sure the model represents, as well as possible, the actual dam parameters.
- Results should be validated using alternative techniques to give the engineer confidence in the results that the model is producing (i.e. structural hand calculations still have a place).
- Complexity should be built into these models only gradually, so that the engineer can see the impact of changes and determine whether they are reasonable.
These same principles are true for many complex engineering models and when setting up calculation spreadsheets or similar.
Now, 25 years on, I have had the privilege of attending the 2025 ICOLD Congress in Chengdu, China. At this Congress, there was much talk about the importance of dams in society for water security, the growing role dams and reservoirs play in providing resilience to climate change and the energy transition, the importance of balancing economic benefits and environmental needs, and – in all of this – the importance of ensuring that our dams are safe for communities downstream.
We have discussed many of these themes before – and they remain highly important; however, one thing I took away from ICOLD 2025 in particular was how China is embracing technology and advancing a ‘Smart Dam’ initiative.
New technologies and smarter dams
One could say that our industry has always been building smart dams, but China’s ‘Smart Dam’ concept is about using the full power of current technologies to construct, monitor and operate dams in smarter ways, and to use technologies to predict and adapt to changing conditions.
The CHINCOLD Workshop on Digital and Intelligent Technologies for Dam Construction, Operation and Maintenance, which occurred during ICOLD 2025, gave a glimpse of what may be possible.
Many projects utilise 3-dimensional digital models and building information modelling (BIM). However, the concept of having a digital twin of the dam, replicating every aspect of the physical dam in a digital form, opens the door to many possibilities, especially in light of the advent of artificial intelligence (AI).
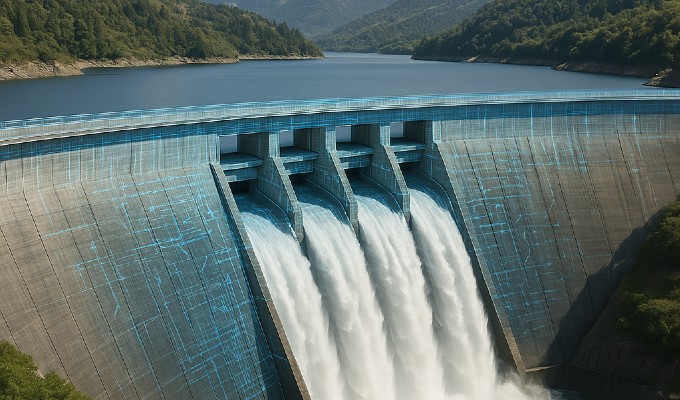
Artificial intelligence and machine learning
Many organisations and nations have been cautious about AI, but China is increasingly adopting it to improve construction practices in dam engineering, improve monitoring and surveillance of dams, and to help adapt to extreme events as they occur.
Machine learning (ML), an element of AI, enables computers to learn from data without being explicitly programmed. ML algorithms analyse data, identify patterns, and make predictions or decisions, improving their performance over time and with more data. There are no doubt many engineering applications where ML could be used to help improve predictive modelling or optimisation, and to make these more efficient. However, the same principles that were important when we were beginning to embrace larger, more refined finite element models with the advent of faster computing remain true here:
- We must verify the input data that machine learning is utilising to ensure we don’t get ‘garbage in equals garbage out’.
- Results need to be validated. AI needs to be trained correctly, and we need experts involved at this stage to ensure that the outputs from AI are correct.
- Complexity, or the full power of technology, should be added incrementally, to provide progressive confidence in the outcomes.
Engineering is the application of science, and therefore it is critical for every engineer to understand the fundamental principles and how to apply them. The complex computer programs used for a lot of engineering modelling can become ‘black boxes’, and practitioners risk diluting or losing their understanding of the fundamental principles behind the models, and hence their ability to validate the results.
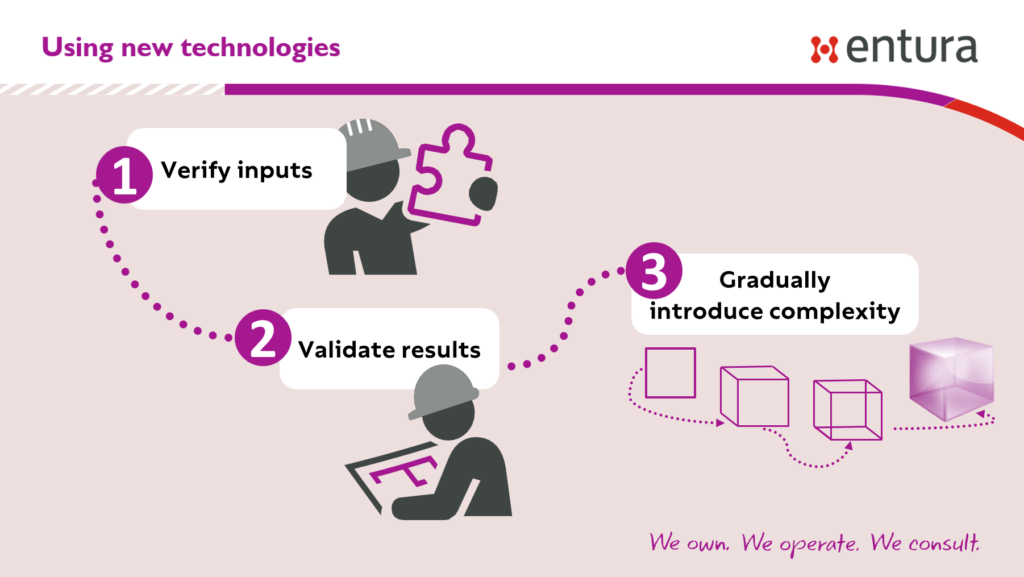
Automation brings a step change in efficiency and accuracy
At the ICOLD Congress in 2000, I co-authored a paper for the international symposium on concrete-faced rockfill dams (CFRD) entitled ‘Hydro Tasmania experience in concrete-faced rockfill dams – past, present and future’. There is no doubt that Hydro Tasmania has a strong history in CFRD, with Cethana Dam playing an important role in the development of the modern, high CFRD.
In 2000, however, the future in CFRD that we envisaged did not include unmanned construction equipment with automatic quality control feedback loops. At the 2025 CHINCOLD Workshop on Digital and Intelligent Technologies for Dam Construction, Operation and Maintenance, a presentation was given by Wang Jiajun from Tianjin University on intelligent unmanned roller systems to compact rockfill dams. Unmanned rolling compaction (URC) systems involve three core technology modules: (1) intelligent perception, (2) autonomous planning and decision making, and (3) intelligent control. These systems use automated driving technology to control the rolling process on earth and rockfill dams, improving productivity and quality. They can accurately control compaction parameters such as passes, speed, vibration and lift thickness. URC systems also enable continuous monitoring and real-time feedback for quality control, reducing human error and improving overall project performance. This automated technology was used on the 295m-high, 1.57km-long Lianghekou hydropower dam in China, with a total fill volume of 43 million m3.
The changing face of dam engineering
With AI and automation, the scope for embracing new technology in dam engineering is growing fast. It is clear that there are significant benefits that could be realised for dam design, construction, operation, dam safety and emergency response – and there’s a role for these advanced technologies at all of the stages of the life cycle of a dam. A degree of caution is appropriate and necessary, but caution should not be a reason to refuse to engage with the new technologies available to our industry.
However, with more sophisticated models – such as digital twins – being created of our dams, it is important to ensure we maintain the guiding engineering principles of verifying input data, validating models for correctness, and building complexity gradually. By doing this, we can provide the necessary assurance and confidence in our increasingly sophisticated and evolving tools.
ABOUT THE AUTHOR
Richard Herweynen is Entura’s Technical Director – Water. He has more than three decades of experience in dam and hydropower engineering, working throughout the Indo-Pacific region on both dam and hydropower projects. His experience covers all aspects including investigations, feasibility studies, detailed design, construction liaison, operation and maintenance and risk assessment for both new and existing projects. Richard has been part of a number of recent expert review panels for major water projects. He participated in the ANCOLD working group for concrete gravity dams and was the Chairman of the ICOLD technical committee on engineering activities in the planning process for water resources projects. Richard has won many engineering excellence and innovation awards (including Engineers Australia’s Professional Engineer of the Year 2012 – Tasmanian Division), and has published more than 30 technical papers on dam engineering.
When the lights go out
Major power outage events, like the one that affected Spain and Portugal this April, can be enormously disruptive and even deadly. Here Entura’s Technical Director Power, Donald Vaughan, considers the complex factors at play and their implications for grids everywhere ...
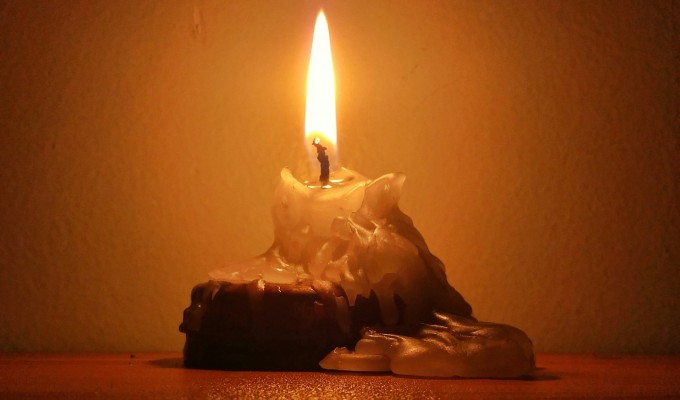
The recent power outage on the Iberian Peninsula provides a serious opportunity for reflection. Many articles have been published that try to explore the seconds and milliseconds after 12:32 PM on 28 April 2025 while only having access to the grainy frequency plots and approximate timelines that have been released (to date). This is not one of those articles. Nor is it an article that will lay blame on a particular technology or energy source. Instead, I will expand on the physics at play in this instance and reflect on whether current network security practices are adequately catering for changes to the power grid.
The physics
The power system is governed by the laws of physics, as is normal in the physical world. Quite a few of these laws tend to gang up on us during a power system event[1].
(i) conservation of energy
(ii) Ohm’s law
(iii) Newton’s laws of motion
and, of course,
(iv) Murphy’s law.
We’ll talk about the first three now and the last one later.
We learn very early that energy can neither be created nor destroyed (law i, above). This is at the heart of a power system event. The power system supplies loads by supporting voltage across the network that supplies millions of parallel loads. Each of these loads converts electrical energy into another form of energy based on the voltage it sees and its internal characteristics. This will continue as long as the voltage profile is maintained (law ii). So, demands take energy out of the power system regardless of what generation events occur.
We know that the main trouble in the recent Iberian event started when a large amount of generation stopped in southern Spain. This led to an imbalance between generation and demand in that region. That imbalance is immediately addressed through the inertial action of synchronous generation across Europe (law iii).
If interconnection were perfect, the burden of this inertial response would be shared perfectly across Europe and we probably wouldn’t be talking about this event quite as much as we are. Yet interconnection is rarely perfect (law ii). The frequency in Spain started to move away from frequency to the east and the AC interconnection to the east opened (which avoided the disturbance that stems from loss of synchronism). This should have been some help to the falling frequency in Spain given the eastward flows at the time. Under-frequency load shedding (UFLS) occurred around this time and should also have helped. It seems that the voltage disturbance that then occurred as a result of all these trips was the last straw.
Network security practices
It would be a gross over-simplification of network security practices to say that the power system should not lose customer load for the loss of one generation or network element (N-1 redundancy). The event on 28 April is way beyond that. Typically, for larger events, the grid should fail safely. We’ll look at that definition of ‘safely’ later. For now though, we can see that the grid did, in fact, try to fail gracefully:
- The AC interconnectors opened to avoid damaging loss of synchronism.
- The under-frequency load shedding operated to try to preserve supply to some customers and keep the grid up, so as to reduce the duration of the interruption.
- Other generating unit controls acted to either increase output or trip to avoid damage.
We see in the Iberian Peninsula outage, as we did in the major South Australian blackout in 2016, lots of independent protection operations slowly but surely weakening the grid to the extent that it is no longer viable. Each of these protection operations undergoes scrutiny after an event of this nature, and will likely lead to some changes in Spain and France as was the case in South Australia.
The 28 April event appears to be quite slow in comparison to some other network blackout events. Even so, the event lasted less than 20 seconds and had 2–3 stages within it. One of the bases of design of the AC network is that it can generally operate with minimal, fast coordination even under large events. Control relies on observation, computation and action. So, to manage an event, a control system must measure what it needs to reliably determine what control actions it must make, and then take those control actions (assuming it can control all the elements it might need to control) in time for them to have an effect. If we think about a need to deftly control the response of individual units (or control systems) in an unusual way in a short period of time, then we can quickly conclude that this may not be possible.
If we can’t manage these events in real time, we have three courses of action:
(i) Physical plant
We could design networks, network supports, and network and generator protection and control systems to be more robust in the face of large power system events, thus decreasing the likelihood of unnecessary cascading protection operation.
This would include better interconnection, more dynamic reactive support (separate from generating units and demand), system-level protection schemes, and a review of generating unit protection settings to ensure generator capability rather than network requirements setting operating limits
(ii) Dispatch rules
We could change dispatch to provide greater margin for real and reactive power control as determined by the security risk and the cost to mitigate it.
We could continue the traditional N-X approach to system supports or we could use a stochastic approach to determining system support requirements (weighting the probability of an event occurring against its impact). Either way, we’d have to pay an ‘insurance’ premium at each dispatch interval to make large-scale system outages less possible.
(iii) Restart planning and capability
We could make recovering from major blackout events easier and faster.
We think about these events in terms of how often they occur (which is what the first two course of action cover) and how long they last. System operators typically have generic plans for system restart that rely on starting synchronous plant and re-energising transmission systems and eventually customer demand. This can be made easier with interconnection. It can also be made easier with good visibility of voltages and voltage profiles across regions (and the tools to control them). Often, for big events like in South Australia in 2016, the network is left somewhat stricken from equipment damage. System restart efforts are often hampered in this scenario because plans need to be improvised to adapt. This depends on the skill, knowledge and experience of the operators. Some jurisdictions have simulated such events as part of training operators.
The fourth law
We know that ‘anything that can go wrong will go wrong’. Seemingly simple things can undermine the best laid plans and the best intentions. We often can’t plan for these things specifically, although HAZOPS, root-cause analyses, scenario simulations and reviews can help us understand where the problems may lie and give us a chance to close loop-holes before they become SNAFUs.
Major power outage events are serious. They often lead to loss of life or injury, and the recent Iberian Peninsula event was no exception. They also always have an economic impact, which is not always fairly distributed. As an industry we need to improve how we manage them. We also need to get better at talking about technical issues in a political environment. If there’s a risk of blackouts, we have a duty to not only mitigate that risk within the current rules but also advocate for rule changes if that mitigation is inadequate. To be most productive, this conversation should happen in a techno-economic environment. The automatic debate after power system events often focuses on the role of renewables, commercial interests and the like, which may sometimes be entertaining but inevitably affects the techno-economic outcomes in a negative way for everyone.
ABOUT THE AUTHOR
Donald Vaughan has over 20 years’ experience providing advice on regulatory and technical requirements for generators, substations and transmission systems. He has worked for all areas of the electrical industry, including generators, equipment suppliers, customers, NSPs and market operators. Donald specialises in the performance of power systems. His experience in generating units, governors and excitation systems provides a helpful perspective on how the physical electrical network behaves.
Image: Basil James on Unsplash
[1] There are more laws, but these are the main and most accessible.
Decommissioning battery energy storage systems: It’s never too early to plan for retirement
All good things come to an end – even big battery energy storage systems (BESS). In Australia, the end of life for BESS may feel very distant, since we’re really only in the infancy of the booming BESS industry; however, the life expectancy of these big batteries is nothing like the design life of other renewable energy and storage technologies. With BESS currently only lasting for around 10 to 15 years of operation, developers and owners of BESS installations need to be thinking and planning now for what decommissioning will involve and what it will cost. In fact, planning for decommissioning is best done right from the start – long before the project is constructed.
Here, one of Entura’s BESS specialists, Dr Rahmat Khezri, answers some burning questions about the end stages of a BESS project.
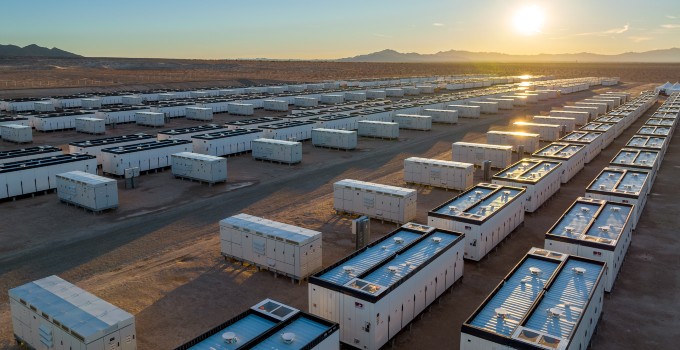
- When does the life of a BESS project come to an end?
The need to decommission a BESS project could arise either from the conclusion of a contract or power purchase agreement – though this is unlikely – or from the expiration of the battery’s operational lifespan. This could be when the battery capacity has degraded to a point where it is no longer financially viable to operate in the market or when the battery’s internal chemistry has reached a point where it is unsafe to continue operating.
For nickel-manganese-cobalt (NMC) batteries, which held a significant share of batteries before lithium-iron-phosphate (LFP) batteries entered the market, this could be after 3,000 to 7,000 cycles at 80% depth of discharge (DoD) or around 10 to 15 years. For LFP batteries, which are gradually dominating the battery market for BESS, it’s around 4,000 to 10,000 cycles or 15 to 20 years. However, several factors can either reduce or extend the battery lifespan. Higher DoD shortens battery life, and frequent high-power cycling (e.g. for frequency control ancillary services, FCAS) can accelerate degradation. Avoiding prolonged high or low state-of-charge management (SoC) reduces degradation. Temperature is also an issue – so proper cooling and heating systems can support greater longevity.
- Is decommissioning the only option?
Full decommissioning of aging BESS assets is not always necessary at battery end of life, as some key components – such as inverters, transformers and balance of plant (PoP) – often retain residual service life. There may be opportunities for repowering or augmentation instead, which will require a much lower level of decommissioning activities. Repowering replaces old batteries with newer or upgraded technology to restore or enhance performance. Augmentation generally aims to increase capacity or power output by expanding the system with additional capacity, for example by adding extra battery racks to an existing setup.
- What does a full BESS decommissioning program involve?
A typical full BESS decommissioning program includes the following activities:
- developing the decommissioning plan including a risk assessment
- de-energising the BESS
- removing power conversion systems (inverter/transformer stations)
- removing integrated battery storage units (site dismantling and packaging may be required)
- shipping the packed battery storage units to recycling facilities
- removing electrical cables and conduits
- removing substation equipment
- shipping the power conversion systems and cables to recyclers of electronic waste
- transporting non-recyclable material removed from the site to disposal facilities
- restoring the site.
- How long could BESS decommissioning take?
Once a BESS project stops operating, the decommissioning process can begin (usually within 12 months) and can take around 6 to 9 months. Of course, this will depend on the scale of the BESS project, which will determine the amount of battery units and electrical infrastructure that will need to be removed from the site. If site restoration is required, this could extend the timeframe.
- What might BESS decommissioning cost?
Decommissioning costs are made up of labour, equipment, transport, materials, and recycling or disposal. These costs can be categorised across the stages of the project: removing the BESS facilities, restoring the site, packaging and transport, and the cost of recycling or disposal. If it is possible to achieve some value from salvage, this can be offset against the decommissioning costs. Currently the total recycling fee for high-powered batteries is around $10–15 per kg. Assuming approximately 6 kg for 1 kWh, the recycling cost would be $60–90 per kWh.
- Talking about recycling, what are the options for decommissioning BESS sustainably?
In Australia, we’re still in the early days of developing a lithium battery recycling industry – but we are seeing increasing recognition by owners, developers, regulators and the community of the need for the renewable energy industry to strengthen the circular economy and minimise landfill. Battery modules are recyclable – but salvage and reuse are likely to remain very dynamic and the future market for used lithium-ion modules remains uncertain. We recommend that every BESS developer/owner should aim to maximise recycling and develop as sustainable a waste management plan as possible. It is worth noting that recycling and reuse of inverters, transformers and BoP components are well established and available.
- What regulatory requirements are there in Australia for BESS decommissioning, and how do you envisage this changing?
In Australia, BESS projects must comply with relevant environmental regulations, which vary by state but generally align with the environmental protection guidelines set by each state’s Environment Protection Authority (EPA). At the federal level, the Product Stewardship Act 2011 promotes the responsible management of products at the end of their life cycle, including batteries. Decommissioned components from BESS projects, particularly lithium-ion batteries, are typically classified as prescribed industrial waste (PIW), requiring handling by licensed transporters and disposal at approved facilities.
At this stage the permitting process to build a BESS facility does not require a formal plan for decommissioning and disposal – but it is probably only a matter of time until we see more stringent requirements as part of the development application process. Despite a detailed plan not yet being required, it is definitely worthwhile doing, not least because the costs of decommissioning should be factored into the business case from the outset.
- What lessons have been learned from international examples of BESS decommissioning?
There haven’t been many examples of BESS decommissioning in our region yet, but the example of decommissioning the Tehachapi Energy Storage Project (TSP) project in South California in 2022 is an instructive real-life case study. This 8 MW / 32 MWh lithium-ion battery project was one of world’s first and largest BESS when it was commissioned in 2014. It had a footprint of 585 m2, with 604 battery racks and two 40-foot PCS containers. The decommissioning was completed in just over 4 months from the generation of the purchase order to the finish.
A key takeaway from this case study is the significant impact that logistical and site-specific constraints can have on project outcomes. Although the PCS containers were initially expected to be removed within a single day, unforeseen space limitations and permitting restrictions ruled out the use of cranes. As a result, the containers had to be dismantled and cut into sections on-site. This increased the schedule by 17% and the cost by 20%. The lesson here is clear: success lies in the details, particularly when it comes to transport and access logistics. Thorough, site-specific planning is essential to avoid unexpected delays and budget overruns.
- What should Australian BESS developers and owners be doing now about decommissioning?
Ideally, every player in the BESS industry in Australia should be thinking ahead, however far off BESS decommissioning, repowering or augmentation may seem right now. It is never too early to start investigating the potential options, costs, timing, emissions, challenges and solutions – and developing a plan that can continue to evolve as the industry matures. A robust decommissioning plan will also be a valuable input into the technical due diligence process for sale/purchase. Ultimately, solid, early planning is the key to minimising risk and maximising value – and achieving a more efficient, more cost-effective and more sustainable outcome for any BESS project.
At Entura, we’ve been involved with BESS since the very start of the sector in Australia, and we’re always learning from our experiences here and around the world. We’re actively developing our analyses of decommissioning costs, transport, timing and circularity opportunities so that we can support your BESS project holistically, from cradle to grave.
Regardless of the stage of your BESS project, Entura can help. Contact Patrick Pease to find out how.
About the author
Senior Renewable Energy and BESS Engineer Dr Rahmat Khezri has vast professional and technical experience with batteries. He has worked in the renewable energy and battery industry in project delivery from BESS design, business case and feasibility analysis to operation and construction. Rahmat has managed several utility-scale BESS projects during his time with Entura, overseeing successful delivery while ensuring compliance with industry standards, optimising performance, and managing key stakeholder relationships. Before joining Entura, he worked on projects supported by Sustainability Victoria for technical design and business case development of ‘second-life BESS’ using retired batteries of electric vehicles. In 2023 and 2024, he was recognised by Stanford University as being in the top 2% of scientists worldwide for two consecutive years.
Planning for the future – the challenges of dam inspection and maintenance
No dam is ‘maintenance free’. Without appropriate maintenance and refurbishment at the right times, a dam may not be able to fulfil its function safely for the full length of its design life (which could be more than a century).
This presents many challenges for asset owners. To keep the dam operating as the designer intended – and get the most out of the original investment over the long term – owners will need to develop and implement a suitable operations and maintenance manual aligned with the asset management plan and reflecting a ‘whole of life’ strategy. These plans will need to consider the unique characteristics of each dam and cover all the relevant issues. And there are many!
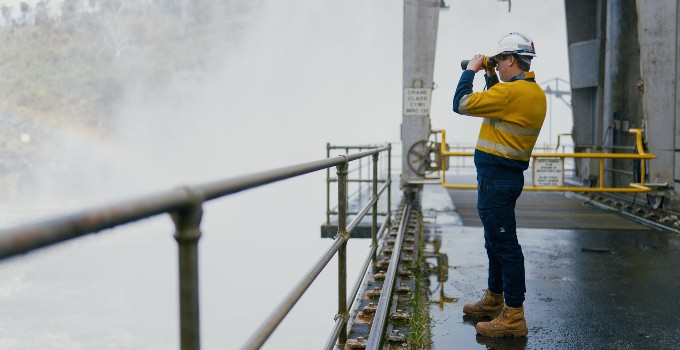
Dams consist of a number of different elements. There are the main civil engineering components including the wall that holds back the water and the spillway – but there could also be mechanical elements (pipework, valves and gates) and electrical elements (power supply to lights, valves, gate motors and control systems). Each of these elements will have its own operational and maintenance requirements and different lifecycle duration. Ideally, all this detail needs to be captured in the operation and maintenance manual (as recommended by ANCOLD guidelines) and in an asset management plan.
Civil components
The civil components of dams have the longest life span, typically more than 100 years if well constructed and maintained. Common maintenance items that need to be regularly addressed include:
- Vegetation management
Trees and bushes will readily grow in earthfill and rockfill embankments. Regular control (e.g. annually) is necessary to ensure that roots don’t grow through the fill and initiate leaks through the embankment. Mowing the grass on the downstream face of the earthfill embankment and downstream contact is necessary so that the condition of the face can be observed. Even concrete gravity and concrete arch dams will require vegetation control along the downstream face contact with the foundation so that the dam can be easily viewed in routine inspections.
- Surface water drainage
Dam construction typically affects natural drainage lines, which is why surface water drains are a common feature around and on dams – such as along the groins (where the dam wall intersects with natural ground), along berms in embankment dams, along benches, at the top of cuttings, and along access tracks. Drains will need regular inspection for both erosion and blockage due to sediment or vegetation.
- Foundation drain cleaning
Concrete gravity dams and concrete arch dams typically have drains drilled into the rock foundations to relieve uplift pressures and help maintain stability of the wall. Over time, silt or iron-rich slime can build up as a byproduct of bacterial growth in the drains, reducing effectiveness. These drains typically require 5-yearly high-pressure flushing. Cleaning will also be needed for drains underneath spillways founded on rock and cut slopes in rock.
- Protection of the dam safety monitoring system
Protecting the dam safety monitoring system requires a range of regular activities. These include cleaning and clearing vee-notch seepage monitoring weirs, checking survey monitoring pillars and targets, and checking the calibration of level monitoring and indication devices, such as reservoir-level sensors, piezometers, tiltmeters and inclinometers. Regular functional testing will also need to be carried out on the alarming and tripping devices that form the primary protection elements of the dam, including spillway gates and scour valves.
- Clearing of trash racks
Outlet works usually have trash racks to stop debris entering the pipework and causing blockages. It’s important to check that the build-up of debris is tolerable and that any hydraulic losses won’t affect operations. Assessing and removing the debris isn’t easy, as the trash racks are often accessible only by remotely operated vehicles (ROVs) or by divers. Before the inspection, the outlet will typically need to be closed and isolated.
Inspection-driven longer term maintenance will also be required for particular elements of the dam, ideally addressing repair items promptly to minimise damage and the cost of future repairs if left untreated. For example, concrete repairs may be needed to address erosion in stilling basins and spillway chutes, or spalling of concrete due to reinforcement corrosion or freeze/thaw damage.
While regular inspections should be undertaken to detect slow deterioration, special inspections following major events – such as floods or earthquakes – should also be part of the operations and maintenance plan. Given that the key areas for inspection are often difficult to access safely, use of UAVs (e.g. to inspect a spillway crest and chute) or ROVs (e.g. to undertake underwater inspections or scanning of stilling basins, plunge pools or riverbed scour) should be considered.
When special inspections identify the need for repairs, the time is right to consider whether the dam’s design or surveillance could be improved to increase resilience for a similar event in future. For example, a higher strength concrete overlay may treat erosion of a spillway chute and increase its resistance to future erosion.
Mechanical components
Mechanical items such as steel or cast-iron pipework can also often last up to 100 years if adequately protected from corrosion. Concrete and cement mortar are very effective for this purpose as the alkaline environment provided by the cement paste provides a very low corrosion environment. Key to the effectiveness of this protection is ensuring that the cement remains in intimate contact with the steel or iron. This will require regular inspections and timely repairs. Where concrete protection is not practical, paint systems can be very effective for up to about 20 years. A suitable inspection regime will be needed so that any areas where the paint has deteriorated can be detected and patched.
Mechanical items such as valves and gates typically have an effective life of around 50 years; however, they need to be exercised regularly to keep them able to work on demand. This is not an issue of the parts wearing out from use; rather, it’s the risk of them seizing due to lack of use. Regular lubrication of bearings, gearboxes and trunnions needs to be included as part of the maintenance of these items. This is particularly important in scour valves and spillway gates that may have a very low frequency of use during normal operations but are there for use in emergencies. The wire ropes commonly used to hoist spillway gates open will need even more frequent replacement, at approximately every 20 years.
Electrical components
Electric motors are commonly used to drive the winches hoisting spillway gates or driving the shafts to open valves. Associated with the motors will be switchboards and power supply systems, typically including grid power supply and backup diesel generators. The typical life of these components is around 25 years. As with the mechanical components, lack of operation can lead to premature failure, so a regular regime of exercise is necessary to ensure maximum reliability and life.
The programable logic controllers (PLC) that are used to automate operations, allow remote operations and generate alarms will have a typical life of only 10–12 years due to changes in programming languages and rapid evolution of the hardware.
Getting the most out of life
As we’ve seen, regular maintenance is fundamental for keeping all the components of a dam operating as intended and maximising their lifespan – whether that’s 10 years or 100. This maintenance, including the exercising of the mechanical and electrical components, needs to be clearly documented in the operations and maintenance manual and recorded in an asset management system. The asset management plan must allow for regular maintenance and also budget appropriately for replacement or refurbishment when any component of the dam is due for retirement.
At Entura, we believe in getting the most out of every piece of infrastructure because that’s good for our clients, communities and the planet. With a solid regime of inspection and maintenance, all the parts of your dam will be on the strongest path to a long, reliable and sustainable life.
If you’d like to talk with us about inspecting and maintaining your dam/s, contact Phil Ellerton, Paul Southcott, or Richard Herweynen.
About the author
Paul Southcott is Entura’s Senior Principal – Dams and Headworks. Paul has an outstanding depth of knowledge and skill developed over more than 3 decades in the fields of civil and dam engineering. He is a highly respected dams specialist and was recognised as Tasmania’s Professional Engineer of the Year in Engineers Australia’s 2021 Engineering Excellence Awards. Paul has contributed to many major dam and hydropower projects in Australia and abroad, including Tasmania’s ‘Battery of the Nation’, the Tarraleah hydropower scheme, Snowy Hydro, and numerous programs of work for water utilities including SeqWater, Sun Water and SAWater. His expertise is a crucial part of Entura’s ongoing support for upgrade and safety works for Hydro Tasmania’s and TasWater’s extensive dams portfolios. Paul is passionate about furthering the engineering profession through knowledge sharing, and has supported many young and emerging engineers through training and mentoring.
What have we learnt about renewable microgrids and remote area power systems?
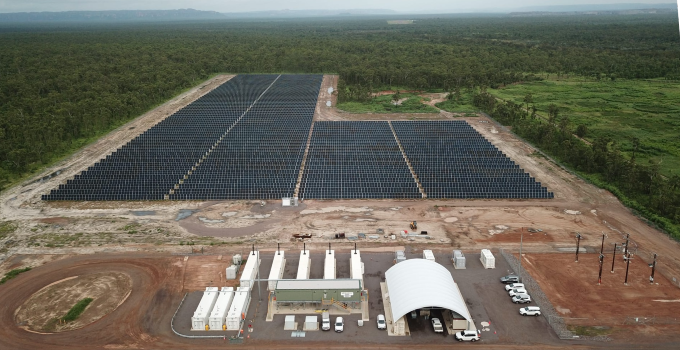
With the evolution of modern inverter and renewable energy technologies, it’s become possible to build microgrids with very high renewable penetration. These renewable solutions are revolutionising electricity sustainability, reliability and access in many far-flung locations – such as Pacific islands, remote locations around Australia, and on mining sites.
High renewable penetration allows operators of off-grid microgrids to extract maximum value from their installed solar, wind or other renewable generation while minimising the use of fossil fuels, such as diesel. It’s a win-win for the financial bottom line and emissions-reduction goals. If the microgrid connects with a broader power system, the benefits of reducing reliance on externally sourced energy are significant too.
Establishing a relatively simple microgrid with modest fuel-saving targets doesn’t have to be particularly complex. It’s within the reach of current technology and practice to be able to optimise microgrids to all but eliminate the use of fossil fuel (with the related advantages of eliminating fuel handling, shipping, etc.). However, careful thought must be given to the distinct nature of the microgrid: its customers, energy sources and storage options.
To make a microgrid successful, some technical challenges will need to be managed. Resolving these challenges in a cost-effective way becomes more difficult as the renewable energy balance approaches 100% – but they’re not insurmountable. Let’s explore.
Challenge 1: Ensuring quality of supply and an acceptable customer experience
The small size of microgrids and the fact that they are usually dedicated to a single ‘customer’ makes engineering a microgrid a sensitive task. While larger grids can operate with tight voltage and frequency tolerances and multiple levels of redundancy, microgrids often cannot. This inevitably means negotiating acceptable system standards for islanded operation that are within the tolerance of customers’ equipment and expectations. Microgrids powered by fossil fuels typically have more difficulty maintaining tight frequency and voltage tolerances than renewables-based microgrids.
Understanding customer and stakeholder expectations relating to reliability and robustness (energy availability and the ability to ride-through faults) is key to the establishment of a successful microgrid. Where the microgrid exists with no possibility of interconnection to another power network (i.e. in an ‘island’), there is more flexibility and less operational complexity. Discerning acceptable standards and practices is still not easy but it can be a more productive discussion than when the microgrid must comply with less tailored standards due to interconnection.
When the microgrid is interconnected, many of the technical requirements for the microgrid will be specified and/or mandated by the network service provider, electricity code requirements, and some operational requirements for electrical safety. If additional communication and inter-tripping with network equipment remote to the microgrid are required, these can add further complexity.
Challenge 2: Managing different modes of operation requiring different controls
In the previous section, we discussed how complicated it is to determine system standards. A great deal of care is also needed when contemplating which standards and controls are most appropriate to the microgrid’s specific characteristics. This is where cookie-cutter solutions could under-deliver and a more insightful approach is required.
A microgrid must manage the voltage, frequency and quality of supply while it is islanded as well as during periods of interconnection. Islands can remain satisfactory for longer if there are energy sources, storage and load controls within the island. Each of these elements comes at a cost and, depending on the frequency and duration of islanded operation, must have a value outside of the islanded scenario.
Our experience with microgrids is that semi-autonomous operation of each of the power sources using standard power system control approaches (solar, BESS and other power sources on voltage and frequency droop control) leads to the simplest and most secure response to transients (load or generation trips, network or network faults). Slower controls can be put in place to balance generation and rates of battery charge or discharge. If the battery power rating is large enough relative to the largest disturbance, it can manage most frequency disturbances within acceptable limits. If the battery energy capacity is large enough, it can always maintain a state of charge that allows fast reaction to variations in customer demand or VRE. Alternatively, auxiliary plant such as switched resistors, synchronous condensers and customer-level load control can be used to minimise battery power, storage and other energy inputs.
Operating microgrids in different modes requires careful engineering of the controls and equipment. The solutions and approaches described above have proven successful across multiple projects, but the key is to always be open to new solutions as new problems arise or new technologies emerge.
Challenge 3: Understanding the marginal value of resistors, synchronous condensers and/or demand management
Auxiliary equipment can help to extend the range and effectiveness of a microgrid to rely solely on renewable energy. The challenge is to understand the actual value of extension in this context. Where it has a direct bearing on fossil fuel use, the benefits are clear. Where it might cause an incremental improvement in the robustness of the islanded operation only, it’s important to consider whether any operational benefits or security benefits gained from the additional capital investment are valuable enough to justify the cost.
If the robustness of islanded operation is to be increased by managing customer demand, customer storage and/or embedded generation (e.g. rooftop solar), the value of the extended island longevity should be weighed against the perceived cost (direct or indirect) to the customer. This requires careful consideration of the diversity within the community, their openness to energy management, and the relationship between true costs and benefits.
Microgrids that maximise local use of renewable resources represent a relatively cost-effective option for lowering carbon emissions and/or reducing energy costs. Isolated communities, remote industrial sites, unreliably connected rural communities and others could benefit greatly from considering microgrid opportunities.
Entura has a long history of design, formation and operation of microgrids throughout Australia (such as King Island, Flinders Island, Rottnest Island, and at mining sites such as the Agnew gold mine) and in the Pacific region (including the Cook Islands, the Federated States of Micronesia, Tonga, and the Solomon Islands, to name just a few). We’ve seen the real benefits these systems bring to our clients and communities.
Contact us if you’re interested in unlocking the full potential of microgrids for your operation or community, or if you’re interested in ways to increase your use of renewable energy.
ABOUT THE AUTHORS
Donald Vaughan has over 20 years’ experience providing advice on regulatory and technical requirements for generators, substations and transmission systems. He has worked for all areas of the electrical industry, including generators, equipment suppliers, customers, NSPs and market operators. Donald specialises in the performance of power systems. His experience in generating units, governors and excitation systems provides a helpful perspective on how the physical electrical network behaves.
Greg Koppens is Entura’s Principal Control Engineer Hybrid Renewable Systems and has led Entura’s secondary electrical engineering team. Greg’s experience spans power, oil and gas, and mining, including onsite roles. With over a decade of detailed design experience, Greg facilitates collaboration between engineering disciplines and other stakeholders to solve complex problems. He regularly shares his extensive expertise with the mining sector to advance their decarbonisation goals. Find out more about Greg in our podcast series here.
We built this synchronicity … but what now?
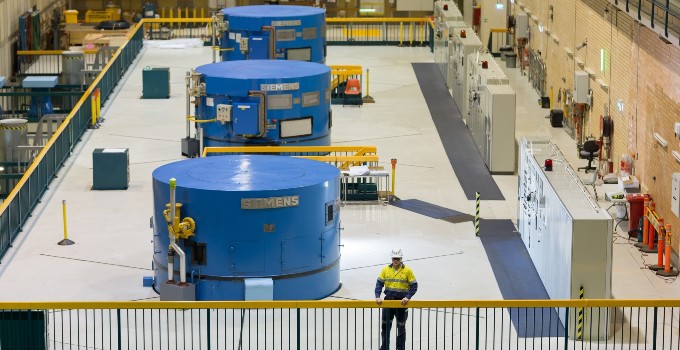
The alternating current (AC) transmission age started in 1891 through collaboration and perseverance. This transmission method has transformed the world, led us to the brink (or over the brink) of a climate disaster, and provides the backbone for a future founded on abundant renewable resources (in Australia, at least). Collaboration and perseverance are now required to ensure the continued utility of the grid.
Synchronous machines have always been the driving force in the grid. These elegantly simple electrical machines sit in powerhouses around the globe using their century-old technology (nearly 150 years, in fact) to convert mechanical energy into electrical energy to power the computer that I’m using to type this.
There’s a romance to these machines. It’s more than nostalgia. They spin, as the name suggests, in synchronism. If one of them falters, all the rest pick up the slack. The only connection they need is the power lines. This robustness is central to the way our electricity grids have operated for over 130 years – but the influence of synchronous machines is slowly being eroded.
The most obvious erosion of the influence of synchronous machines is their displacement by inverter-based renewable (IBR) technologies as solar, wind and battery energy storage (BESS) installations proliferate. A less obvious erosion of their influence is the diminishing understanding and appreciation of synchronous technology within the industry. This lack of understanding by engineers, planners and regulators of the fundamental building blocks of the electricity grid is starting to show.
This might sound like the curmudgeonly ranting of yesterday’s engineer as technology passes them by. Maybe it is … but, rather than dwell on negatives, let’s look at what synchronous machines bring to the power system.
- System strength
The fundamental difference between synchronous machines and IBR is thermal inertia. Typical synchronous machine design can sustain high levels of over-current for a relatively long time (seconds) compared to IBR units (milliseconds). This difference allows synchronous machines to provide a strong ‘natural’ response to voltage variations in the power system without threat of overload and damage. Transmission protection systems – and therefore grid security and safety – rely on this characteristic.
There are alternatives. Overload capacity can be built into inverters, but this is expensive. Dedicated inverter-based devices such as static synchronous compensators (STATCOMs) can be used to provide fault response.
- Inertia
Synchronous machines spin. Their spinning bits (rotors) have mass, so they have mechanical inertia. This mechanical inertia doesn’t require a control system to provide an inertial response. The inertial response from a synchronous machine is a known, predictable quantity, regardless of voltage.
IBRs can provide synthetic inertia and, when voltage is healthy, can out-perform synchronous units. When voltage is not nominal, the same current limitations that affect the IBRs’ ability to deliver fault level can also restrict the effectiveness of synthetic inertia delivery.
- Robustness
The previous two characteristics – system strength and inertia – show the support that synchronous machines can provide to the power system during disturbances. The synchronous machine can deliver these supports across a wide range of power system disturbances to voltage and frequency.
IBRs typically rely on fast controls to manage their response to system disturbances. Under some extreme conditions these controls may not be fast enough or well enough tuned to manage. While tuning is important to synchronous machine performance, often it has a second-order effect or adds robustness over and above the natural response.
Displaced but not superseded
Understanding the inherent dynamics of synchronous machines gives power system engineers a better appreciation of these machines’ contribution to power system stability. Regulators should be mindful of the reduced risk (and mostly advantages) to system security that synchronous machines offer relative to IBRs. This is despite the uncontrollable nature of synchronous machines. That is, physics dictates the stabilising effects from synchronous machines whereas control algorithms determine whether an IBR can stabilise or destabilise. Controller model accuracy is therefore more important for IBRs than it is for synchronous machines where transient stability or electro-mechanical transient time frames are considered.
Better understanding of synchronous machines should lead to more appropriate rules relating to dynamic response to system events. Overly specific requirements for fault ride-through, power recovery post-fault, and maintenance of real and reactive power during voltage disturbances may all lead to needless protracted negotiations over access standards. This slows down the progress of the energy transition, frustrates otherwise helpful development, and diverts resources towards trivial considerations rather than focusing on issues of greater importance.
Synchronous machines will play a role in the energy grid of the future. Our industry needs to maintain expertise and regulatory frameworks that allow this technology to continue providing the grid with vital stabilisation and robustness.
ABOUT THE AUTHOR
Donald has over 20 years’ experience providing advice on regulatory and technical requirements for generators, substations and transmission systems. He has worked for all areas of the electrical industry, including generators, equipment suppliers, customers, NSPs and market operators. Donald specialises in the performance of power systems. His experience in generating units, governors and excitation systems provides a helpful perspective on how the physical electrical network behaves.
Getting the answers you need: Technical due diligence for vendors, buyers, lenders or insurers of renewable energy projects
Technical due diligence (TDD) for a renewable energy project evaluates the risks and opportunities associated with the project to establish its technical and financial viability, compliance with regulations, and other factors influencing its value. TDD is fundamentally a well-understood risk assessment process, with practitioners typically having templates they can tailor to specific projects and client needs. However, different parties will have different objectives, different scope for TDD to cover, and different risk appetites.
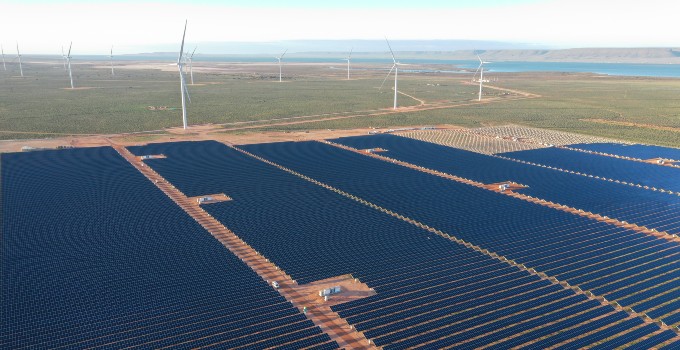
Objectives
Vendor perspective: Do we have our house in order?
An owner (or vendor) is most likely to procure TDD to show the market and prospective buyers their project or portfolio of assets for sale. Engaging an ‘independent’ party to prepare a TDD report serves several purposes: it can facilitate a quicker sale process, enable the owner to anticipate a buyer’s questions, and allow the owner to take pre-emptive actions to mitigate perceived risks. This can give the owner greater control over the sale process or how the project is later structured. For example, in Australia, there is a trend of wind turbine suppliers (original equipment manufacturers, OEMs) getting involved early and developing the project around their specific wind turbine model, then selling the project while maintaining a strong interest as the OEM.
Buyer perspective: Is this project worth our investment?
A buyer conducts TDD to evaluate whether the project aligns with their investment goals, operational capabilities, and risk tolerance. They are interested in understanding the technical feasibility, potential challenges, and opportunities associated with the project. There is often a need for technical inputs to feed into a financial business case, such as CAPEX and OPEX estimates and estimates of energy yield.
Lender perspective: Will we get our money back?
Lenders, such as banks or funding agencies (e.g. Clean Energy Corporation, ARENA, World Bank, Asian Development Bank), conduct TDD to assess the project’s ‘bankability’. This involves evaluating whether the developer can fund the project and if the project can generate sufficient returns to repay loans. Lenders focus on mitigating financial risks and ensuring compliance with lending criteria and industry standards.
Insurer perspective: Is this project insurable, and at what cost?
A wide range of insurances may be in place during the construction and operation of a renewable energy project. Insurers will evaluate project risks and feasibility to determine insurability, the cost to insure, and how to manage potential claims effectively.
Scope
Vendor perspective: Help us prove to buyers that we’re transparent
A prudent vendor will try to anticipate everything buyers might want to know and present the project in the best possible light, ideally addressing information gaps and mitigating risks. The vendor will rely on the consultant’s independence for the TDD report to have value for potential buyers.
Buyer perspective: Tell us the risks – and if the project can be improved
A buyer may undertake TDD at any stage of the project life cycle, from conception to decommissioning, requiring a tailored scope of work. The buyer will focus on technical aspects impacting ownership and operational responsibilities, such as technology selection, construction feasibility, resource assessment, and operational performance expectations. Existing assets may also influence their priorities during TDD.
For example, a buyer who already operates a portfolio of wind farms will be much more comfortable with many of the typical risks of wind development in comparison to a buyer for whom the project is a first of its kind.
Owners will often employ a consulting business to undertake TDD alongside environmental, social and governance (ESG) due diligence, with legal and financial due diligence conducted by other specialist parties.
A good TDD for an owner will focus not only on risks, but also on opportunities for improving the project.
Lender perspective: Tell us everything!
Lenders sometimes directly engage a consultant for TDD; however, often the owner will manage the engagement of a ‘lender’s’ or ‘independent’ engineer for TDD, with the resulting TDD report provided to a bank or consortium of banks for their evaluation and questioning.
Lender’s TDD engagements typically have a broad scope, encompassing not only technical aspects but also financial, legal and regulatory considerations. They assess the project’s financial model, revenue projections, contractual agreements, insurance, permitting, and compliance with regulatory requirements. Lenders are interested in the capability and experience of key contractors, the robustness of contractual arrangements, and will look to TDD consultants for assurances that project schedules are achievable.
Lenders will have a particular interest in things like budget contingencies, and what contractual mechanisms offer assurances such as warranties and liquidated damages.
In practice, the TDD scope for a ‘shovel-ready’ project may be similar for a buyer and for a lender considering investment.
Insurer perspective: Is the technology mature, and what’s this we’ve heard about a flood zone?
Insurers assess risks, including vulnerabilities, operational disruptions, and compliance with industry standards. They are particularly interested in technology maturity and environmental risks that may lead to future insurance claims. For example, rapidly released new wind turbine models may increase the risk of failures, making insurers keenly interested in operational hours as a measure of a model’s proven reliability.
TDD is a core activity for insurance underwriters (those who evaluate and analyse the risk) and is not typically outsourced to consultants. But consultants can learn from the insurance industry, which deals in risk assessment every day.
Risk appetite
Vendor perspective: Help us show it’s a safe bet
Naturally, vendors will typically prefer to present risks as identified and under control. However, it is in their interest to present the project honestly. After all, many transactions have the vendor retaining a stake in the project.
Buyer perspective: Help us find a project with low risk and good returns
The buyer may be evaluating technical risks during project development, construction or long-term operation depending on the project status. In practice, the earlier in the project’s life cycle, the greater the risk, and, in theory, the greater potential financial return.
For example, a project claiming to be ‘shovel-ready’ should have all major planning permits in place, a confirmed grid connection, and technical studies completed (such as geotechnical investigations). The TDD assessment will review documentation to identify specific risks that might eventuate during construction and operation.
On the other hand, for a project in early development, the risks may be of a more generic nature and the buyer may need to accept that there are some unknowns. This is essentially greater risk but there is potential for greater rewards in the long run.
Lender perspective: We’re taking a lot of risk here, so has everyone done their homework?
A typical funding model is where a bank or syndicate of banks provides a loan to a project owner that is subsequently paid back via the revenue earned by the project. The loan is secured against the assets of the project, and the banks want to ensure they will be repaid. Lenders take on substantial risk; hence, during TDD they expect to see that projects are well-conceived and executed, and they will adopt relatively conservative views on issues such as expected energy yield.
Insurer perspective: What’s the right level/cost of cover?
Insurers have sophisticated risk modelling techniques and real-world experience of what is going wrong on projects and what it’s costing. Insurance is a global industry, and what happens overseas impacts the TDD that insurers do for Australian projects.
Decisions made by project owners can have a substantial impact on the cost of insurance, and in fact whether insurance is even obtainable. For example, if an owner selects a relatively new or untested wind turbine model, the cost of insurance may negate any intended savings.
In summary
While vendors, buyers, lenders and insurers conduct TDD to assess the feasibility and risks of a renewable energy project, their perspectives, objectives, scopes and decision-making criteria differ based on their roles and interests in the project. As technical consultants who conduct TDD, it’s our responsibility to understand these differences and tailor our TDD approach accordingly.
If you’d like to talk with our specialists about technical due diligence for a renewable energy project, contact Patrick Pease, Bunfu Yu or Shekhar Prince.
About the authors
Andrew Wright is Entura’s Senior Principal, Renewables and Energy Storage. He has more than 20 years of experience in the renewable energy sector spanning resource assessment, site identification, equipment selection (wind and solar), development of technical documentation and contractual agreements, operational assessments and owner’s/lender’s engineering services. Andrew has worked closely with Entura’s key clients and wind farm operators on operational projects, including analysing wind turbine performance data to identify reasons for wind farm underperformance and for estimates of long-term energy output. He has an in-depth understanding of the energy industry in Australia, while his international consulting experience includes New Zealand, China, India, Bhutan, Sri Lanka, the Philippines and Micronesia.
Brendon Bateman is a senior renewable energy engineer with more than 20 years of experience on renewable energy projects in Australia, New Zealand, Pacific islands, Philippines, China, India, Sri Lanka, North Korea and South Africa. Brendon is recognised as a technical expert for feasibility or due diligence of renewable energy projects with involvement in the assessment of over 10,000 MW of greenfield and operational projects, identifying key risks for developers, banks, equity funds and aid agencies looking to develop or invest in renewable energy projects. Brendon is highly experienced in the areas of resource assessment, energy estimates and their associated uncertainty, operational performance assessments, wind turbine due diligence and O&M practices.
Powering a greener mining future with hybrid renewables
This article reflects on a panel discussion chaired by Ray Massie at the Energy and Mines Australia Summit 2023, which you can read more about here.
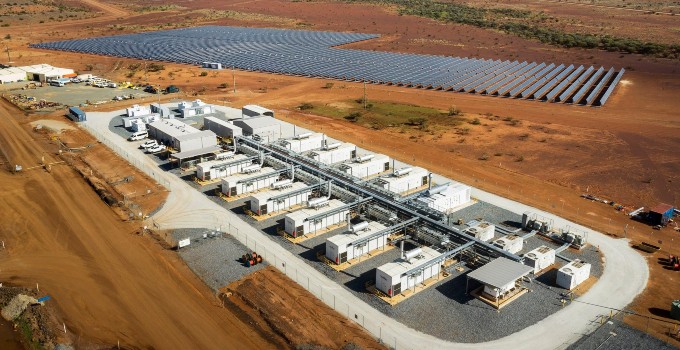
The discussion about powering mines with renewable energy has moved a long way in a short time. As the imperative to go green has escalated, the mining sector has grown hungrier for viable, rapid and cost-effective strategies to decarbonise, build greater social licence and tap into the competitive market for products with a lower carbon footprint. Integrating cheap, abundant renewable energy into mining operations is the natural solution.
These are exciting times as the sector moves far beyond the ‘why’, ‘whether’ and ‘when’ of renewables – and digs much, much deeper into the nuances of ‘how’.
Early forays into small hybrid off-grid renewable energy systems have demonstrated and built confidence in the technology – so there is no longer any question in the mining industry of whether off-grid hybrid renewable systems will work. Off-grid hybrid projects aren’t small test beds anymore. They’re ground-breaking, large-scale, cutting-edge renewable power systems of the future, able to be deployed on a fully commercial basis with clearly understood risks and operational adjustments. In many ways, the mining sector is out ahead of the pack, and the deployment of renewables on off-grid mine sites is offering lessons for the wider power sector and the future of the grid.
With many of the early technical risks resolved, the driving focus now is how to take full advantage of what a hybrid system can offer. How can the system be optimised to maximise its benefits? What’s the required level of reliability? How much storage is enough – and in what form?
Of course, every mine site is different, so there are no one-size-fits-all answers. And today’s answer may not be the right fit for tomorrow, given the rapid and continuous transformation of the energy landscape – in terms of technology advances, policy shifts, price volatility and global trends. It’s a dynamic space.
Integrated control and storage change the game
Traditionally, the relationship between mining operations and power supply has been a relatively simple transaction requiring a given amount of power with a set level of reliability and availability. The modelling of the power system was based on simple load metrics and power quality dictated by the capabilities of thermal generation plant. This equated to a very simple, flat cost of energy with any variance at the macro scale driven by changes in the price of fuel.
As we all know, when we switch over to multiple intermittent and variable generators, things become more complex. One of the keys to unlocking the benefits of a hybrid renewable system is the integrated control approach. With the correct control philosophy in place, you have many more ‘levers’ that can bring each element into play for a given operational mode or system event. This enables achievement of the levels of power quality and reliability that are needed, rather than being limited to the levels that traditional thermal plant could supply.
With this sophistication of control, we can start to think differently about reliability across the whole mining operation. Does the mining plant process or works need the same reliability or availability across everything all the time? Perhaps, for example, power supply for pumping may not require as high a level of reliability as other more critical areas of the plant. A clear understanding of the true reliability needs will help derive the optimal design at minimal cost.
When storage comes into the mix, we can also start to think differently about how to best match energy supply, timing of energy-intensive activity, and storage of excess energy to get maximum value from the renewable resource and minimise both the cost of energy across the operation overall and the cost per tonne of the mine’s output. The economics of long-duration storage are improving all the time.
New horizons for energy storage
Although the technology and the sector have travelled a long way already, there are still issues to finesse. One area of uncertainty is the optimal and most cost-effective storage technology and duration.
Going back a decade, the economic storage duration was 10 to 20 minutes, using the battery primarily for its discharge capability. Now we are seeing economic storage durations approaching 4 hours, which lend themselves to energy-shifting roles in which the charging capability comes into play as well as the discharge mode. The economics of longer duration storage will continue to improve but the optimum arrangement will vary site by site.
Funding for advancing novel long-duration energy storage (LDES) technologies has increased by 36 times over the past 5 years[1]. While lithium-based batteries still dominate and are likely to continue to do so for the foreseeable future, many more types of storage are now possible, including metal-air, pumped hydro, compressed air, flow batteries, gravity, thermal and various novel chemistries. Some storage technologies require specific topography and geology, for example pumped hydro and large compressed air storage, and others are at varying stages of technical readiness. Flow batteries of various chemistries are experiencing a significant amount of support aimed at breaking through the long-term storage cost barrier, though this is yet to be achieved at scale, and more likely to be competitive at longer durations (>10 hr) and in larger sized systems (>100 MW).
It is clear, however, that finding the best LDES for a mine project is not just for the mining sector to solve alone. The entire global power industry is looking at storage – and the mining sector can take full advantage of this as LDES evolves. What the mining sector can do right now is to identify the energy use and demand side opportunities that various storage durations could unlock for their projects.
Another key learning we have found over years of hybrid system development is that not every bit of energy produced by renewables needs to be stored. Some can be spilt or, better still, adjustments can be made on the load side to better match the variability in generation. Once the system stability, reliability and demand-side opportunities have been addressed, the storage of ‘spill’ really comes down to economics, which will change over time as storage costs decrease.
Collaboration and risk management
With all these new approaches and possibilities – and the many factors that always come into play such as mine life, capital limits and risk – it’s possible to over-analyse. Not every new project needs to break barriers and set new records. There is definitely still a place for choosing the low-hanging fruit, as the primary case for renewable hybrids being cheaper than thermal-only is well established. You will never really be able to answer every question in a single project – or even predict every question that might arise.
This is where you simply don’t have to go it alone. The key to overcoming hesitation is collaboration. Getting the correct advice is always worth the investment, as is sharing learning at an industry-wide level. There are many players that specialise in one or more aspects of the future mix of technology, mining process, hybrid power operation, renewables knowhow, integration skills, commercial thinking and so on – and bringing these skills together is a must.. Collaboration is the key to solving problems, reducing risk and its appropriate allocation, and a successful project that will benefit all industry players more than competition and working in isolation.
We also believe in learning by doing, through delivery of a specific project. Forming a group of key parties to drive forward a tangible project makes it far more manageable. In innovative projects, ‘pushing risk through’ often just comes back as significantly increased cost. A better approach in these cases is a shared risk profile. The learning is a significant part of the return in early adoption.
Are the right people and the right materials available?
The industry is already experiencing a shortage of experienced hybrid system operators. This needs to be managed through increased training and backup. We believe that operational personnel should be engaged very early in the design of a hybrid power system so that they can have input into development of the system, gain familiarity with it, and consequently feel a level of ownership of the assets.
It is also important to have a close relationship between those involved in the mining process and those operating the power system. For the power system operators, this is a chance to better understand the criticality of various mine plant processes; for the mine operators, it’s a chance to get a better understanding of the mix of operation modes that can be used to meet the mine’s changing power needs.
In many ways, the people skills and resources needed across all the project delivery stages (design, deployment, operation, maintenance and support) are more important than the technology – and this needs to be considered carefully for hybrid projects to be successful.
Finally, neither the mining industry nor the energy sector at large will be able to transition to renewables if we don’t have the right minerals and materials on hand to manufacture clean energy technologies such as wind turbines, solar panels and batteries. Having the mining industry supply these resources in a sustainable way is a powerful contribution to the clean energy transition.
ABOUT THE AUTHOR
Ray Massie has more than 30 years of expertise in renewable energy technology. He managed the development phase of the Hydro Tasmania iconic King Island Renewable Energy Integration Project (KIREIP) and Flinders Island Hybrid Energy Hub as well as undertaking key roles for hybrid system projects at Coober Pedy, Rottnest Island and more recently EDL’s Agnew Hybrid Renewable Microgrid powering Gold Fields’ Agnew Gold Mine and Scott Base in Antarctica.
Entura is an expert in hybrid off-grid renewable energy systems, from our world-leading King Island Renewable Energy Integration Project through to large-scale off-grid mining solutions such as EDL’s Agnew Hybrid Renewable Microgrid, powering Gold Fields’ Agnew Gold Mine. If you would like to talk to us about integrating more renewables and storage into your energy equation, contact Patrick Pease, Donald Vaughan or Greg Koppens.
[1] “The long and the short of energy storage tech”, Climate Tech VC (CTVC), March 2023
MORE THOUGHT LEADERSHIP ARTICLES
What is the value of conventional and pumped hydro storage in a transitioning energy market?
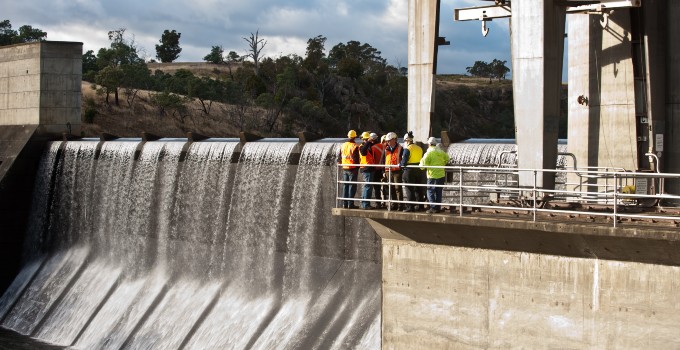
Entura’s Technical Director Power, Donald Vaughan, presented a paper at the global CIGRE Symposium in Cairns, Queensland in September 2023. This is a short summary of the outcomes of the analysis presented in his paper, regarding the value and roles of conventional hydropower, pumped hydro and battery energy storage as the power system transitions to a greater proportion of variable renewable energy in the form of wind and solar PV.
There is a growing need for firming and/or storage in our power systems as we move from predominantly dispatchable sources of power to variable renewable energy (VRE). In the Australian context in the National Electricity Market (NEM), the volume of storage required is expected to be around 46 GW (640 GWh) by 2050 (AEMO 2022). Multiple sources, technologies and methods are being considered but it may be that conventional hydro as well as the more obvious pumped hydro and battery energy storage (PHES and BESS) can play a role.
How do we value storage?
Storage can be valued in many ways. For pure storage, like BESS and PHES, value in a market sense can be measured based on the arbitrage between charging and discharging. Similarly, we can place value on a firming function for VRE. It is more difficult to value the restraint of generation at one time so that stored or withheld energy can be used later. This is the kind of storage offered by conventional hydro sources.
One way of thinking about value is through a measure of realised value vs average value in the market for a particular generator or group of generators. This ‘value factor’ approach is an appropriate measure for storage if we are measuring storage as a contributor to meeting market demand (either local or via interconnections).
One of the problems with the value factor approach is that it is difficult to apply properly without considering market price changes. Introducing plant that can effectively change demand profiles (such as PHES or BESS) will also change the market price, making it difficult to calculate value factors without complex market modelling.
We can instead measure the value of storage by assessing its ability to firm VRE. The measure is based on the ratio of smoothed to unsmoothed VRE with and without the storages applied.
Where there are large amounts of VRE, flexibility from market participants can be valuable. In terms of hydropower generation, conventional hydro plant (storage, Run of the River and head waters) has sufficient flexibility to provide significant market value for modest levels of VRE.
The scale of the transition to VRE will, however, exceed the capacity of conventional hydro to manage variability. Other forms of firming and actual energy shifting, rather than just energy withdrawal (as conventional hydro provides), will be required once the energy balance tips towards energy coming predominantly from VRE sources, with the associated need to manage large diurnal variability as well as longer, weather-based variability. Pumped hydro and battery energy storage will play an important role in providing this more flexible storage.
The role of PHES and BESS in firming
The BESS high power-to-storage ratio allows it to respond to a series of short-lived surpluses or deficits. The PHES deep storage allows it to manage longer duration surpluses or deficits.
The ultimate mix between PHES and BESS in the market is likely to be driven by several factors including the rate of VRE development relative to the level of inter-connection, load growth and VRE mix.
The nature of the VRE will also play a role in determining the storage mix. A predominance of solar will lead to a diurnal pattern that will allow all storage forms to recharge more regularly than would be the case with wind alone. This may allow shallower storage to manage evening peaks with deeper storage reserved for baseload operation overnight.
The economics of BESS and PHES will also play a role in determining the right balance. The market demand for batteries for other purposes and the high market demand for power electronics may yet lead the price/MW of these two storage forms to begin to converge and to limit the depth of storage that will be possible using BESS. PHES on the other hand requires long-term planning, complex approvals processes and less certainty in terms of capturing value from the market. The Integrated System Plan (ISP) of the Australian Energy Market Operator (AEMO) forecasts a large requirement for PHES as deep storage and some very large projects are beginning to be planned.
As these factors play out, the appropriate mix of BESS and PHES will become clearer – but both will certainly play a role in Australia’s clean energy transition.
For more information about the analysis behind his paper, or to discuss how conventional hydropower, pumped hydro and battery storage can be valuable to your situation, contact Donald Vaughan.
How to avoid analysis paralysis
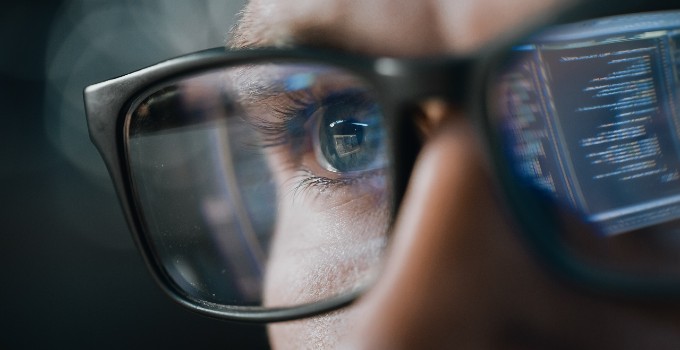
Modelling has a very important role in every sphere of engineering. Complex mathematic models help us better predict and understand behaviours and performance so that we can solve technical problems, push the boundaries of applied science, and optimise construction and manufacturing.
We use finite element models (FEM) to determine the forces, stresses and deflections of a complex structure. We use computational fluid dynamics (CFD) to analyse complex three-dimensional hydraulic problems and determine flow vectors, velocities, water depths and pressure fluctuations. A complex finite difference model (such as FLAC) helps us model complex geotechnical problems. A rainfall–runoff model supports our understanding of potential flooding along a river channel.
In the 30+ years that I have worked in civil engineering, computing power has increased dramatically. As a result, modelling tools have become more powerful, enabling engineers to model increasingly complex principles and problems. For example, we can model non-linear stress–strain properties of materials, rather than simply assuming that they are linear. We can model the turbulent nature of water hydraulics, rather than assuming that the flow is laminar.
The advantage of having more powerful and more extensive modelling tools available to engineers is a significant improvement in our understanding and therefore, in many cases, a corresponding improvement in the engineering. But there is a potential downside: the risk of ‘analysis paralysis’, which is when our ability to make timely decisions is impeded by over-analysing or over-thinking scenarios or alternatives.
I am not a psychologist, but some say the root cause of analysis paralysis is the fear of making the wrong decision, choosing the wrong option or missing out on a potentially superior solution. This fear drives ongoing analysis, and the result is a loss of the expected or potential value of a timely, successful decision. Rather than making a decision, we try to preserve all existing options, continuing to analyse and refine.
This might look like a lower risk strategy, but it is actually a losing strategy. Complex modelling with an overload of scenarios, alternatives, sensitivity analyses or options can overwhelm the situation, making it very difficult to reach conclusions and make the decisions that are inevitably needed to move the project forward. This can potentially cause a bigger issue than if a decision had been made earlier. Prolonging the modelling and analysis phase will merely postpone, not eradicate, the risks associated with implementation. At some point, implementation will be expected.
It is very important to always remember the purpose of modelling, which is to help us understand a problem in order to make decisions – in many cases, engineering decisions. Engineering should drive the process. Although we may be able to refine a model further, perhaps we already have sufficient understanding to make the necessary engineering decisions, so the extra refinement is superfluous. Just because you can refine a model, or add complexity to a model to better reflect reality, doesn’t mean you should. The more refined and complex a model becomes, the more time is required to develop, analyse and interpret the results. It also becomes harder to validate the results, which is critical; blind faith in any complex numerical model is dangerous.
Early in my career, in relation to finite element modelling of dams, a mentor advised me to start simple with the model, validating the results against real data and known engineering behaviours to develop confidence in the model before adding further complexity. A big driver for this process was the extensive run times of these models three decades ago. Despite the progress in modelling over the decades, I believe that there is still a lot of merit in this gradual process of building complexity into a model. However, due to the software and computing power available today, a high degree of complexity is often built into a model right from the start. When this occurs, the modelling can become less of an engineering tool and more like a dark art.
The computing power available today certainly offers engineers access to some amazing inputs for our design processes. But numerical modelling does not replace the engineering. No matter how much modelling we do, we must still eventually make some important engineering decisions. If further refinement of the model won’t change the engineering decision, it’s time to stop. Don’t fall into the trap of analysis paralysis!
In summary, my tips for avoiding modelling paralysis are:
- Keep the purpose of your model in focus.
- Start simple and add complexity to your model only as required.
- Validate your models and ensure confidence in the results.
- Before refining the model, consider whether it will help your decision-making or if you already have sufficient understanding to make your decision.
- Remember that modelling does not replace good engineering practice and decision-making.
- Know when to stop modelling. Come back to the problem you are trying to solve or the decision you are trying to make.
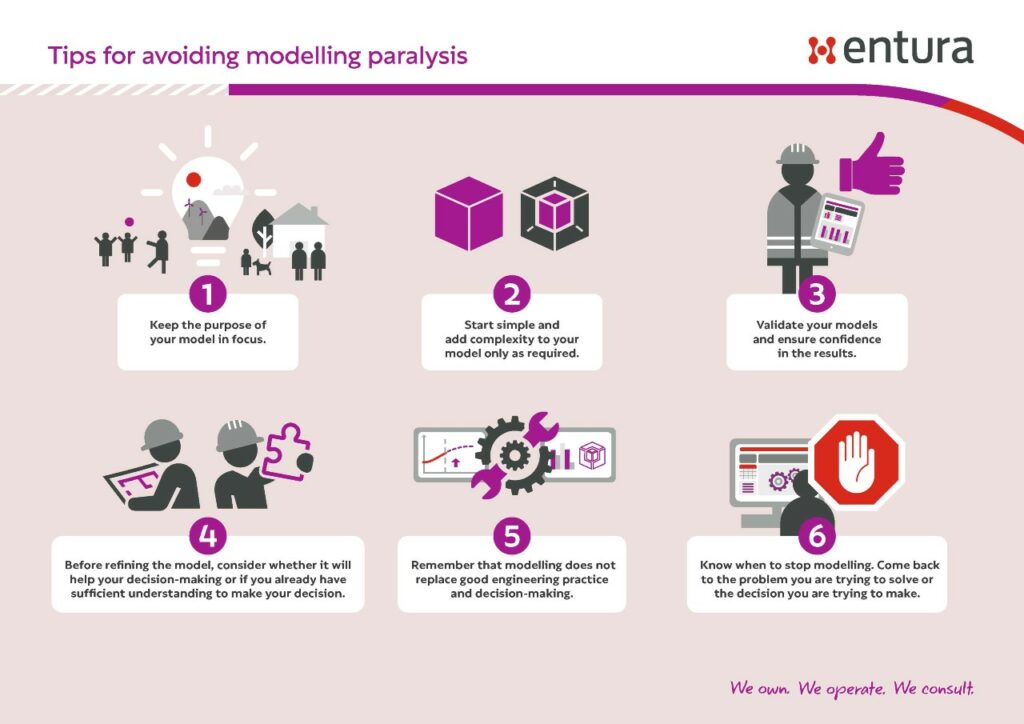
To talk further with an Entura specialist about your modelling challenges, contact Richard Herweynen.
About the author
Richard Herweynen is Entura’s Technical Director, Water. Richard has three decades of experience in dam and hydropower engineering, and has worked throughout the Indo-Pacific region on both dam and hydropower projects, covering all aspects including investigations, feasibility studies, detailed design, construction liaison, operation and maintenance and risk assessment for both new and existing projects. Richard has been part of a number of recent expert review panels for major water projects. He participated in the ANCOLD working group for concrete gravity dams and is the Chairman of the ICOLD technical committee on engineering activities in the planning process for water resources projects. Richard has won many engineering excellence and innovation awards (including Engineers Australia’s Professional Engineer of the Year 2012 – Tasmanian Division), and has published more than 30 technical papers on dam engineering.
MORE THOUGHT LEADERSHIP ARTICLES
How can an Owner’s Engineer smooth the progress of a renewable energy project?
Throughout the renewable energy sector, there are plenty of examples where decisions made during the planning and procurement phases have caused difficulty during construction and affected future operations. A smoother construction process is to everyone’s advantage – avoiding cost blow-outs and time over-runs, and a lot of unnecessary stress and sweat.
An experienced Owner’s Engineer can provide an extra level of continuity and foresight to help reduce risk and minimise surprises. Having independent eyes focused on ‘doing it right’ from the earliest stages is an investment in keeping a project on the path to success.
Here we discuss a few simple and practical opportunities where an Owner’s Engineer can make a meaningful difference to progress.
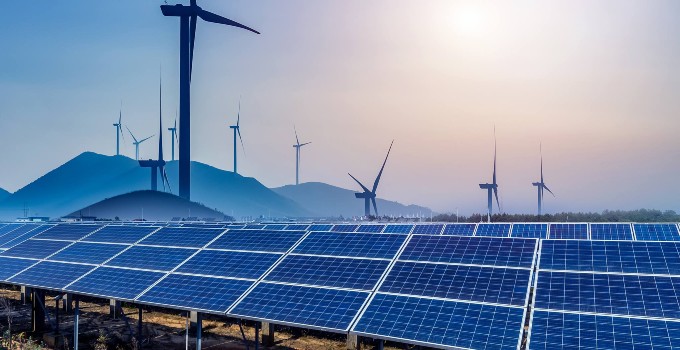
Providing critical continuity
Continuity during the development lifecycle of a renewable energy project can sometimes be difficult to maintain. Transitions occur when project ownership changes, people come and go, government policy shifts, and when the project transitions from one development phase to the next. An Owner’s Engineer who is part of the project through all the phases of development can add a valuable perspective and source of knowledge to the project team through these transitions.
The Owner’s Engineer can apply industry-wide learnings and experience to identify risks and detect opportunities to maximise value in both the immediate detail of the project as well as later stages of the development’s lifecycle. This increases the likelihood that the transition between lifecycle phases – such as when a project advances to construction, or the handover of a newly constructed asset to an operations team – will be smooth and successful.
Maintaining order and good process
In a project where schedule risk is a big concern to all involved, sometimes good process falls to the wayside. The appropriate order of studies, design validation and construction can be impeded by a desire to get construction underway as soon as possible. Good forethought, data, modelling, discussion and design validation take time, but they are essential inputs for a successful outcome. A rush to get construction underway before this process is concluded increases the chances of re-work being required – a risk that’s always best avoided.
Identifying knowledge gaps
Having an independent Owner’s Engineer involved in a project from the beginning of the development and design process means that there is an independent expert who can review early technical studies, and identify where there may be gaps in the analysis. These early technical studies ― such as geotechnical studies for foundation and road design, and soil thermal resistivity testing to inform the right choices for cable sizing and trenching ― can have major impacts on the cost and effort expended during the design process, and the type of design that is required for a successful project. If these studies aren’t completed early enough, or thoroughly enough, there will be higher risks for the EPC contractor bidding on a project, hence higher cost. There may also be delays in the design process and at critical construction stages, with costly ramifications.
Thinking through logistical constraints at planning application stage
Construction of a wind farm, solar farm or hybrid renewable project is always a logistical challenge. For example, wind turbine components are massive, and getting bigger all the time. Rural roads are rarely of the width, camber and capacity to handle the large vehicles needed to carry materials, components or machinery. They may also not cope well with the volume of truck movements required. Community preferences and planning constraints can also limit the number of truck movements to and from sites per day.
Another important consideration in the construction of large renewable energy projects is how to move cranes around the site. In the case of a wind farm, will it be more effective to choose a crane that can be disassembled after erecting each turbine, moved in sections, and reassembled at the next turbine site? Or will it be quicker and cheaper to drive a crane between turbines? Given the potential for the width of the crane to overflow the width of the local roads, such a decision needs to take into account the potential for additional environmental approvals for a wider area of disturbance.
These challenges need to be carefully considered as early as possible in the planning application stage. Time and effort spent on the planning application can make a big difference to the ultimate project outcome. As the project progresses, clear sequencing and communication is vital for keeping things moving smoothly while also adhering to the constraints of construction and transport conditions.
Writing and enforcing clear specifications
A project’s technical specifications and the contractor’s response to them ultimately determine the end quality of the project. For both the owner and the contractor, it is vital that specifications are unambiguous and reflect the owner’s technical requirements and desired quality for the project. The Owner’s Engineer can help improve specifications based on their experience, for example specifying what sort of fixings can be used to hang cables below the solar panels, thus impacting long-term lifetime and maintenance costs.
When it comes to following specifications during the design and construction process, strict is good from the owner’s perspective. If the Owner’s Engineer rigorously enforces the specifications from the start, it sets the tone and expectations for the rest of the construction process and is likely to result in better project outcomes and fewer issues arising down the track.
Identifying safety issues and opportunities for improvement
An Owner’s Engineer brings a breadth of experience to a project as well as a clear pair of eyes and the ability to see the details as well as the bigger picture. The Owner’s Engineer is therefore well placed to identify potential safety issues and suggest improvements throughout design and construction. The Owner’s Engineer is involved in all stages of design, so is able to suggest safety improvements during safety-in-design and hazardous operations workshops. This can improve the chances of having issues of construction sequencing, construction safety or operational safety issues raised early in the design stages.
Construction inspections are often undertaken by a regular team member as well as a range of specialists. The regular team member creates continuity and the ability to compare practices on site over time. The targeted inspections by specialists focus fresh eyes on any potential issues arising during key milestones of construction.
Bringing a unique perspective
In our experience, the Owner’s Engineer can play a very valuable role in any project: helping to minimise risks such as construction delays and difficulties and maximise opportunities to achieve ‘best for project’ outcomes. The Owner’s Engineer brings a unique perspective: the ability to see a project from all angles, to maintain an independent view, and to filter everything through the lens of experience.
At Entura, we’re privileged to work with specialists who have been involved in both the design and operation of many power and water assets across their careers. They have worked with assets over the full lifecycle, so their insights stem from deep real-world experience. This ‘owner-operator’ perspective is not common among consultants, and we’re proud to apply it to help our clients get the best from their projects.
If you would like to discuss how Entura can help you with your renewable energy project, please contact us.
About the authors
Kate Hammerton is a Renewable Energy Engineer with a passion for hybrid energy systems and isolated micro-grids. She is involved in managing multi-disciplinary teams as the Owner’s Engineer on utility-scale renewable energy construction projects across Australia and the Indo-Pacific region, including the Agnew Hybrid Renewable Project, the Rottnest Island Water and Renewable Energy Nexus Project (WREN), Antarctica New Zealand’s Scott Base redevelopment at Ross Island, Tasmania’s Cattle Hill and Granville Harbour wind farms, and implementation of 14 MW of battery systems in Tonga.
Andrew Wright is a Specialist Renewable Energy Engineer at Entura. He has more than 15 years of experience in the renewable energy sector spanning resource assessment, site identification, equipment selection (wind and solar), development of technical documentation and contractual agreements, operational assessments and owner’s/lender’s engineering services. He has an in-depth understanding of the energy industry in Australia, while his international consulting experience includes New Zealand, Antarctica, China, India, Bhutan, Sri Lanka, the Philippines and Micronesia.
MORE THOUGHT LEADERSHIP ARTICLES
Making progress in the field, despite pandemic challenges
While some aspects of fieldwork can be modified through technological innovation, there are other things that simply can’t be done without getting out on the ground or in the water. How can we make fieldwork not only efficient and effective, but also COVID-safe?
For our Environment and Planning team, interstate and intra-state travel restrictions and work-from-home orders rolled in at the height of the field season when most summer and autumn seasonal surveys were being completed and when many in the team would usually spend multiple days each week in the field. We’ve managed the fieldwork challenges through practical modifications for greater safety, taking confounding factors into account when analysing our results, using technology to support fieldwork, and collaborating with our clients, partners and local businesses to find solutions together.
Practical modifications for safety and wellbeing
Despite the restrictions and changed conditions brought about by COVID-19, we have been keen to find safe solutions to continue working seamlessly with our clients. Our teams have adapted their fieldwork patterns and adopted stringent methods, including fieldwork procedure reviews, undertaking day trips rather than longer trips where possible, reducing the number of people per field trip to the practical minimum, maintaining social distancing, and practising good hygiene, such as wiping down equipment and common touchpoints, from car gear sticks to the helms of our boats.
For example, our aquatic scientists are braving the Tasmanian winter chill to ensure that water quality and monitoring datasets for Hydro Tasmania continue to be logged. This data is critical to understanding impacts on aquatic fauna, and forms part of a multi-year monitoring regime for many of the state’s water bodies. The team would normally be undertaking week-long field trips; however, in response to the pandemic and due to the temporary closure of many accommodation options, the trips are shorter and efforts have been made to avoid the virus hotspots within the state wherever possible.
Managing fatigue is always important when undertaking field work, and especially so during COVID-19. For most field work, physical distancing requirements have ruled out travelling in a single vehicle. However, travelling in separate cars means that the driving can’t be shared. To manage fatigue associated with driving, we have made field days shorter, or, if more practical, we’ve stayed overnight in local self-contained accommodation to avoid travelling after long working days.
Mental wellbeing has also been a crucial consideration while living and working through the pandemic. Our teams have stayed connected, whether working at home or in the field, through more virtual team catch-ups, quiz nights and virtual Friday post-work-week banters. Picking up on cues that indicate someone may be struggling is more difficult over email or a phone or video call than when working together in the office, so it’s more important than ever to actively check in on each others’ and our own wellbeing. At Entura, ensuring staff mental and physical wellbeing is always a high priority – and, particularly during the pandemic, taking time out to breathe and declutter the mind has helped us avoid mental burnouts and kept us as motivated as ever to deliver outcomes for our clients.
Taking confounding factors into account
Our ecologists have continued to undertake their monitoring programs, including night-time roadkill surveys along lengthy stretches of winding wilderness roads to look for threatened fauna such as quolls, Tasmanian devils and wombats. One of the challenges of undertaking this work during the pandemic has been the potential that the data collected may be confounded by reduced traffic volumes, making it questionable as to whether the data collected can be applied to a post-COVID world. In addition, reduced traffic volumes may also be influencing wildlife habits – for example, making them less wary of roads.
When interpreting the data, we took these potential implications into consideration, and some monitoring regimes were extended to compensate for potential changes to usual patterns. This will help ensure that the monitoring program provides a realistic representation of trends from which ongoing management decisions can be made.
Minimising fieldwork through technology
Entura has been actively assisting with Hydro Tasmania’s Battery of the Nation initiative. This initiative, jointly supported by the federal government (through the Australian Renewable Energy Agency) and state government, is investigating and developing a pathway of future development opportunities in hydropower system expansion including pumped hydro. For our Environment and Planning team and our Spatial and Data Services team, fieldwork for their involvement in Battery of the Nation has been able to continue, albeit with some innovative adaptations.
The spatial team has developed robust methods for visual impact analysis that can be applied to multiple project locations and types. To meet COVID-19 fieldwork guidelines, minimal staff have ventured into the field. These smaller teams have used technology to send real-time information (such as geo-tagged photos) to a pre-arranged server, allowing others at the ‘office’ to access the information almost immediately. The data has included light detection and ranging data, 3D models of project elements and real-life photography, which has been processed to generate 3D walkthroughs and web-scenes. These provide an important output for the project, but are also a useful tool for other team members to understand the site context without needing to go into the field themselves.
Solving problems through local collaborations
In some cases, overcoming the fieldwork limitations of COVID-19 has required a higher than usual level of collaboration with clients, partners and other organisations. For example, when the pandemic travel restrictions prevented the original interstate consultant from travelling to Tasmania as planned, our surveyors and ecologists were called in to assist our local partner TasNetworks with an important project on Bruny Island in Southern Tasmania. The submarine cable from mainland Tasmania that ensures security of electricity supply for the Bruny community is currently being replaced after the existing cable was damaged beyond repair late last year. Our proximity made it possible to step in to help. In a display of local collaboration, Entura assisted with the bathymetric and cable trenching clearance surveys, passing the data on to TasNetworks’ cable design engineers so that planning for replacement of the cable could continue.
Anticipating the ‘next normal’
In Tasmania, we are fortunate to be gradually emerging from COVID-19 isolation and we are eagerly awaiting the return of our ability to undertake the works and visits we have had to delay, yet we’re well aware that some changes or restrictions may be with us for quite some time yet. For now, we will keep working closely with our clients to be agile and resilient, so that together we can find safe and innovative COVID-friendly ways to move our projects forward.
If you would like to discuss how Entura can help you with your environmental or planning project, please contact us.
For more articles from our Environmental and Planning team, visit our Thought Leadership collection, where you’ll find their articles about maintaining the progress of international projects and the challenges of starting new projects during the pandemic and the changes it has brought to planning regimes around Australia – amongst many more articles of interest to anyone involved in the power and water sector.
MORE THOUGHT LEADERSHIP ARTICLES
New circumstances, new projects, new regulations
It’s a major challenge to keep an existing local project running during these tricky times (let alone an interstate or international project!), but how can we start new projects as the ground shifts around us and as regulations around Australia change?
In this third article from Entura’s environment and planning team, we feature a recent win in the national water infrastructure space – the detailed design, and planning and environmental approvals for a new off-creek storage in the Northern Tablelands of New South Wales. And we take a look at how regulatory changes are playing out around Australia to provide greater flexibility to respond to current constraints.
Starting a new project during a pandemic
Entura, working together with Hunter H2O, is now assisting Walcha Council with a regionally significant project despite COVID-19. The township of Walcha is currently serviced by one small off-creek water storage, which means that stringent water restrictions are needed during periods of drought. The regional council, supported by federal government funding, is investing in improving Walcha’s water reliability and security, which will also deliver social benefits to the community.
Our team tendered successfully when COVID-19 was yet to hit our shores, but in a mere few weeks we found ourselves loading up our office gear to set up from home. The same week that our engineering, planning and environmental specialists were scheduled to fly to Walcha to meet with Council on site, travel restrictions intensified and flying out of Tasmania was no longer an option. We adapted by taking to virtual platforms to communicate with our client about the challenges imposed by COVID-19 and how we could still keep the project moving, albeit with some deviations from the original schedule.
As a multidisciplinary firm capable of working across many jurisdictions, we pride ourselves on the relationships we have established with local contractors. In these times we are even more aware of the benefit of these associations to help keep the work flowing. For this project, collaboration with local contractors and swift adaptation has allowed the team to keep the project moving forward. Local geotechnical contractors have begun their investigations to feed information to our teams. Meanwhile, our environmental and planning experts have studied databases and existing literature to determine potential terrestrial, aquatic and regulatory constraints that may affect the design of the new off-creek storage.
Lockdown restrictions are starting to ease across the nation, but for now we are sitting tight and waiting until it is safe to visit the site. We need to ensure that storage design works are undertaken only when our technical specialists have stepped foot on the site themselves and have a thorough understanding of the site context. In the meantime, we continue to provide value through virtual meetings and workshops with our client. Hunter H2O and Walcha Council share our view regarding both the safety of our people and the quality of design required for the project.
On this constantly shifting ground, we are keeping the regulators up to date with the progress of the project, and we are also ensuring we keep up to date with any regulatory changes which may affect the project and that these are well-communicated with our client.
Regulatory changes for flexible responses
Across the country, state governments are establishing new measures to accelerate projects to shovel-readiness to help buffer the social and economic impacts of the pandemic. They’re also making temporary orders to existing legislation to provide flexible planning and environmental responses.
New South Wales
In New South Wales, the Planning System Acceleration Program has been introduced to fast-track State Significant Developments, rezonings and development applications, as well as provide support to decision-makers to speed up local and regionally significant projects to approval. Temporary orders have been implemented to allow some infrastructure construction work to be carried out on weekends to maintain productivity and employment in the sector. In NSW, temporary changes to the Environmental Protection and Assessment Act 1979 (EP&A Act) allows the Minister for Planning and Public Spaces to authorise development to be carried out on land without any approval under the EP&A Act where that development is required to protect the health, safety and welfare of the public during the COVID-19 pandemic.
Other recent legislative change in NSW is the long-awaited amendment of the NSW Bilateral Agreement under the Commonwealth Environment Protection and Biodiversity Conservation Act 1999 (Cmwth), which was required after the introduction of the new Biodiversity Conservation Act 2016 (NSW). This updated bilateral agreement has allowed environmental assessments and offsets to be streamlined, including endorsement of the NSW Biodiversity Offsets Scheme for the purposes of offsetting for a Commonwealth approval.
Queensland and Western Australia
In Queensland, COVID-19 has been declared an applicable event under planning legislation, thus allowing the Planning Minister more flexibility to suspend or extend any statutory timeframe across the planning framework if required. Similarly, in Western Australia, the Minister for Planning has issued a two-year extension for all current development approvals to assist job-creating projects during the recovery stage, along with other exemptions from planning approval for essential local community services.
Victoria
The Victorian Government has announced temporary measures to make sure that planning and approval processes can continue to function despite remote working arrangements, including allowing local government planning authorities to make decisions under delegation to facilitate efficient application turnaround times. The Victorian Government has also established the Building Victoria’s Recovery Taskforce to explore planning and investment opportunities to boost the development industry. Additionally, the new Victorian Environment Protection Amendment Act 2018 (EPA Act), which is relevant to many infrastructure projects, was to take effect from 1 July 2020 but has been deferred until July 2021 to ensure developers, consultants and regulators have time to adapt to changes in workload and workflow as a result of the pandemic.
Tasmania
Tasmanian planning reform continues with the exhibition and assessment of local planning schedules as part of the transition to a statewide planning scheme. Consultation has also concluded on the proposed process for major projects, which, if enacted, will be the state’s first multi-permit approval process.
Nationwide
The Commonwealth Environment Protection and Biodiversity Conservation Act 1999 is also currently being reviewed, and our planning and environmental consultants are ensuring that they keep pace with the impending changes and implications for ongoing and new projects.
Managing change
For the Walcha project, the approval process is comparatively simple and the changes to approval processes are not likely to impact the project. However, for some of our other projects, these changes create challenges. Most notably, physical distancing requirements have meant temporary shutting of council offices and town information centres where application documents and technical studies are usually displayed. Instead, full suites of application documentation are being published online or, when specifically required, hardcopies are being mailed out. With postal services already under pressure, one way to ensure the community has a fair opportunity to provide feedback is to lengthen comment and consultation timeframes.
Although the global pandemic may have been disruptive to our work arrangements, smart and innovative ways to juggle project commitments and changed circumstances have fostered strong relationships which will persist beyond COVID-19. Elevated levels of trust and virtual teamwork with clients will surely present more opportunities to collaborate once the ground settles and we reach a new equilibrium.
If you would like to discuss how Entura can help you with your environmental or planning project, please contact us.
MORE THOUGHT LEADERSHIP ARTICLES
Keeping international projects moving, even when we’re grounded
With no set date for when life will return to usual after COVID-19, nor any guarantee of whether life will ever return to what we previously knew as ‘usual’ at all, there are very few areas in the consulting life in which we can simply say ‘we’ll wait until this is all over’. Life, and projects, must go on.
Although we can’t avoid the disruption and uncertainty that the coronavirus has unleashed, we can increase our resilience and agility. We can also embrace opportunities to innovate and to create new ways (or reinvigorate old ways) to achieve our goals.
Here, Entura’s Environment and Planning team continue to apply their proactive approach to keeping projects alive in the current circumstances, and explain how they are continuing their activities on two international projects despite the travel restrictions that are making it impossible to visit the project sites.
Old ways for new times – Engaging communities in Tonga
For many countries across the globe, the immediate challenge is building resilience to fight through the pandemic. However, for some small island nations that have managed to stay out of the virus’s path so far, such as Tonga and the Federated States of Micronesia, the concept of resilience has a broader context.
Climate resilience is a core objective, as these nations are feeling the increasing impacts of rising sea levels and more frequent and intense weather events. In this context, robust power infrastructure that is suited to extreme weather is one component of greater resilience, as is transitioning from diesel dependence to higher levels of renewables, which builds greater security of energy supply at a lower longer term financial and environmental cost. More access to stable, reliable and clean electricity is also critical for the health, wellbeing and education of local communities, and is the foundation for economic development. Entura has been fortunate to be involved in some meaningful resilience-building projects in the Pacific, supporting many of our neighbouring nations to implement sustainable energy solutions.
However, with a current project in Tonga, coronavirus has thrown our travel plans into disarray. The challenge we’re facing now is how to continue the planning, engagement and environmental activities required by such a project when we can’t physically get there, can’t hold town hall meetings and can’t host information sessions with locals.
While the pandemic is forcing many practitioners to extend and expand their use of digital forms of engagement (such as websites, Facebook, Twitter, ‘Bang the Table’ or moderated ZOOM-based focus groups), some projects are located in communities that do not enjoy easily available or reliable internet or telephone access. In these cases, such as our project in Tonga, we need to think differently about ways to facilitate engagement from a distance.
For the Tongan project, we’re heading back to basics: the tried and tested solution of providing information on paper. Working with the local project management unit, along with our client, we are designing and implementing a newsletter to be printed in the local language and distributed to regulators and communities. It will provide snapshots of the project, latest updates on scheduling, and will even feature some interviews to provide greater coverage of ongoing community engagement.
As the construction company for the project is, like us, unable to travel internationally at the moment, construction is yet to take place. Nevertheless, we are continuing to facilitate all aspects of the project remotely, such as lining up approvals with regulators, and guiding engagement on the ground. With the help of our Tongan counterparts, we can still keep information and updates flowing despite the physical limitations on our involvement ‘in the flesh’.
Buying time and building partnerships in South-East Asia
Just as COVID-19 started closing borders and halting international travel, our team was reaching the culmination of many weeks planning an impact assessment for a large infrastructure project in South-East Asia. Our discipline experts were about to book their tickets and embark on the journey to site to survey environmental and social impacts. However, we placed the site surveys on hold indefinitely to comply with travel restrictions, ensure the safety of our people and contractors, and not risk spreading the virus in remote communities.
This abrupt shift in our plans afforded us the chance to take a breath, reflect on the project and its broader risks, and then develop an alternative plan to keep progressing aspects of the work that could be done remotely. We are now proactively undertaking desktop approval studies and initial public consultation from our desks. We’re ‘buying time’ now to save time later.
When travel restrictions lift and it is once again safe to physically attend the site, we will be ahead of where we would have been pre-COVID-19. We will better understand potential issues and have a more thorough insight into the local and community context. We’ll have already carefully planned our field studies with more targeted approaches. We’ll be better prepared for stakeholder questions that may arise, and will have already considered ways in which the project might manage challenges and risks going forward.
But there’s something more that we’re seeing emerge in this COVID-19 period. We’re finding that the shared need to adapt to trying times and the mutual desire to find workable solutions is strengthening our relationships with our clients, building even greater trust and collaboration, and it is leading to ‘partnership’ relationships that transcend the more common transactional paradigm of client–consultant. We are working closely together to openly discuss issues and options, and to determine how best to manage emerging challenges to benefit the project.
Would this have happened without COVID-19? Perhaps – but under the usual pressure of timelines, expectations, standardised processes and the drive for efficiency, there isn’t often the same flexibility or space to build different qualities and layers in our relationships or to consider potential issues quite so broadly or creatively.
Will the project benefit from the changes made necessary by COVID-19? Probably – despite the difficulties caused by the limitations on travel, it can only be positive to have had the chance to take the time to more thoroughly and holistically consider all the issues and risks before we proceed to field studies and stakeholder engagement.
Will timelines change significantly because of COVID-19? Not necessarily – we will inevitably lose some months by not being able to go into the field, but we will have ‘bought’ some time by compiling a good portion of the project documentation prior to the field studies, so that the time required in subsequent stages is lessened.
Wherever in the Indo-Pacific region our international projects are located, our clients can be confident that we’re seeking all the ways we can – new or old – to keep making progress in these uncertain and complicated times … and to come through them stronger together.
If you would like to discuss how Entura can help you with your environmental or planning project, please contact us.
Don’t let COVID-19 stop your project
A vital part of the success of all projects, whether they are new or operational, is maintaining progress towards milestones and retaining currency in the social and regulatory realms. How can we achieve this during a global pandemic?
With the COVID-19 crisis affecting people and businesses across the globe, employers and employees alike are racing to find normalcy. Fortunately for Entura, we’ve already been working and collaborating virtually for many years across country and state borders, with dispersed office, client and project locations. So, even though our teams are working from home, it is still business as (mostly) usual, in unusual times!
Although COVID-19 hasn’t thrown us completely, travel restrictions have pushed us to think differently about many of our projects and methods. This is the time to explore proactive ways to ensure projects do not come to a grinding halt or fall off a community’s or regulator’s radar.
Keeping environmental and planning projects moving forward
Entura’s environment and planning team works frequently in the field – lakes, forests, roadsides, development sites and many more – so COVID-19 travel restriction have taken a hit at our ability to undertake survey and monitoring programs or to conduct site visits, but it hasn’t led to tools down.
We may miss out on our chance to hit the frosty outdoors this autumn and winter, but there are still many ways that we can and will continue to make progress and deliver value. It’s about thinking creatively about how we can be proactive. And that means finding measures and activities for the short and medium term that will keep the project moving towards the longer term project milestones and goals (without the anticipated longer term extending into the much further horizon!)
For example, there are proactive things we can do to prepare us better for when we can once again visit the site. We have access to a wide range of data and can undertake thorough desktop investigations early in the project. We will then be able to step on site well prepared and looking to fill knowledge gaps or to verify what should be there. That puts us in a better position to be alert to anything unexpected we might find when we’re physically on site in future. Unusual discoveries and observations will be more pronounced. Such approaches can help shorten project timelines post-COVID-19 compared with the inevitable blowouts that would be caused by downing tools completely.
Policy and regulatory reforms are also still happening across the country – some as a result of COVID-19, others associated with larger reform programs to update antiquated legislation. Our discipline experts continue to engage with the regulators and relevant government agencies and authorities to ensure we understand the nuances of these changes and how they may influence the scope of existing and future projects and programs of work.
More proactive, less reactive
The restrictions caused by COVID-19 have highlighted the need to be proactive so that we can be better positioned for the longer term. It’s natural for a consulting paradigm to tend towards the reactive and process-driven, but this is the time to shift such tendencies.
With a future-focus and forward thinking, we can all seek out proactive solutions to keep projects and processes running as smoothly as possible, to meet any milestones that are still feasible, and to do everything that is reasonably possible in the present circumstances that will minimise delays once the pandemic has eased.
This needs to be a shared process. If as consultants and clients we put our heads together, we can develop shared understandings of the opportunities, risks and issues affecting all parts of the project and all the players involved. With team work and good communication, together we’ll find the most innovative and workable solutions, and together we will survive and thrive.
Beyond the immediate
The circumstances of the pandemic are also an opportunity to think beyond the immediate projects on our desks. This is a great time for our clients to review their projects and environmental and social management practices, to be better positioned for the post-COVID-19 future. This could include being more informed about potential risks or thinking through changes that you could make to your management practices to better address ongoing or emerging issues.
In our next article, we will highlight some of the projects we are currently working on, and how we have adapted them in light of COVID-19. We will also dig down into some of the key regulatory reforms happening across the country, and what implications they may have on projects during the COVID-19 period and beyond.
At Entura, we will continue to respond to government measures as they surface, and we will continue to be here to assist all our clients to better understand the opportunities, risks and issues associated with keeping your project alive during COVID-19.
A message from our team to yours
And to finish on a light note – Entura’s environment and planning team has nimbly settled into their new branch offices, from urban Melbournian set-ups to peri-urban workplaces at the foothills of the majestic kunanyi/Mount Wellington in Tasmania. From our team to you or yours, here are a few handy tips which we have found to help with this transition to working from home:
- Stay connected – drop your colleague or manager a line and ask how they are going, and where possible (bandwidth permitting), turn on the video during your virtual meetings.
- Schedule regular team catch-ups, and why not end the week with an optional virtual gathering to kickstart some weekend banter?
- Don’t be embarrassed if your pets or children make an appearance – it helps lighten the mood and may provide the laugh that someone really needed.
- Get some fresh air before you start work – imitate that commute to work by going for a walk or cycle.
If you would like to discuss how Entura can help you with your environmental or planning project, please contact us.
Pictured, clockwise from top left:
- Senior Social and Stakeholder Consultant, Dr John Cook
- Land Use Planner, Bunfu Yu
- Senior Aquatic Scientist, Dr Malcolm McCausland (and friends)
- Team Leader Environment and Planning, Raymond Brereton
- Senior Environmental Planner, Cameron Amos
- Senior Planning and Environmental Consultant, Scott Rowell (about to head out for a ride)
- Environmental Consultant, Rachael Wheeler
MORE THOUGHT LEADERSHIP ARTICLES
What’s the best technology for your pumped hydro project?
For your pumped hydro project to be suited to future energy market conditions, you need to understand the technology options available – because pumped hydro plant is not one-size-fits-all. Let’s go for a deep dive …
Pumped hydro has been around for more than a century, but in recent years it has leapt into the forefront of the quest for energy storage and firming options as the energy sector embraces increasing levels of renewable energy generation. If you want to get the best from a pumped hydro project, it’s important to come to grips with the implications of the different types and combinations of mechanical and electrical machines that have been developed over the long history of hydropower and pumped hydro.
The choices are among fixed-speed reversible pump turbines, variable-speed reversible units (including doubly-fed inverter arrangement), and ternary sets. Each has its own variations and strengths in terms of the services able to be provided to the energy market. But the technologies also vary in costs, housing requirements and performance.
All pumped hydro projects are likely to offer benefits to the market by contributing to operating reserves, reducing spill or curtailment of variable renewable energy, reducing cycling and ramping of thermal plant, lowering transmission congestion and associated costs, and lowering greenhouse gas and pollutant emissions when used to displace thermal generation. But let’s look at the specific pros and cons of each of the different pumped hydro configurations, and how they compare.
Reversible units
Reversible units comprise a single hydraulic machine (turbine-pump), a single electrical machine (motor-generator) and a single shaft. The unit changes rotational direction to switch between generating and pumping modes.
These reversible units come in two different forms: fixed speed and variable speed. The fixed-speed reversible units can’t optimise the uptake of power from the grid in pumping mode, which is important in a grid with the rapid and frequent fluctuations characteristic of high levels of variable renewable energy. However, with a multi-unit arrangement in a power station, additional flexibility during the pumping cycle could be achieved at a premium.
Variable-speed reversible units provide greater efficiency and flexibility and provide different opportunities for grid support than fixed-speed units in pumping mode. However, should all the thermal plants be retired as the energy market transforms, the lack of synchronous machines could become a major issue where rotating inertia becomes scarce. Asynchronous (variable-speed) machines rely on their power electronic controls to provide inertia. While this can be artificially enhanced relative to synchronous machines, it relies on externally provided system strength which may also be lacking in the absence of thermal units.
Based on recent projects in Australia, the cost of electrical and mechanical equipment for variable-speed reversible units is about 30% greater than for fixed-speed units and the construction cost is approximately 10% more. Yet, while fixed-speed units come at a lower cost, variable-speed machines have the potential under some configurations to provide more valuable services in operation, such as variable load during pumping operation, and as long as there is adequate synchronous generation, inertia distributed around the network.
Ternary sets
Ternary sets comprise two hydraulic machines (a turbine and a pump), coupled on a single shaft, with a single electrical machine (motor-generator). This means that the direction of the turbine is the same in generating and pumping mode. They are often the only solution for projects with very high head but they can be applied for lower head projects too. Without having to change direction, little changeover time is needed between modes, making it possible to respond much faster to the grid. There’s also less stress on the machines, which can be individually optimised. The turbine and pump can even operate simultaneously (in hydraulic short-circuit mode), and the turbine can be used to start the pump (further reducing changeover time).
This description makes it sound as if ternary sets are the way to go … but it isn’t that simple.
Many of the elements of the civil works for a pumped storage project are the same whether fixed-speed reversible units, variable-speed reversible units or ternary sets are used. However, the powerhouse structure for ternary sets needs to be taller or wider (as the units are bigger), penstocks and tailrace branch pipes will require an extra bifurcation, and it is likely that the costs involved in hydro-mechanical equipment such as gates and valves will be significantly greater.
The extra construction costs can add up to approximately 25 per cent more than for reversible units. And the additional electro-mechanical equipment could come at a 35 to 50 per cent higher price tag compared to the fixed-speed reversible units. However, countering the increased cost of ternary sets is their likely efficiency gain of 2 to 3 per cent and a faster response time than reversible units are capable of.
The increasing need for fast response
Adopting either variable-speed reversible units or ternary sets appears, on the face of it, to be more expensive than fixed-speed reversible units, but there are mitigating circumstances that make them worthy of serious consideration.
With settlement periods in the Australian National Electricity Market reducing from 30 minutes to 5 minutes, fast response is critical. Both ternary sets and variable-speed reversible units have a big advantage over fixed-speed units in this regard, but fixed-speed units can work with the 5-minute settlement if they are utilised appropriately as part of a pumped storage scheme.
Short-circuit mode
Reversible units and ternary units require similar amounts of power from the grid in synchronous condenser mode. For a 125 MW unit, the grid power required is estimated at about 4 MW.
Some projects investigating the idea of hydraulic short-circuit with variable-speed, doubly-fed inverter machines are currently underway. In essence, a waterway is shared between two units with a bifurcation upstream and downstream of the units. In this case one of the units will operate in generating mode and the other in pumping mode.
What’s the answer?
There’s a lot to take in when comparing the different pumped hydro configurations. It’s generally accepted that variable-speed reversible units and ternary sets have certain advantages over fixed-speed reversible units in a changing energy market. Yet, in some cases fixed-speed units will do the job, and at a lower cost, whilst at the same time guaranteeing synchronous generation if rotating inertia is of essence to grid stability. There’s no clear-cut winner when it comes to pitting variable-speed reversible units and ternary sets against each other. As usual, the right choice will depend on the specifics of your project conditions and what changes you anticipate as energy markets continue to evolve.
If you would like to discuss how Entura can help you with your pumped hydro or renewable energy project, please contact Nick West on +61 408 952 315, Richard Herweynen on +61 429 705 127 or Phillip Ellerton on +61 439 010 172.
About the authors
Nick West is a civil engineer at Entura with more than 18 years of experience, primarily in hydraulics and hydropower. Nick’s skills range from the technical analysis of the layout of hydropower projects to the preparation of contractual project documents and computational hydraulic modelling. Nick was a key team member of the Kidston Pumped Storage Project Technical Feasibility Study and is currently involved in feasibility assessments of pumped hydro options as part of Tasmania’s Battery of the Nation initiative.
MORE THOUGHT LEADERSHIP ARTICLES
Engineering – by humans, for humans
When engineers think about the future, do we get so engrossed in the complex technical problems that we don’t attend enough to the human angle?
Engineers have a reputation, whether rightly or wrongly, for being poor communicators, working obsessively and in isolation, and focusing on the immediate goal rather than its impacts on communities. Often, clichés have a basis in truth. If we are going to shift perceptions, we need to start by thinking about the way we work and the leadership we show to the next generation of engineers.
There’s no way we can predict the major developments, challenges or solutions of the next five or six generations of engineering careers. What we should focus on is what we can do right now to lead change in our profession and our communities – and I think the keys are communication, collaboration and community.
Communication
I recently listened to a podcast in which two energy market experts talked with a power system engineer. They discussed all sorts of technical matters relating to frequency and voltage control. I love those topics, but this conversation was limited and uninspiring because the participants simply didn’t have a common language or understanding.
We need to learn to communicate in ways that a variety of people can understand. That will mean better conversations with the people who can help our work have greater impact, and it will help our communities to appreciate the importance of our work in their lives.
It’s too easy for us as a profession to sit at our desks or stand under our hard hats and luxuriate in how clever we are, and then bemoan how so many people have no idea what we do and don’t value our work.
When things that involve engineers go wrong, a flurry of opinions erupts. Failures such as the blackout in South Australia, or the cladding issues at the Grenfell Towers, or issues with airlines or bridges or dams all lead to our communities questioning and debating engineering practice. Engineers tend to try to stay out of this rough and tumble for fear of being misrepresented. Yet maybe it’s better that we do engage where we can, since being misrepresented on a small issue is better than allowing a groundswell of misguided public opinion due to a lack of understanding of engineering principles.
We need to try to better explain our work and find simple ways to convey the complexities of the decisions that we make.
Collaboration
The world is far more complex now than it was a century ago – but it is impossible to imagine what level and pace of change future generations will experience. If we want to transform our world or help build a better future, we can’t do it by ourselves.
Engineering no longer operates in isolation, if it ever did. We must collaborate across the engineering team and across other professional disciplines to achieve truly effective development for our communities. Sometimes we may need to focus a little less on technical delivery as a primary outcome, and increase our recognition of the value gained by engaging successfully with the communities on whom the project relies for success.
Collaboration makes our work more effective, and exposes us to a wider range of inputs and values that we can incorporate into our designs and processes. Engineering can be a leader but it can also be a facilitator for better outcomes when we draw on, listen to and learn from the other experts involved in other aspects of our projects.
Community
Engineering work almost always benefits more people than merely the one who pays the bill. Much of my work is in connecting wind farms and solar farms to the grid. Mostly my work is paid for by the owner of the farm, and while it delivers direct benefits to the owner through return on investment, it also affects everyone connected to the nearby network. It affects the network service provider and market operator, it pays salaries, and it supplies the clean energy that helps the country reduce emissions and meet its international targets. In other words, my work, which may seem intangible, has tangible effects in the real world.
If we agree that our labours produce real impacts, we need to take better care to fully consider the wider consequences of our work, which often has the potential to cause ‘collateral damage’. We can’t build a road or a wind farm without changing the landscape. When we build a machine, it uses energy and may emit pollutants; and it reduces reliance on manual labour, which may put someone out of a job. There may be a risk to lives, livelihoods or the environment if something goes wrong.
Do we always make decisions about these matters with the community front of mind, or do we place our clients on the higher pedestal? This is a tricky area and I’m not espousing a puritanical approach. However, if we knew in 1919 what we know now about lead poisoning, acid rain, greenhouse gases, scarcity and general sustainability principles, what different choices could have been made?
In a time of automation, we need to think about benefits and risks and how they affect our communities. On one occasion early in my career, I designed a controller to turn on and off a couple of compressors at a power station. I wrote some code to balance the run hours. A few months after the new system was commissioned, I asked one of the operators how the system was going, in terms of the run hours management, and he said ‘you’ve done me out of a job’. I hope he was joking. The task he’d been doing wasn’t particularly important, but there was value in having a person who was in tune with the equipment to take care of it, and there was also value in giving that person dignity through work.
My point is that we must keep our communities foremost in our minds as we go about our work. It’s not just about what we produce. It is the way we work and the people we choose to work with and for. Our influence on the development of the next generation of engineers perhaps has more impact on communities than our actual work outputs.
Through communication, collaboration and community, engineering can be both ‘more human’ and ‘for humans’.
About the author
Donald Vaughan is Entura’s Technical Director, Power. He has more than 25 years of experience providing advice on regulatory and technical requirements for generators, substations and transmission systems. Donald specialises in the performance of power systems. His experience with generating units, governors and excitation systems provides a helpful perspective on how the physical electrical network behaves and how it can support the transition to a high renewables environment.